Behind the scenes at Siemens’ Bad Neustadt factory: IT/OT convergence
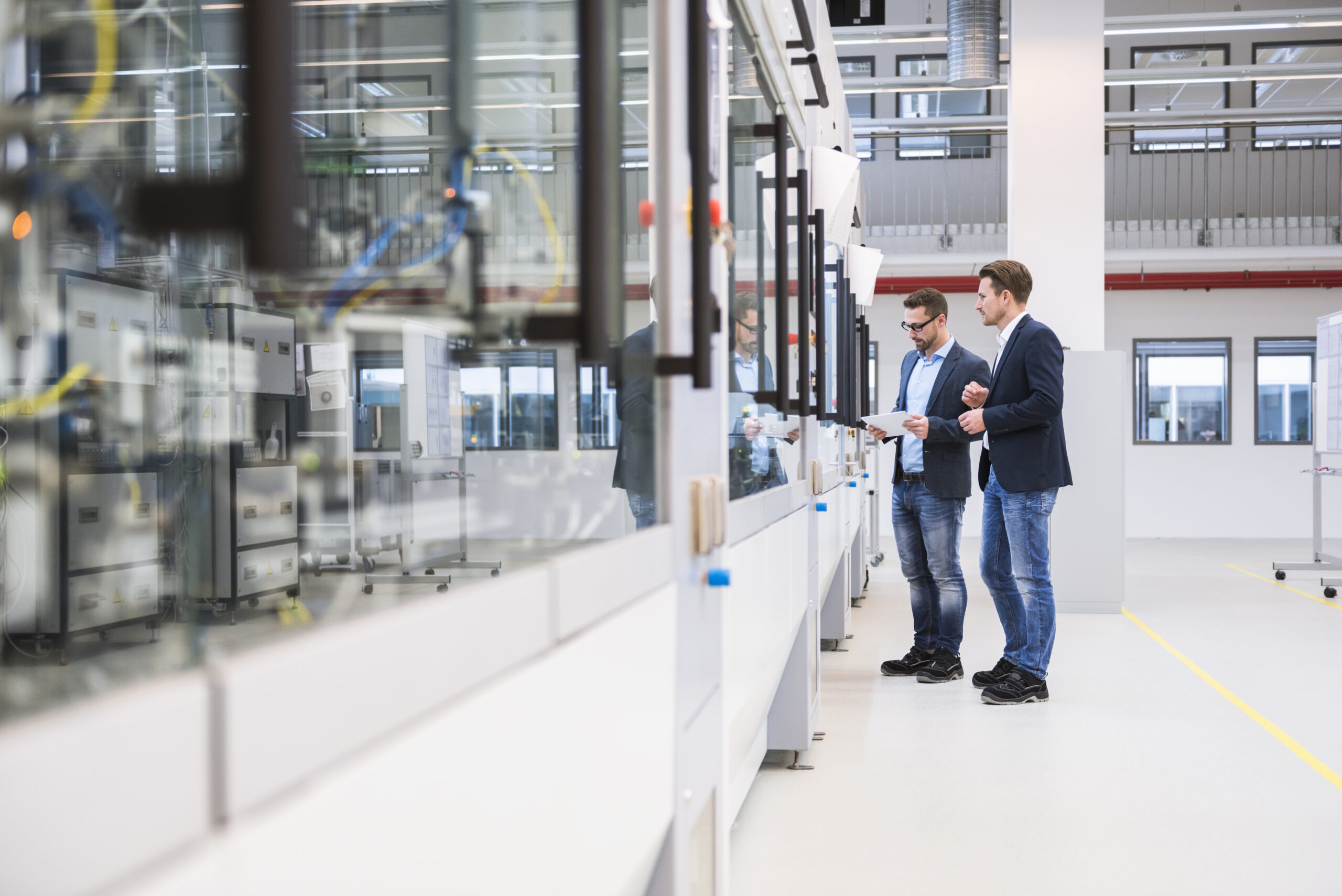
In today’s ultra-competitive and complex manufacturing landscape, organizations are beginning to recognize that IT/OT convergence delivers a significant advantage over competitors. By fusing IT capabilities with OT functionalities, manufacturers can access data that drives operational excellence, enhances decision making and reveals opportunities for innovation and optimization.
Discussing the potential advantages of IT/OT convergence for an organization is one matter, but implementing it is entirely different. That is why Siemens electric motor factory in Bad Neustadt is taking the lead in bringing IT/OT convergence into its very own factory operations. The factory is undergoing a digital transformation, moving from manual assembly towards flexible automation.
The crucial distinction: IT vs. OT
To appreciate the significance of IT/OT convergence, it’s essential to distinguish between the two domains:
- Information technology (IT): IT is the brains of the factory. IT resources include the organization’s computer information technology stores, which analyzes and processes operational data which can then be translated by workers to make insights-based decisions. IT technology is fast, scalable and data-driven based on modern software design practices.
- Operational technology (OT): OT is the foundation of the factory. It has long relied on proven, legacy systems that interface with factory level hardware including factory equipment, programmable logic controllers (PLCs) and the technology that powers machinery.
Historically, these realms have operated in silos, with OT focusing on reliability and IT on adaptability. Moreover, they’re staffed by workers with completely different training and skillsets. However, with the ubiquitous adoption of IIoT (Industrial Internet of Things) devices and smart technologies in factories, the once clear delineation between IT and OT is progressively fading. Organizations are realizing that IT has the power to enrich existing OT functionalities leading to benefits such as:
- Closed-loop optimization
- Supply chain resiliency
- Enhanced sustainability efforts
- Holistic cybersecurity concepts
These benefits will enable manufacturers to make their production processes faster, more sustainable and increasingly autonomous.
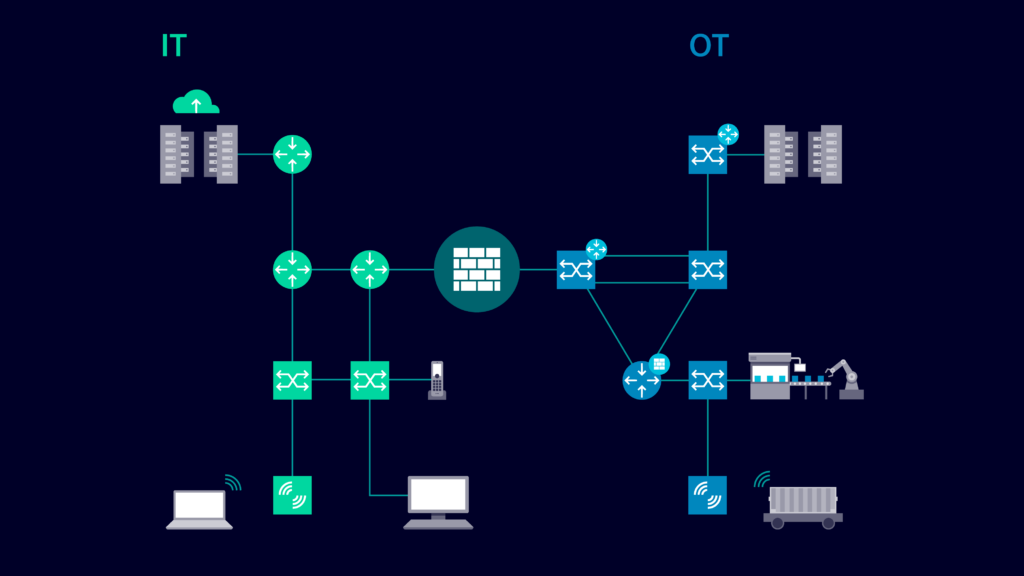
IT/OT Convergence becomes a reality
The Bad Neustadt factory produces multi-axis electrical motors for Motion Control Drive systems—a high variance and high-volume production achieved through a Make-to-Order approach. This highly individualized method produces 500,000+ configurable variants for customers per year. In fact, they estimate that the factory changes the product setup process every seven minutes on average and is approaching being a lot-size of one factory where everything is made to order. To keep pace with this incredible demand, factory management at Bad Neustadt must continuously refine their production processes to meet client expectations and maintain competitiveness.
Furthermore, their factory target is “modular automation by using autonomous material transport and AI applications on the shop floor.” They aspire to implement a manufacturing process that is both flexible and dependable, leveraging automation and artificial intelligence (AI) to enhance efficiency and decision-making from shop floor to top floor—with IT/OT convergence as the key enabler to achieve these aggressive objectives.
Their goal is simple: to become a data-driven factory, making decisions based on automatically collected and visualized data.
A use case driven strategy
To begin their IT/OT convergence journey, the Bad Neustadt factory initially established an OT-centric ecosystem, connecting crucial sources of factory information to lay the foundation for integrating IT and OT. This enabled the collection of data from previously isolated sources on the shop floor such as sensors, machines and controllers as well as end-of-line tests and QA. All this is combined in a data lake with specific interfaces from our enterprise resource planning (ERP) and manufacturing execution system (MES), added further capabilities for data storage and data processing to the ecosystem.
All this data is then uploaded to provide the crucial information for various IT processes that will generate more insights—such as visualization, data analytics and AI. Blending these two worlds facilitates the execution of various use cases that depend on data from both domains.
However, as the data amount increases, data structures become more complex and can jeopardize the data’s quality. Their solution? Selectively onboard data for a particular use case so domain experts and data engineers work cross functionally with the data, further guaranteeing data quality. In essence, they use data to identify use cases and then employ those use cases to capture and filter future data. This cyclical process forms the core of IT/OT convergence, resulting in an ever-more efficient addition of use cases for optimizing factory machines and processes.
One major use case is streamlining anomaly detection for end-of-line testing. Referred to as a “reduced test effort”, it entails using historic data to derive rules for determining if a specific motor needs to be tested. The goal is to minimize testing without sacrificing the quality of the motors shipped. By applying AI algorithms, they can calculate the number of tests needed for a specific motor configuration. Combining historical data with real-time information from the factory floor, the intelligent algorithm dynamically defines the number of tests, resulting in reduced time and money spent on testing. In fact, the EWN achieved 16% less end-of-line tests for motors.
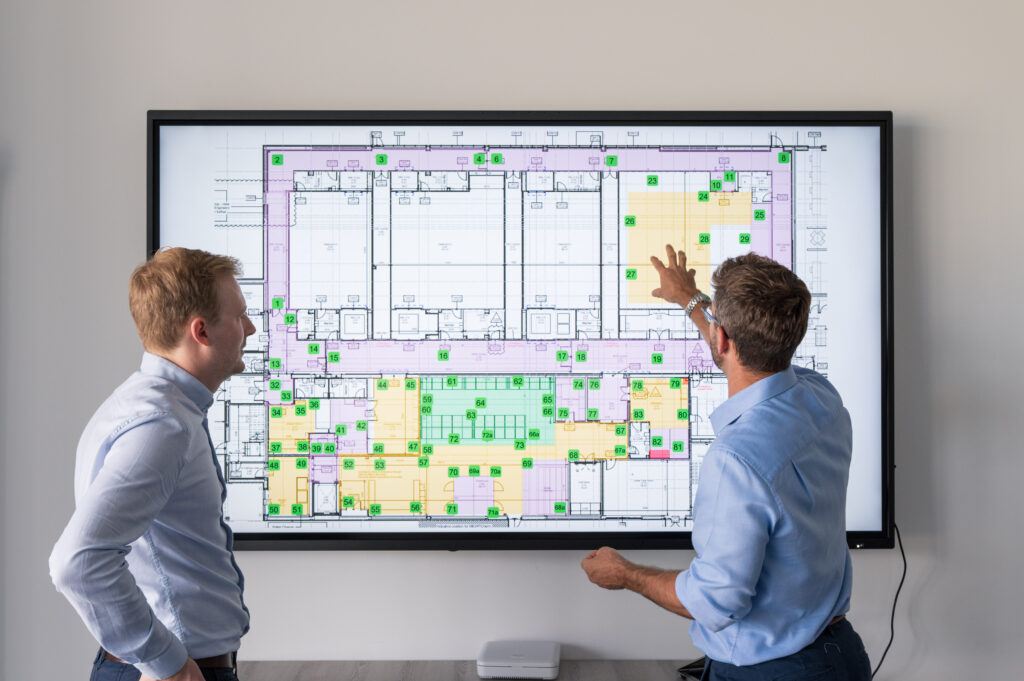
Bad Neustadt experiences the benefits of IT/OT convergence
Though the factory is still in the implementation and learning process, they are already experiencing how IT/OT convergence translates into tangible benefits on the shop floor:
- Verification of process times: Through the implementation of digital cycle time management, the factory has successfully improved the master data quality and identified potential areas of process improvement.
- Sustainability: With data captured by sensors and machines, the factory has been able to establish energy data monitoring which allows decision makers to reduce energy waste in a target-oriented way. Not only is this an enormous advantage in an era heavily concerned with the sustainability of operations, but it also yields cost savings.
- Automation: IT/OT convergence enables the automation of time-intensive tasks. For example, through the establishment of an automated data pipeline, one domain expert was able to save hours of data processing per week—enabling them to work on other critical tasks.
- Optimizing testing processes: As mentioned above, using data from the factory’s MES and edge technology allows the factory to skip certain test steps based on statistical evaluations. This enhances their operations, enabling them to fulfill customer demands more quickly.
As the implementation progresses and data continues to lead to better insights, the team is adding more use cases that will further contribute to the overall efficiency and success of the factory’s operations.
Continuing IT/OT convergence
Looking forward, the Siemens factory in Bad Neustadt plans to scale their IT/OT convergence efforts. The goal is to become a data-driven factory reliant on automated data collection and visualization. To achieve this, they are becoming more proficient at developing use cases by adopting the necessary technologies, training their teams, onboarding more data and refining their standards. This will enable them to scale using quality data sets and an extended data ecosystem.
Overall, this Siemens factory is a model of success for our customers, tangibly demonstrating how the strategic integration of IT and OT can empower a smarter and more flexible future for manufacturing.
Interested in learning more about IT/OT convergence in manufacturing? Explore our ebook for insights on how IT/OT convergence can help leverage data, reduce emissions and enhance operational efficiency.
Download the ebook here.
Siemens Digital Industries Software helps organizations of all sizes digitally transform using software, hardware and services from the Siemens Xcelerator business platform. Siemens’ software and the comprehensive digital twin enable companies to optimize their design, engineering and manufacturing processes to turn today’s ideas into the sustainable products of the future. From chips to entire systems, from product to process, across all industries. Siemens Digital Industries Software – Accelerating transformation.