Industry perspectives on AI with Dale Tutt – Part 2
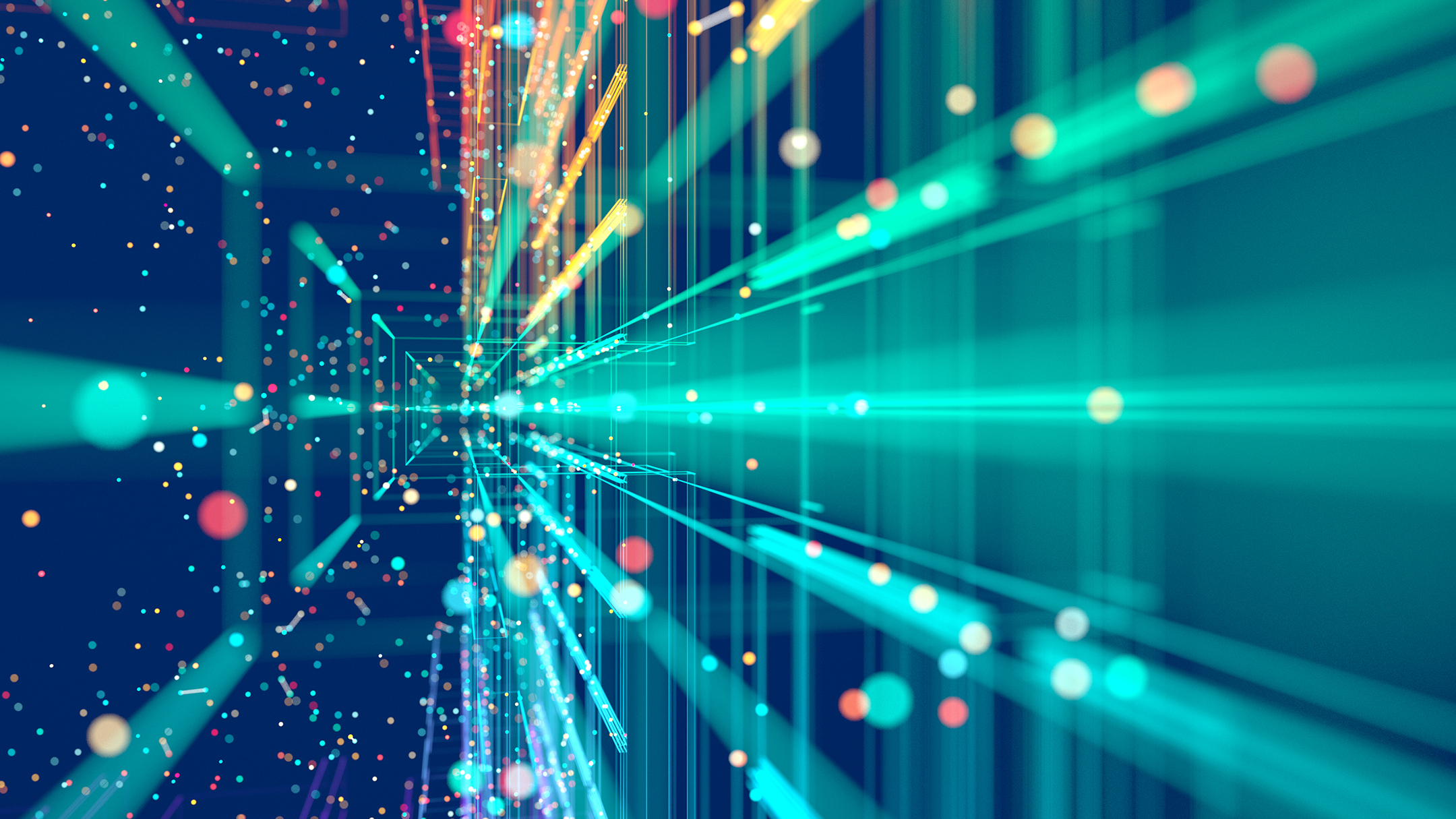
Continuing a conversation from a recent podcast (check out a summary of part 1 here), Dr. Justin Hodges, an AI/ML Technical Specialist and product manager for Simcenter, was joined once again by Dale Tutt, Vice President of Industry Strategy at Siemens Digital Industry Software to keep exploring the challenges and benefits of adopting AI in industry. Dale’s 30+ years of industry experience mean he’s seen many new innovations come and go, giving him a deep understanding of what it takes to bring new technologies from proof of concept to indispensable asset. Keep reading for some of the highlights of their conversation or click here to listen to the full episode, or click here for the transcript.
AI brings it all together
Data is one of the cornerstones of the digital transformation, building understanding and insight into processes and products and allowing optimization across a product’s entire lifecycle. However, when it comes to managing the dozens or hundreds of variables that make up a single product, a multitude of challenges quickly present themselves. Dale highlights the processes of ageing batteries and manufacturing carbon fiber composites which, beyond the actual chemical formulas themselves, are also highly sensitive to external variables such as temperature, humidity, and pressure. Optimizing these processes doesn’t just mean creating the best process for manufacturing the part itself, but understanding how changes in the initial stages of production will affect the part later in its lifespan.
AI and machine learning offer a way to do this, however. The relationship between these variables forms a complex, non-linear relationship often times with more variables than equations to relate them – the so-called curse of dimensionality. Justin says that, when it comes to situations like this, machine learning is an ideal tool for generating predictions and insights even without the ability to rigorously define the entire bounds of the problem. This makes AI an ideal tool to assist in optimizing the countless complex processes found across the manufacturing industry.
Building trust in new technology
As with any new technology, adopting it into real workflows can be challenging, and building trust within the userbase stands as a major hurdle. While AI technology today already offers many practical benefits to the design process, actually bringing it into the loop is another matter entirely as critical questions around trust and verification need to be answered first. While AI is still in the early stages of this process, Dale recounts his own experience with another technology that once needed to prove its place, but is now ubiquitous with the modern design process – simulation.
In all industries but especially those like aerospace, where every element of a design must be rigorously tested down to the smallest bolt, moving away from a tried-and-true method (building physical prototypes) to a new unproven one (computer simulation) can be a hard sell. Dale remembers how, at the time, when the simulated model revealed an issue the company he was working for decided on a dual approach, carrying on with the traditional prototype as well as developing a solution using the simulation. When the physical prototype revealed the same issue that the simulation predicted, they were able to quickly implement the solution already developed and stay on track. While it may seem wasteful in hindsight, by taking this approach it was possible to build trust in the simulated result so when it came time for another project, those results could be taken as fact rather than second-guessed.
AI is still at an early stage in this process, where most implementations will run in parallel with existing processes to validate results but, over time, as the AI models continue to generate accurate results, trust will develop in them in just the same way it has with simulation. Similarly, just like how simulation didn’t completely replace the use of physical prototypes, AI won’t completely replace the other technologies it’s competing with either. AI is a powerful tool for the digital transformation but it works best when used in conjunction with, not in place of, existing tools and methods, layering on new capabilities to enhance, accelerate and refine existing processes.
A bright future for AI
Just like any new technology, bringing AI into industry isn’t going to happen overnight, but through steady, long-term effort AI will find its place in the ongoing digital transformation happening across all industries. Despite how it might seem, AI isn’t going to outright replace existing jobs and processes instead serving as another valuable tool in the toolbox of engineering when it comes to designing new products and solving problems while lifting the burden of mundane and repetitive tasks from their shoulders.
To learn more, check out the full episode here and listen to all of Dale and Justin’s insightful commentary on the role of AI in the digital future.
Siemens Digital Industries Software helps organizations of all sizes digitally transform using software, hardware and services from the Siemens Xcelerator business platform. Siemens’ software and the comprehensive digital twin enable companies to optimize their design, engineering and manufacturing processes to turn today’s ideas into the sustainable products of the future. From chips to entire systems, from product to process, across all industries. Siemens Digital Industries Software – Accelerating transformation.