Reaching Closed-Loop Optimization Part Two – Summary – Talking Aerospace Today
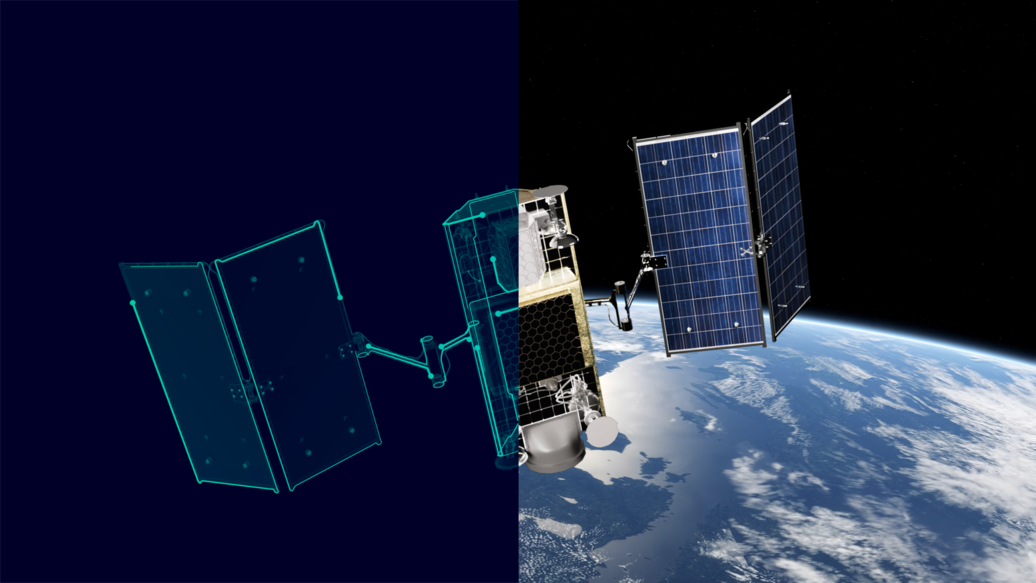
The aerospace and defense industry (A&D) has been on the path toward digitalization for a long time, and has made great strides. The process of digital transformation maturity, as discussed in the Talking Aerospace Today podcast, promises to help companies build on those strides to achieve new capabilities once thought impossible. Closed-loop optimization, the automatic self-evaluation of engineering processes and the final stage of digital transformation maturity, can be especially critical to bringing the industry to new heights.
In the latest episode of Talking Aerospace Today, Todd Tuthill, Vice President of A&D for Siemens Digital Industries Software, is joined again by Thierry Olbrechts, Director of the Aerospace Industry Solutions Simcenter Simulation and Test Portfolio for Siemens. They continue their conversation on optimization from the previous episode, expanding on its application across the product lifecycle, the reasons why A&D companies should adopt it, and why they should start investing in optimization capabilities now rather than later.
Optimization across the lifecycle
While the focus of digital transformation maturity in previous episodes has been centered around aerospace design, the reality is the five stages can be applied across the product lifecycle, and closed-loop optimization is no exception. According to Thierry, a digital twin can be created for any phase in the lifecycle, whether it is the manufacturing process or the product in service, which can collect data in real-time that can be used to run simulations. These simulations could then be used to create new iterations of the product and the workflows surrounding it.
This can result in continual optimization that runs both during and after design, ensuring products are being optimized at all times. For example, the digital twin of a spacecraft in operation can be monitored to ensure its systems are working nominally or if there are defects aboard. That information can then be fed back to the digital twin and be correlated with data gathered by simulations to inform future iterations of that spacecraft that will not experience the same problems. Optimization works not just for the products of the present, but also for the products of the future.
Why is optimization necessary?
There are two significant reasons closed-loop optimization should be adopted in A&D engineering processes, the first being risk reduction. Aerospace products operate in some of the harshest environments known to humanity, and if something goes wrong, help will often be too far away to arrive on time. This is doubly so for spacecraft, especially those that go on missions to the Moon, Mars, or beyond. Therefore, problems must either be able to be solved immediately aboard the aircraft or spacecraft, or be anticipated beforehand and accounted for in its design. By taking data from simulations and active operation to influence its design decisions, closed-loop optimization tools can help make the best iteration that enables both.
The second major reason is to streamline increasingly complex engineering processes. Todd mentions how thousands, perhaps millions of decisions were made across the Apollo program’s lifecycle, for example, all by human beings. As today’s aircraft and spacecraft integrate new technologies and systems, the number of those decisions are bound to increase tenfold. This is not sustainable in an industry facing a growing worker shortage where one in five positions are expected to be unfilled in the next decade. Closed-loop optimization tools can take the burden of swathes of smaller decisions, letting human workers focus on higher-level engineering and accelerating their workflows.
Optimize aerospace today
It will still be a long time before the A&D industry reaches a level of closed-loop optimization that can effect decisions for a whole aircraft or spacecraft like Todd alludes to, but the capabilities that can build toward that goal exist today. Simulation and optimization tools exist in current engineering software, albeit limited to single engineering domains rather than incorporating data from multiple. Yet they are continually being innovated upon with each passing day, and recent advancements in artificial intelligence and machine learning present opportunities to advance them in ways that were once unheard of.
If companies wish to receive the full return on investment from closed loop optimization and digital transformation maturity, investing in and building on those capabilities now would enable them to grow alongside the technology as it grows. This would let them reap its benefits immediately, leading to a new generation of aircraft and spacecraft optimized to perform at their very best.
Be sure to listen to the rest of Talking Aerospace Today’s episodes on digital transformation maturity, and stay tuned for new episodes on other exciting topics.
Siemens Digital Industries Software helps organizations of all sizes digitally transform using software, hardware and services from the Siemens Xcelerator business platform. Siemens’ software and the comprehensive digital twin enable companies to optimize their design, engineering and manufacturing processes to turn today’s ideas into the sustainable products of the future. From chips to entire systems, from product to process, across all industries. Siemens Digital Industries Software – Accelerating transformation.