Simulation for industrial systems-ep. 2 transcript
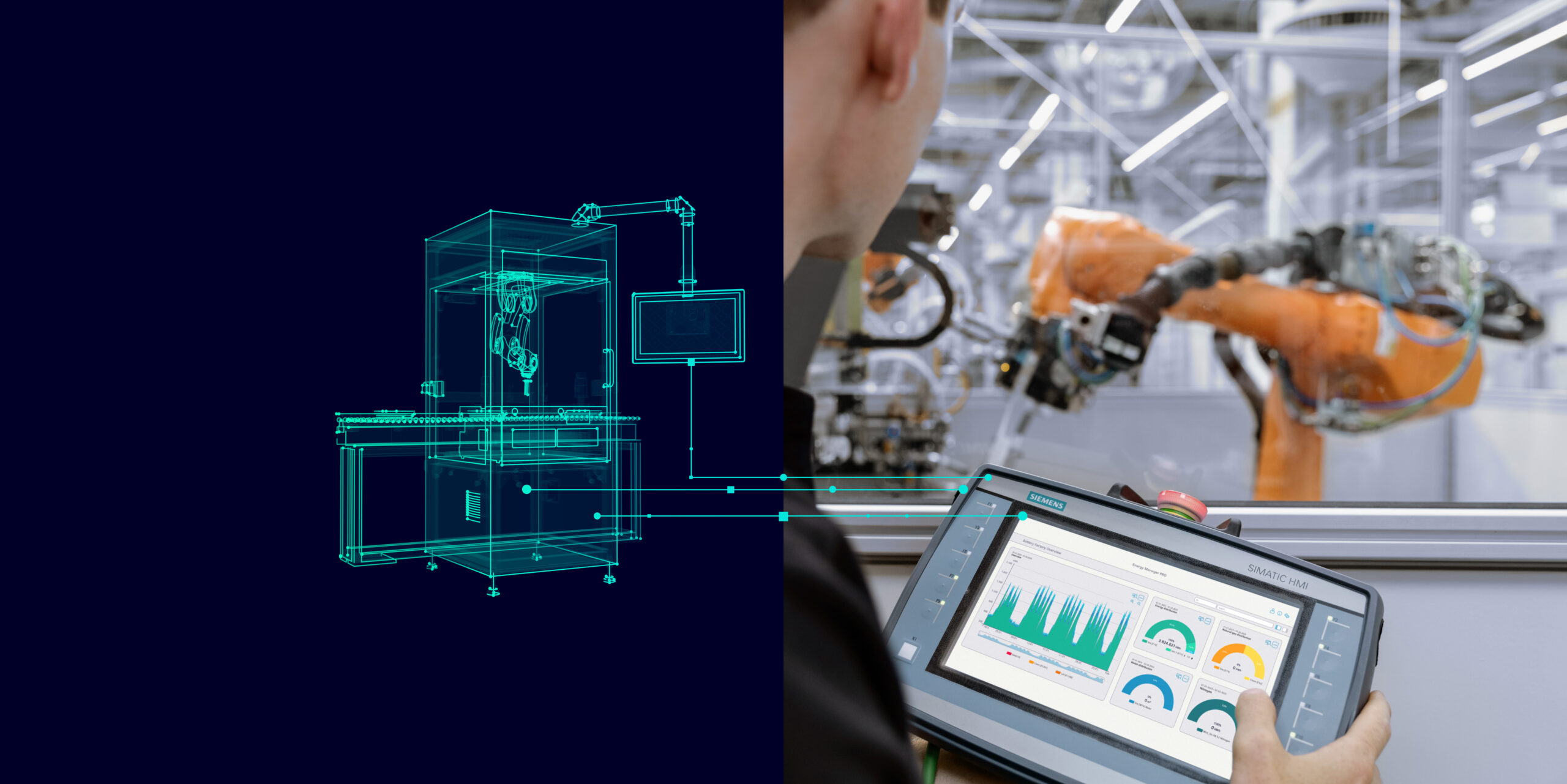
Victoria Carlos: Hello everyone and welcome back to part two of our simulations in industrial systems podcast. In this episode, Rahul Garg and Dominic Zettler discuss how manufacturers can leverage digital tools like the executable digital twin to track real-time developments in their factories. They will also cover best practices for ensuring operations stay cyber-secure. In addition, they delve into the exciting and promising future industrial machinery with technological advancements like the industrial metaverse. We hope you enjoy the show.
Rahul Garg: Dominic, can you talk about how companies can use simulations for industrial systems for things like production planning, capacity planning, facility location planning, and forecasting? How can this simulation topic be further expanded in a production system?
Dominik Zettler: Thanks for the question. We mainly talk about how the first use cases typically deal with machine throughput, system buffers, how much equipment is needed and so on. This is the basic functionality of what we have on the planning side. We can simply start simulating the throughput offline by utilizing simulation. The interesting part is if we use theoretical values to simulate your throughput, later on you will have a much clearer view of the lifecycle of the machine.
From there, you can improve and update your first model with additional data and have a much more precise model. Depending on how your plant behaves, the third step would be simulating the conveyors or ATV fleet management. We also need to control the material flow with automation, with maybe a MES system so we can see what is happening. Is it getting into my systems? Is my plant working? And so on.
Step by step we can enrich my model and make it more and more precise. We can find which data could improve it and build on it.
Rahul Garg: This is where we went to talk about the whole idea of closed loop optimization, right where you are now beginning to get a real production throughput number and using that as input into your virtual models to see how things could be further optimized based on the real numbers and what changes you could make into your production system before actually making a change. You can evaluate the change. You can evaluate the impact of the change.
How could the change be executed before you actually make a change in the virtual model? You make sure it’s right and then you can optimize your production systems going forward. It becomes a lot more effective way to further leverage the simulation systems in your real-world production as well. I think that this is very good.
So, Dominik we spoke about the closed loop optimization a while ago, which is a way to further evaluate the impact of a change and how to make a production system perform better. There’s another new emerging topic that is that is coming into the industry about an executable digital twin. Can you speak a little bit about that and the value and the impact that this can have in the industry?
Dominik Zettler: Yes, we mostly talked about the planning phase before. Now, we are going to talk about the customer side. Using real data, we can create a closed loop. We can now connect the shop floor while utilizing simulations models to perform what if scenario. What if I maintain this machine next week? How can I improve my production next week? These new scenarios are executable. The executable digital twin is really running in real time during production. It’s not a separated simulation model like we have in engineering and planning phase. What if scenarios in the executable digital are embedded in the process itself. Here we have totally new use cases. At the moment I have no clue how many ideas will come in the next years because we are just starting with this journey.
If we imagine a simple use case, think about virtual sensing. It is one simple example of the executable digital twin. We can embed a simulation model of a heat exchanger when normally we couldn’t have a sensor there. It’s tricky to control the process, but with the simulation model can really visualize the system and the energy consumption in real time.
And as we mentioned before, this is where sustainability comes into play. We can simulate energy input to reduce the energy we put into the system. And the customer can take advantage of his for a lifetime of the machine and generate value from the executable digital twin.
The twin in this case would be heavily supporting your sustainability goals and it’s really easy to apply. We (Siemens) can do it already with real time simulation models in operations.
Rahul Garg: Yes, the executable digital twin will see explosive growth as customers begin to understand the value of being able to change in real time certain functions and certain parameters of some equipment or for line or something. And real time changes can be happening because of various reasons.
You just mentioned temperature inside a heat exchanger. It could be because of the weather conditions where the machine is running and the humidity on the shop floor can have an impact and you’re trying to control that. There are a lot of real time implications that can be that can happen in a production environment. And if you can take advantage of this capability, it can help you further fine tune your production process, further optimize your production process and get more value.
This is certainly an area where we see a lot of more growth around this whole topic of executable digital twin.
Dominik Zettler: I want to one mention one more topic. In this executable digital twin, the machine builder will have the model of the machine in real time know how it should behave. The machine would have been modified and optimized to run in real time in parallel to the real machine.
This can be used for anomaly detection. A difference in behavior may have early implications for maintenance or performance of the machine. And maybe we could also go back to closed loop, optimize the machine again, and deploy a new digital twin. This is a very valuable process. You can say that you utilized what you did in the engineering phase and bring it to the shop floor. Then you use the machine for its entire life cycle, and you’ll be able to see how the machine should work, where the deviations are, etc. From our customer’s side, they’ll be able to see the modern possibilities.
Rahul Garg: Yes. The executable digital twin can, as you said, be used for not only improving the performance but also getting some early indications of some maintenance needs. Some preventative maintenance needs, etc. The twin can really help our customers improve down the road on their usage of their machines as well.
Dominik Zettler: Exactly. If you start the journey with us, and use our tools, additional business models become available and bring additional value. You’ll be more competitive and/or bring additional value to your customers. I think this is the main focus. We need to show our machine line builders and other customers that we are the right partners to fulfill all those use cases along the entire life cycle, from the idea till end of production.
Victoria Carlos: When we’re talking about smart manufacturing in the advent of new technologies, especially in executable digital twin, security ends up being a really big concern for companies. So, my question is, what can OEMs do to ensure their operations remain protected when utilizing simulation software?
Dominik Zettler: Security is a crucial topic. We see that cybertheft is rising. Cybersecurity is a standard topic for the OT since it is normally protected. Still, we need to ensure that the models we bring into productions are also tested and validated, and we also need to educate our customers on how they should deliver their models. They need to know they can rely on models that we bring into production, that they are cybersecure and tested before they run in production. At the moment, most of our executable data twins run on our industrial edge platform.
This means that you can prevent outside attacks and that you have closed applications running on the machines and on the shop floor to avoid any incidents. The customer or the supplier can make sure that the models in their lines have no possibility that somebody else is deploying something which is not permitted from the operator.
Rahul Garg: That’s a good point. Bringing in IT and OT security systems together can help provide a much more secure environment from a cyber-attack perspective. And the other area I would say that perhaps the gets further exemplified is leveraging SaaS and cloud capabilities. Today our SaaS systems and cloud technology providers, especially the high per scalars, companies like Amazon and Microsoft and Google have really tightened their security capabilities where even large government enterprises like NASA and the US Air Force are beginning to use them for their own purposes.
From a security perspective, the levels of capabilities have increased so significantly through bringing in cloud technology, as well as IT and OT convergence. Because of these, security gets extremely well addressed.
Dominik Zettler: Absolutely. It’s very clear that we are collaborating with the big vendors. We are collaborating with Microsoft. We are collaborating with AWS, sometimes Google Cloud as well because they have their systems under control. We would not go with a small vendor because their security would not fulfill our needs. When it comes to SaaS, cloud, or even hybrid SaaS solutions we always rely on the big suppliers so we can ensure cybersecurity. Whether its engineering or operational software like industrial edge, we can always trust larger suppliers. That’s a very fair point, Raul.
Victoria Carlos: We’ve spoken a lot about how simulation for industrial systems can optimize operations today, but I want to ask, how do you envision the future of industrial simulation evolving, especially in light of advancements like the industrial metaverse?
Dominik Zettler: That’s very cool topic. I say we need to rely on the speed of our customers. For us, it’s still a journey full of possibilities. What we can imagine, but the first step is the digital twin, which Roland Busch presented at CES. The second step is software defined automation. And the third step was data and AI. And within all those topics, we see the executable digital twin. It’s already both data and simulation and it simulates mechanical, physical, and electrical behavior. We bring additional capabilities with immersive-ness, with a collaborative room there more partners can collaborate. This is the next logical step in the evolution from the journey.
I’m curious about what we will see in the future. Siemens is one of the only companies dealing with the industrial metaverse because we have all the building blocks in our pockets. It’s getting them together, making it comprehensible, and working together with our customers on their journey.
Rahul Garg: Yeah, I would say with the industrial metaverse, which is certainly a very exciting topic, is applying the metaverse, which was thought of to be a consumer topic, to the industrial world. And this is where leveraging some of the comprehensive digital twin technologies and the software driven automation and other capabilities is helping us drive improvement in efficiencies in manufacturing and engineering, and even in field service.
It really helps us bring the really detailed comprehensive digital twin to the physical world and that’s where you need strong computational power of back-end systems to enable these systems to be working together to give you a real time simulation. And that’s where even our partnership with NVIDIA becomes essential.
NVIDIA is a market leader in the whole issue of processing systems and the back-end system GPUs. They offer the kind of horsepower you need to create this industrial metaverse. We really think that this will help many of our customers on the leading edge to push the boundaries of technology for adoption in their manufacturing systems.
Dominik Zettler: I like your wording. Push the boundaries. It’s the next step in the in this whole evolution. And you mentioned already beforehand that we can include environmental data into simulation. This is a very massive topic in the industrial metaverse.
I know already my supply chain. I know my ship is in a storm in the Indian Ocean. How? What implications will this have on my production lines? How will I need to improve my scheduling system? Maybe now because I know the material is missing, so I take my model and make it do operator training.
That’s why I’m always saying these systems are simply the next evolution.
Victoria Carlos: Thank you both. And you know, today’s conversation has been really great, but before we close out for the day, are there any final thoughts you want to leave our listeners with?
Dominik Zettler: Our customers have different maturity levels. It’s important that we convince our customers to start with the journey. Sometimes they will go at different speeds, or they start with simpler use cases. We (Siemens) have a bunch of possibilities already. So, my message is that Siemens is the right partner with all the possibilities and can start the journey with the customers wherever they are.
Rahul Garg: Yeah, this is an extremely exciting journey. The capabilities that have now matured from a technology perspective have become front and center and in all production systems. Companies that are in the business of manufacturing things can really turn the corner and they will find something that they can start taking advantage of. As Dominic mentioned, think of it as a maturing step. You don’t have to get everything done day one but start the journey as soon as possible and Siemens can be a great partner for you.
Victoria Carlos: Thank you so much for tuning to our podcast on simulations for industrial systems. Stay tuned for new episodes on our digital transformation podcast series. We hope you enjoyed, and we’ll see you again next time.
Siemens Digital Industries Software helps organizations of all sizes digitally transform using software, hardware and services from the Siemens Xcelerator business platform. Siemens’ software and the comprehensive digital twin enable companies to optimize their design, engineering and manufacturing processes to turn today’s ideas into the sustainable products of the future. From chips to entire systems, from product to process, across all industries. Siemens Digital Industries Software – Accelerating transformation.