Strategic technology enables closed-loop approach to quality
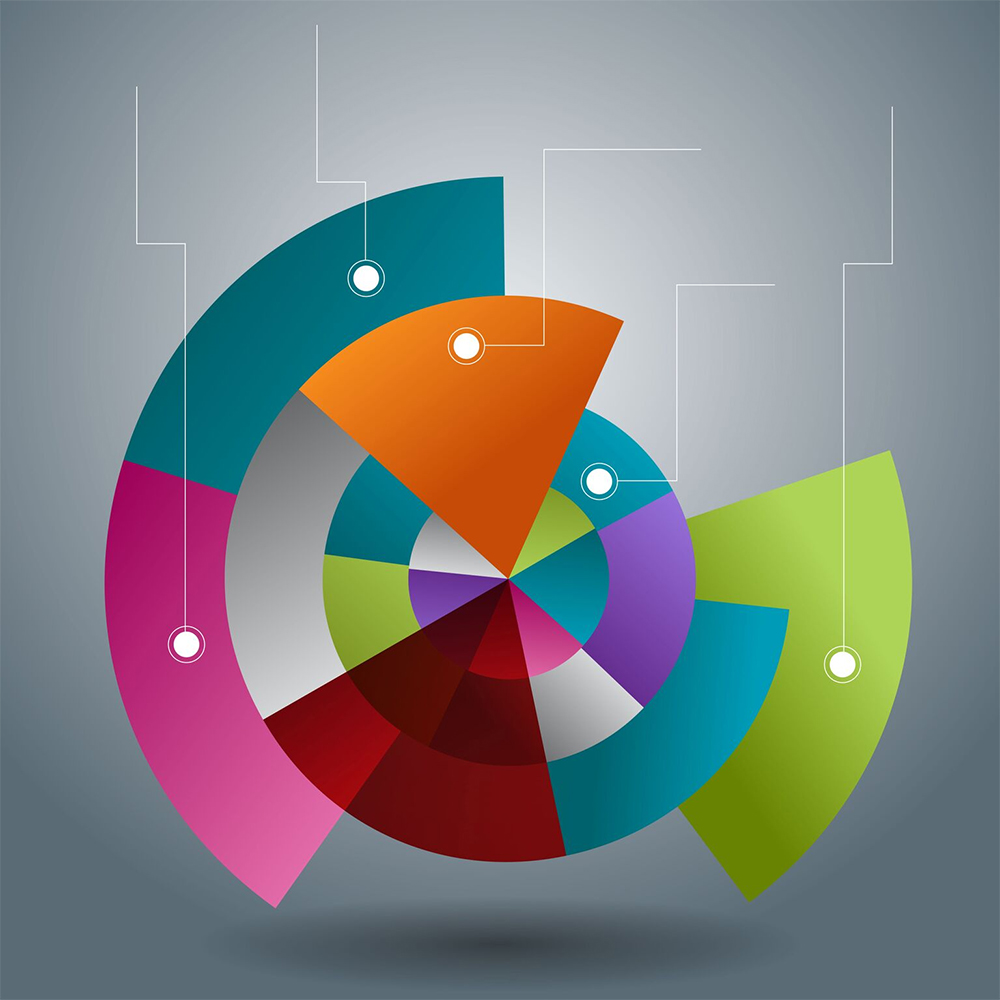
Recent reports from two prominent research firms have identified a new appreciation for quality in manufacturing. The new view heralds an approach dubbed closed-loop quality, which itself is overseen by a robust, end-to-end digital quality management system. What’s driving this new approach?
Market dynamics that have arisen from globalization and digitalization.
In the report Quality in the Future of Manufacturing, Frost and Sullivan asserts that increased digitalization within manufacturing industries, combined with increasingly competitive business, “make a compelling case for a holistic quality management approach in discrete industries.”
LNS Research focuses on quality’s impact in product innovation. Its surveys show that, of manufacturers that include lessons learned from prior product generations in new product development, 89 percent rely on data from quality management systems. It adds that, “The market is broadly emphasizing the importance of NPI [new product introduction] to revenue growth,” with some segments indicating that “NPI is anticipated to contribute more than 50 percent of new revenue in the next 12 months.”
As quality becomes more critical to manufacturing success, companies are turning their digitalization efforts toward streamlining quality practices, while at the same time integrating quality more tightly with functions across the manufacturing supply chain. They’re finding that QMS is doing for quality what advanced systems have done for new product development and management. This includes:
• Enabling quality to be a strategic function, rather than tactical or department-level function
• Building an integrated, closed-loop approach to quality from design and manufacturing through delivery and service, which includes quality components such as critical characteristic definitions, control/inspection plans and corrective actions
• Elevating quality to an all-encompassing effort involving not just product and process quality in execution, but as integral to meeting the brand promise and customer expectations
Why automate quality?
The reasons for quality’s increased importance and the drive to digitalize it are similar to those that prompted the rise in the adoption of product management systems.
A big driver is the need to optimize quality at each step of the value stream while streamlining the hand-offs between them. With QMS, everyone across the lifecycle gains easy access to all data gathered from each step. This helps teams avoid problems or minimize the costs of problems by identifying and solving them at the earliest possible time in the development process.
Without a systematic view of quality, companies also struggle with downtime, rework and slow productivity growth. They’re less agile when confronted with changes to market and consumer demands, and they struggle with risks due to the complexities that exist throughout the manufacturing value chain.
Together, these issues conspire to slow getting new products to market.
The Frost and Sullivan study reports that QMS helps organizations “improve the efficiencies of their manufacturing processes, reduce costs and rework and improve manufacturing productivity.” In turn, this can have a positive impact on an organization’s financial status.
QMS in the context of the product lifecycle
To get a clearer vision of how QMS works, it helps to compare it with product management systems to reveal the synergies gained by integrating the two.
This strategy includes:
Conceptualization and ideation – The first stage of quality begins early with gathering customer requirements and understanding their business needs to create a new product concept. QMS can help facilitate this by feeding data and information from earlier product generations into these early stages.
Product design – As the product team designs the product, builds prototypes and defines the manufacturing process, the quality team develops the control and inspection plan. Though control and inspection is often considered part of the manufacturing plan, involving quality ensures the team understands how the product and processes will be tested during manufacturing, as well as the expected level of quality.
Supplier quality – Most companies buy materials and components. While the product team specifies them, quality verifies them through testing and collaboration with suppliers to confirm they meet standards and expectations. This ensures inputs aren’t found to be unacceptable later in development, when it would require a costlier fix and delay projects.
Failure mode and effect analysis (FMEA) – Using a step-by-step approach to identify the possible manner for which a design might fail, and critical to determining supply quality, is FMEA. It can be part of product development and product lifecycle systems, but is also a crucial QMS component.
Manufacturing – Quality testing and assurance continues through manufacturing as teams execute the control plan and inspect both the product and the process, including the tools used in production. With QMS, everything is monitored and tracked, and immediate corrections are made following the identification of nonconformance. Gathering and disseminating data, drawn from these tests, is automatic and trends are recorded to facilitate statistical process control.
Maintenance – Both product management systems and QMS gather data about product behavior once it’s delivered and in use. This helps product and quality professionals understand causes of problems that crop up. The systems make this data available for use in the design of new products.
With QMS and an end-to-end, closed-loop approach to quality, manufacturers ensure that all the inputs, whether coming from a machine, human or test, are being consolidated in one, always available, easily accessible system.
Elevating quality
It’s time to view quality management as having the same strategic value as product development, sales, engineering and manufacturing management. The market demands it, and the technology is available to support it.
When using QMS, manufacturers can extend quality throughout the enterprise informing each other function, which compounds to the overall success of the organization.
This concludes our series on the future of quality in manufacturing.
About the author
Raffaello Lepratti is the vice president of business development and segment marketing within the Manufacturing Operations Management software business of Siemens PLM Software. After several years of experience in the car manufacturing industry, he held positions in product management, marketing and account management at Siemens AG. Since 2015, Raffaello has been part of the Siemens PLM Software organization and a member of the MESA board of directors. He holds a Ph.D. in Applied Science for Human-Machine Collaboration. He is married and has 3 children.