The renaissance of smart machines for future factories in 2024
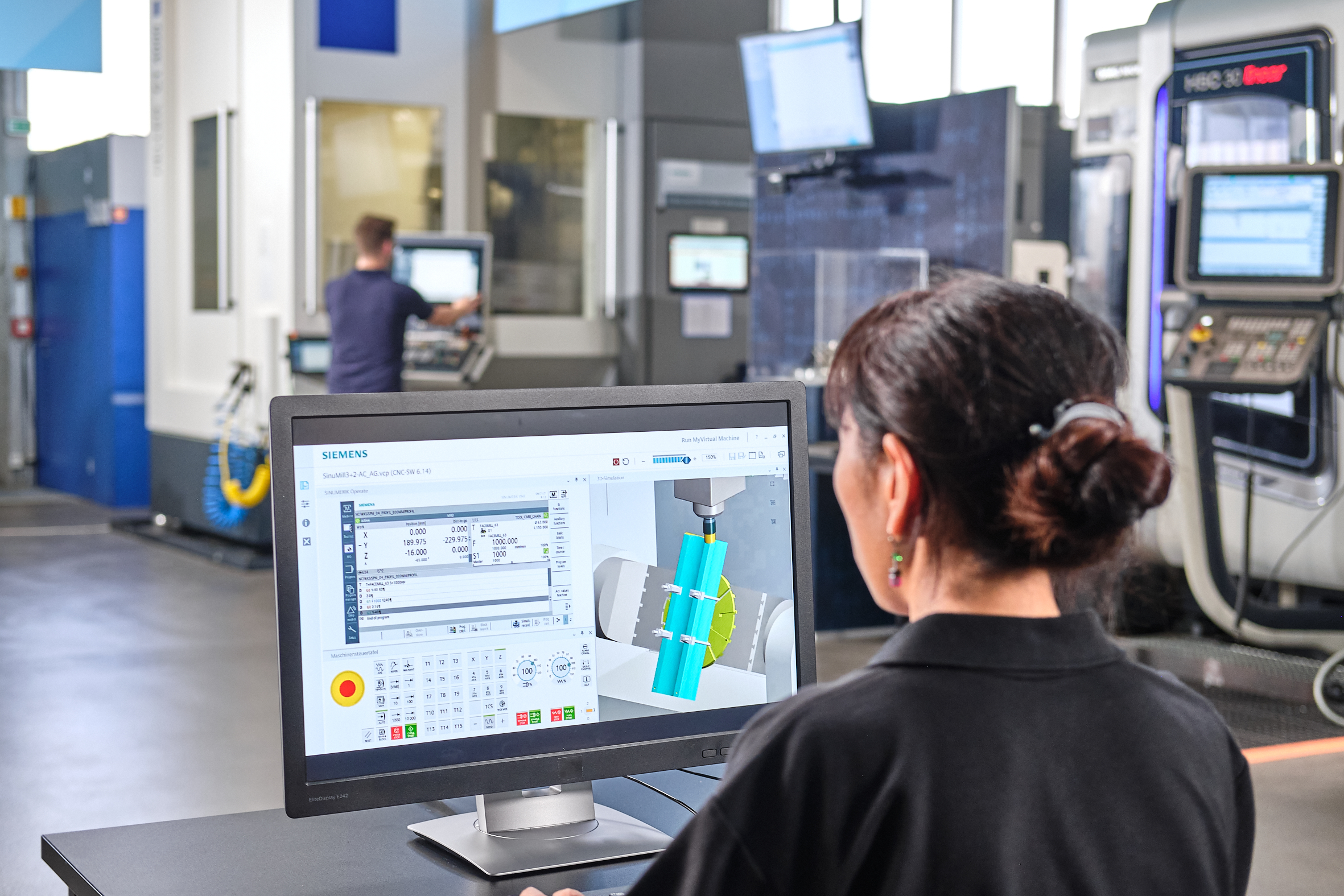
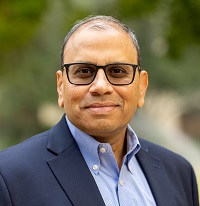
In a recent engineering.com article by Rahul Garg, VP for Industrial Machinery and SMB Program at Siemens Digital Industries Software, he discusses manufacturers’ many challenges, including a volatile market environment, driving them to adopt new ways to develop next-generation products.
Accompanying these challenges are quality, cost, performance, and sustainability demands. Areas are emerging for manufacturers, moving them from well-established domains into adjacent or new markets. Future factories are developing around sustainability, flexibility, and the future workforce. New technological advancements allow manufacturers to thrive, even with these industry challenges.
New capabilities are driven by significant intelligence via digitalization, providing an array of data that integrates digital tools, systems, and IoT data, connecting previously siloed information across design, engineering, production, and service.
“With digitalization, manufacturers can move beyond automation to more predictive and adaptive production environments. Adaptive manufacturing delivers the flexibility to enable effortless production switching with changing markets and customer needs. Moreover, it simplifies the workflow systems so manufacturers can do more with the same workforce,” says Garg.
Digitalization decreases manufacturing risk to provide flexible processes to access data across engineering and production disciplines. Previously from siloed disciplines, this data requires solutions built on an expert understanding of machine design, simulation, factory automation, and project lifecycle management (PLM).
The core of digitalization is the digital twin
The manufacturing renaissance requires digitalizing the complete lifecycle of the production process, including production machinery. It starts with the design phase – creating the smart machine’s digital twin. The machine’s digital twin is developed based on multi-disciplinary engineering that covers the machine’s mechanical, software, electrical, and automation systems.
In the past, the digital twin was used for design exploration and evaluation through a virtual prototype. Now, when a machine is ready for deployment, the digital twin will enable virtual commissioning before the machine is physically installed. This allows for familiarizing yourself with the machine and taking advantage of operator training to minimize the risk and time necessary for deployment.
Then, when the machine is installed in the factory, the machine’s digital twin is continually supplemented with data from operations across the machine’s lifetime. This creates a closed loop between the accurate and digital representation.
“With increasing fidelity, this operational digital twin delivers invaluable performance insights, enabling the manufacturing team to monitor and improve manufacturing efficiencies and quality continually,” says Garg.
A digital thread transforms manufacturing
Digitalization reveals new horizons for manufacturing.
“Robust digital twins of discrete machinery can integrate into a digital thread that extends from the individual machines to factory layout and design, then into manufacturing operations,” says Garg.
Plant-level simulation allows simulation across machines, automation processes and production lines, continuously optimizing speed and quality. Then, manufacturers can optimize the overall plant performance, beginning with planning and continuing operations. All this results in a smart factory with seamlessly accessed and shared data throughout the operation.
Enablers such as sustainability, production flexibility, and labor shortages provide more sustainability with energy management, production flexibility, and human-machine collaboration via AI, machine learning, and data analytics.
Additionally, a digital thread significantly minimizes risk when converting or modifying the line to adapt to fluctuating market conditions. As you connect to the physical world digitally, cybersecurity must be prioritized and integrated into all aspects of digitalization.
“With digitalization, machine builders can confidently embrace an innovative future,” says Garg.
Learn more in the article.
Siemens Digital Industries Software helps organizations of all sizes digitally transform using software, hardware and services from the Siemens Xcelerator business platform. Siemens’ software and the comprehensive digital twin enable companies to optimize their design, engineering and manufacturing processes to turn today’s ideas into the sustainable products of the future. From chips to entire systems, from product to process, across all industries. Siemens Digital Industries Software – Accelerating transformation.
For more information on Siemens Digital Industries Software products and services, follow us on LinkedIn, Twitter, Facebook and Instagram.