Reaching Closed-Loop Optimization Part One – Summary – Talking Aerospace Today
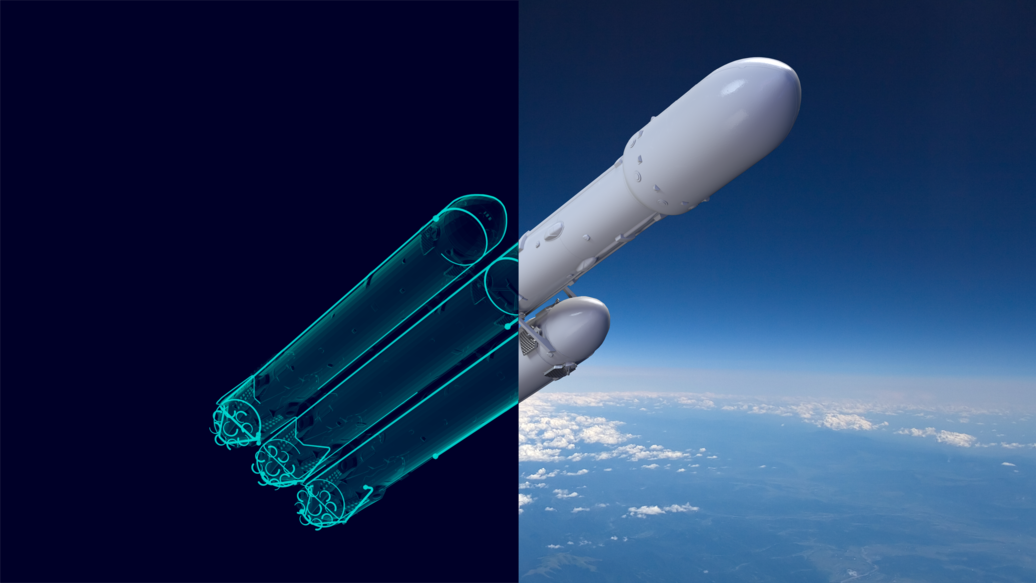
Since July of last year, the Talking Aerospace Today podcast has been focused on the five stages of digital transformation maturity, a framework companies can use to determine where they are in their digital transformation journeys. Now, after exploring why the aerospace and defense (A&D) industry could benefit from digital transformation maturity, the role AI will play in it, and the stages of automation and generative design, the podcast has reached the final stage in this journey: closed-loop optimization.
In the latest episode of Talking Aerospace Today, Todd Tuthill, Vice President of A&D for Siemens Digital Industries Software, is joined by Thierry Olbrechts, Director of the Aerospace Industry Solutions Simcenter Simulation and Test Portfolio for Siemens. Together, they introduce the problems closed-loop optimization is meant to solve, how it fits into the digital transformation maturity framework, and how digitalization efforts today have paved the way for its adoption.
Closed-loop optimization and time
One of the biggest problems digital transformation maturity as a whole addresses, according to Todd, is time. Designing an aircraft or spacecraft is a time-consuming process, consisting of numerous decisions that can impact multiple engineering domains. Previous episodes have discussed how earlier stages of the framework help with doing more in less time. For example, automation delegates mundane tasks away from engineers so they can focus on higher-level work, and generative design does something similar by automatically generating engineering artifacts.
A notably large factor that Todd finds taking a lot of time in engineering workflows is fighting against suboptimization. During his previous experiences in the industry, Todd had often come across plenty of instances where engineers on different teams, such as mechanical and electrical teams, work in parallel, optimizing their respective systems in isolation from each other. These engineers end up struggling to adjust their systems to work in concert but might not finish due to time constraints, resulting in a suboptimized product.
This is because at the end of the day, engineers need to ship products that make money. With so much time spent working on systems in isolation, then working to make sure those systems work together, there is little time to optimize the aircraft or spacecraft as a whole. This also prevents engineers from increasing the amount of design iterations they can explore, potentially losing out on making the most optimized variant.
Closed-loop optimization is meant to remedy this problem by automating those interconnected design decisions through repeated self-evaluation based on a set of key performance indicators. After all, if generative design can automate the creation of an engineering artifact once, there is no reason the artifact can be fed into a simulation, and the same algorithms or AI can optimize the artifact based on the results. Whereas engineers could create a dozen iterations of a product in traditional workflows, closed-loop optimization can result in iterations numbering in the hundreds or even thousands.
Primed for optimization
While the A&D industry has yet to enter the advanced stages of digital transformation, Thierry highlights how digitalization has already transformed the industry in ways that can enable the adoption of closed-loop optimization.
Take the space sector. Back in the 1960s, the Apollo program employed a total of 400,000 people across its workforce. Today, the capabilities of today’s engineers are expanded thanks to digital technologies such as computer-aided design (CAD) and simulations that can bridge isolated engineering domains and identify problems early. Now many modern space programs only need ten to fifteen thousand people to do the same amount of work. The impact of digital transformation in the A&D industry is very real.
Despite these improvements, however, many aerospace projects today take longer than they did back then. The Apollo program was able to put humans on the moon just seven years after President Kennedy announced that intention in 1962. Meanwhile, according to Thierry, new aircraft programs can take as much as ten or eleven years to enter service. A&D companies are very eager to overcome this issue and reduce their times-to-market
Between this desire and the continuing advancement of digital technology, closed-loop optimization is primed to fit right in with the digital transformation of A&D. It will still take some time to reach such a level, but as long as companies continue investing in their digital transformation journeys, the payoffs can be astronomical.
Stay tuned for the next episode of Talking Aerospace Today for the conclusion of this conversation on closed-loop optimization.
Siemens Digital Industries Software helps organizations of all sizes digitally transform using software, hardware and services from the Siemens Xcelerator business platform. Siemens’ software and the comprehensive digital twin enable companies to optimize their design, engineering and manufacturing processes to turn today’s ideas into the sustainable products of the future. From chips to entire systems, from product to process, across all industries. Siemens Digital Industries Software – Accelerating transformation.