What sustainability means for the automotive industry – Part 2 transcript
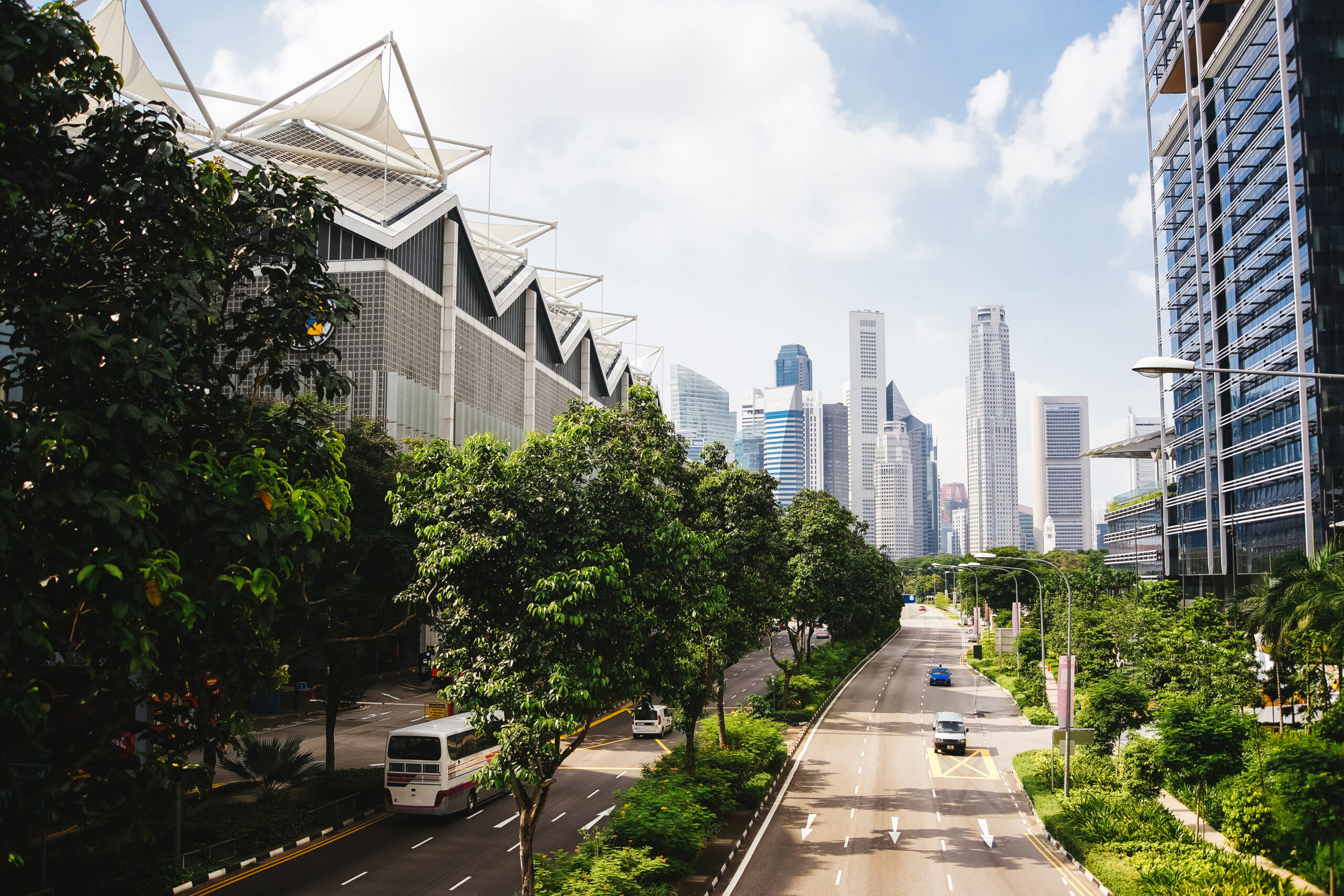
Conor Peick: We’re seeing that sustainability can have these wide-ranging impacts throughout an industry and thinking of AVs in particular, we’ve touched on a few of these aspects. I’d be curious to hear from you guys, how do you see sustainability impacting the stages of the AV lifecycle? We’ve talked a bit about design. Eryn, you said that the design engineers’ job is basically harder than it’s ever been. So, in addition to that, how does sustainability impact AV production and in particular the end-of-life recycling or dealing with these vehicles as they come to the end of their service lives?
Eryn Devola: I’m going to continue to put more pressure on that design phase and share this statistic that 80% of all environmental impacts are determined during that conceptual phase, whether that’s the impacts of the product itself or the way that it’s produced. So up front is when you must make those decisions about what’s going to happen to it at the end of life, you can’t wait for that product to be at end of life to start making plans for that product next life. It’s about designing products that can be better disassembled. For example, I had a conversation just a couple of months ago with an aluminum manufacturer that was talking about how do we recover aluminum from vehicles or build them in a different way that makes it much easier to recover that aluminum at the end of the life of the product.
These are the conversations that have to happen up front to minimize those impacts at the end. The other big one is that the best way to become more sustainable is to make end of life further away. So really building more reliable products with the bigger lifetime. Again, that all starts at the design phase. I hate to say it, but a lot of the responsibility for what happens in other places is really determined at that design phase. This is why it’s so important as we talk about autonomous vehicles because that’s where we are. We’re determining what all the requirements for these vehicles are. We’re in this proving phase and the decisions we make now can have impacts for 20, 30, 40, 50 years in the future.
Nand Kochhar: Yeah. And to kind build on that aluminum example because it brings the end of life and design together based on the recycling because aluminum is expensive as well or costly as compared to some other materials. There are certain grades of materials, and you can’t mix those up. So, from a recycling perspective, sorting those materials and then putting them in separate bins so you can recycle them. And that comes back to the question of what the overall cost is and then bringing it back for the next generation of the vehicles, how do you do material selection? So now you’re considering that I have to manage separate bins and have to recycle them differently. Versus can I pick another grade which could be common, but it’s a little bit more expensive up front in the design part, but ultimately net cost is going to be a saving.
Those are some of the examples where end of life and the design cycle kind of come together when you look at it as a holistic end to end situation.
Now, let’s look into the supply chain transparency, which I think we’ve already touched on a little bit that has become a vital component of sustainability efforts. How can companies manage where their materials are coming from and their overall carbon footprint?
Eryn Devola: I think so much of this comes from or so much of the supply chain comes from having that transparency. You mentioned it in the question and then what that transparency looks like one of the challenges that we have as a manufacturer of so much hardware is really understanding what data is available and then what level of granularity or what precision that data is. And I think the first effort is always getting something and then getting more and more precise with that over time so that you can make better and different decisions. The other challenge I think we’re going to have, and you mentioned this a little bit when we were talking about aluminum recycling, is that the demand for things like secondary plastics and secondary material is going to increase.
And so, part of the transparency is important, but once you have that transparency, making sure that more sustainable alternatives are becoming more available. I think as a global challenge that we have right now, for example, recycled plastics are in high demand, and we see companies looking for advanced purchase contracts. And so, as we shift, the whole world has to shift a bit and I think we’ll see demands for secondary material increasing and the companies are going to have to be pretty strategic and securing those materials in the short term.
Nand Kochhar: Yeah, you’re absolutely right. Again, from my experience, we dealt with this quite a bit during production scenarios when there were disruptions in the plastic raw materials availability. You have companies who have to have alternative materials, alternative options, and they need to get the performance testing done on those materials that they’ll give you equivalent performance or better becomes very critical not only just as a transparency of data but to have alternative solutions ready cause any of the supply chain disruptions.
Usually, you would don’t want to rely on a single source, and when you have a dual source, you can quickly for whatever reason, whether it’s cost, whether it’s competitive pressure or some disruption, that you were able to adapt and not compromise on your production and so on.
Conor Peick: So maybe we can look specifically at battery recycling as well. I you know we’ve touched on a lot of aspects of vehicle and life and recycling for tons of materials. But I think, like batteries that will power electric vehicles and most likely autonomous vehicles as well. I know there’s going to be an influx of these things. So, what are the specific challenges related to battery recycling and bringing those materials back into the lifecycle for reuse?
Eryn Devola: One of the things you think about is as we make a transition to electric vehicles, there is a huge demand for batteries and the challenges that those giga factories are being asked to come on online as quickly as possible. One of the things that I’m sure many of your listeners know is that battery production tends to have a relatively high fallout and that recovering material is has traditionally been complicated.
What we’re seeing with some of these new battery factories is twofold. They’re using digital twin technology for their production facility to better understand their there are critical factors for fallout and improve that first pass yield and get better quality out of their process. The second thing we’re seeing is that they’re building recycling processes right in or right next to the plant where they’re doing manufacturing so that they can take that precious resource, understand the problem, and recycle it right there. So, I think these are two ways that we’re really looking to minimize and reuse resources.
The other thing that’s happening that I think will also help here is there’s a movement in the UK called the battery passport. It’s going to be regulatorily required in 2025 that requires manufacturers to know where their batteries are, because one of the challenges in the past has been knowing where these batteries wind up to pull them back for recycling. And I think this problem with the legislation will be solved in the short term and giving people more transparency to bring those batteries back into their process.
Nand Kochhar: Very good points. I think one of the biggest things we help companies with through our digitalization technologies is through reduce the scrap rate. So today, especially within batteries, the cell manufacturing, depending on the manufacturer, there’s a heavy percentage of scrap, especially during the development initial stages and before it’s streamlined.
We help companies not only from a technology standpoint and the chemistry modeling perspective, but also managing the data or monitoring the data throughout the various steps of cell manufacturing and optimizing that so that we minimize the waste. That’s one of the biggest ways. Also, I think overall with the battery passports as they roll out, the batteries can also be repurposed that it’s not necessarily the EV batteries going to stay in the electric vehicles, only at the second life. Battery could have different purposes.
For example, for the storage and things like that are going from one system to the other, so there’s a lot of ideas around how do we minimize the new mining resources by planning different applications for the batteries and the EU.
Conor Peick: As we’re as we’re coming to the end of our discussion today, I think I’d like to zoom out again. So far, we’ve talked a lot about autonomous vehicles and the automotive industry in particular, but mobility is comprised of a lot of other industries as well, and a lot of different ways of moving around.
I’d like to hear what you guys think about, how is sustainability changing how we move people and goods kind of in the abstract, more than just cars and personal vehicles?
Eryn Devola: As part of our Siemens portfolio, we also have a rail focused mobility business. And what we’re seeing there in the US and across the world really an increase in demand for rail travel. So, I think there is a bit of a return to rail movement and the other thing that we’re seeing is in cities and congested areas, the transformation for busing for people and goods transportation to electrified vehicles to help with congestion #1 and with pollution #2 in those in those areas really improving the air quality for the folks who live there. I think in the US this is a little bit slower, but we’re definitely seeing those first early indicators of moving back to rail, and electrifying vehicles that spend their time mostly inside city footprints.
Nand Kochhar: Yeah, Conor, again, as the world population continues to grow, all these impacts, like crowded cities and thenneed for more transportation of goods and people continues to increase. So that’s a huge sustainability challenge. I think that offers gives us the opportunity to continue to innovate.
Eryn already touched on connected cities, whether it’s the railway systems of the busing. But one of the other things going on is the trend in the micro mobility are some also call last mile driven. So, within micro mobility, I know we talked about cars all the time and autonomous and electrified cars, but if you look at some parts of the world, especially within Asia Pacific region, you will see mopeds, E scooters, motorcycles, rickshaws, everything converting into electrified products which feeds towards sustainability goals.
But that’s another mode of transportation which people are adapting more and more from overall, both for people transportation as well as for the goods delivery.
Conor Peick: Before we sign off for the day. Is there anything else you guys would like to leave our listeners with today?
Nand Kochhar: I think I would say overall sustainability is everyone’s responsibility. Eliminating waste is good for the environment, good for our next generation and good for our business. So, continuing looking for opportunities where we can eliminate waste, we do that. And in this podcast, we talked about during design during manufacturing. But I think equally important is during usage or the application of the things, I think that will make a huge impact down the road for all of us.
Eryn Devola: Nand said it so well I’m not sure I have much to add. I would just only say it as Nand just mentioned that sustainability is everyone’s job. I think sustainability will become part of every job and really the more we can integrate it into the design process, the more successful will be long term. So, any of you design engineers out there looking for ways to put sustainability up front will only benefit your organizations.
Conor Peick: Well, thank you guys so much. I’d like to say a quick thanks to Eryn for joining us today. It was a great pleasure having you on the show and a big thanks to my co-host Nand as well always. We always appreciate your expertise on these podcasts. A big thank you to our listeners as well for tuning in and we hope to see you again soon back on The Future Car.
Siemens Digital Industries Software helps organizations of all sizes digitally transform using software, hardware and services from the Siemens Xcelerator business platform. Siemens’ software and the comprehensive digital twin enable companies to optimize their design, engineering and manufacturing processes to turn today’s ideas into the sustainable products of the future. From chips to entire systems, from product to process, across all industries. Siemens Digital Industries Software – Accelerating transformation.