The future of smart machines and smart industries – Transcript ep. 2
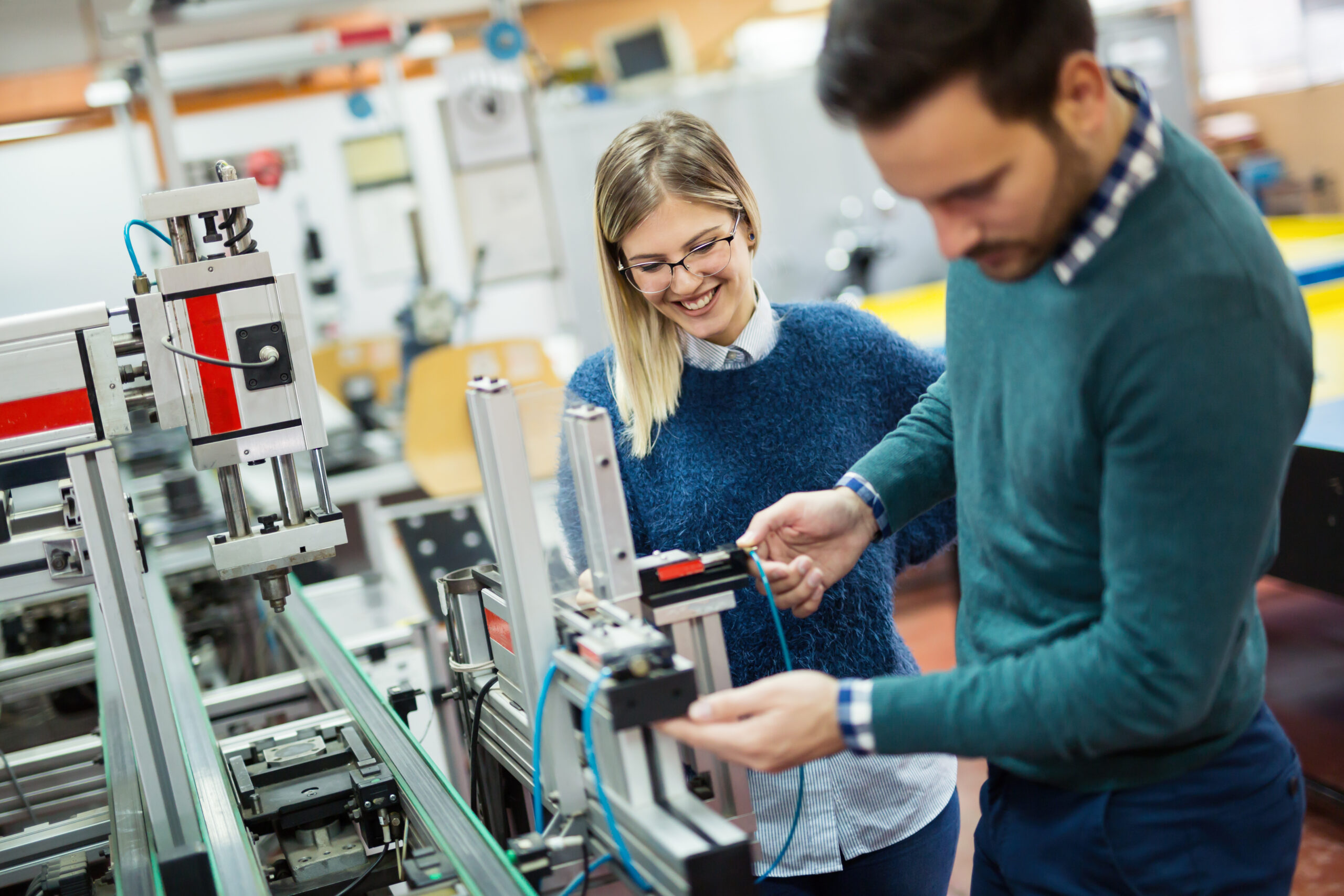
Our engineering experts, Dale Tutt, VP of Industry Strategy; Rahul Garg, VP of Industrial Machinery; and Michael Thomas, SVP of Factory Automation and Head of Production Machines, continue their discussion of the trends and challenges in the manufacturing ecosystem today, including technological advances on the horizon, and the role of digitalization in enabling the future of smart manufacturing.
Read the transcript below or listen to the audio podcast.
Conor: We are starting to talk about some of the technologies available to companies to help them overcome the challenges that we’ve talked about in our previous podcast episode. We have discussed the digital twin, with the idea of digitalization and digital transformation.
Rahul and Michael, are there any other key technologies that can be used to help overcome some of the challenges like shortages of labor, complexity, increasing sustainability requirements and so forth?
Rahul: Yes, from a technology perspective, even on our sustainability quest, there are many capabilities now available that can help you evaluate energy models, or per machine, and evaluate not just at the component level, but across the entire function of the entire machine itself.
So, we are not just focusing on the energy consumption of a drive or a motor, but the implications of that drive or motor working in tandem with the rest of the of the entire machine itself, which may have another 20 or 30 or 200 such drives.
So what’s the implication of you making a change in any one of these areas? There are various ways by which you can bring in machine level simulation. You can take it a step further up and do a plant level simulation to help evaluate how a machine functions in the context of a full plant simulation and then try and do an energy evaluation across the entire plant.
And then, on an ongoing basis, evaluate the electrical behavior model, making changes there, and knowing what the impact of that change will be in other parts of the application. There are plug-in tools and software applications available inside the Siemens organization that help these companies evaluate multi-physics models and papers to push this further. It will have an impact on its load bearing capacity or vice versa. So, it helps evaluate many things from a simulation perspective.
Basically, this is simulation for industrial systems. And the industrial simulation for the industrial system encompasses not only a component, but it’s also at a machine and plant level. It allows you to evaluate the entire performance of your production plant, all the way from production planning to the actual operation, so there are many tools now available to help customers speed up and assist with their transformation journey.
From a technology perspective, the industry has evolved significantly over the last few years, along with the trends and issues that Michael was talking about earlier. So, it’s more imperative for machine builders to seriously look at these to help them succeed and manage the expectations of their end customers.
Michael: Yes, and we started like 10 years ago in using first simulations in the design or planning process of machinery and it is more and more moving from the design to a simulation and digital twin over the life cycle, meaning the digital experience is generated in the design process and maintained over the life cycle. They are used in the operation of the machine, and they also do some research on training of AI algorithms. A digital twin cannot simulate failures on very expensive machinery equipment, and therefore it becomes more important to address the specific topics we can simulate and the value of how this will help in the machine build to solve that topic.
On the other hand, simulation during the design phase makes it sustainable over the life cycle of the machinery. And that leads us in combination with machine builders, in automation and the simulation, to optimize them. The PLM landscape of the machine builder automates what is possible because we always challenge the machine. So, with a digital twin, how do you derive it between the manual work and automated by applying the technology in a very smart way?
There are many examples. The value of that digital twin and simulation is only sustainable if we manage to get it highly automated into the design process, and not as a manual.
Is it the PLM landscape in designing manufacturing of the machines up to the shop floor, getting data connected to it?
Dale: I like this discussion around the simulation, the digital twin, and how we can leverage AI in the future and certainly you know, Michael, you’ve talked a lot about the benefits that the customers are getting when they start adopting this technology.
So, let’s dive a little deeper into the technology itself. This conversation is bringing us back to conversations that we had in aerospace about using simulation to fly it before you build it, proving everything beforehand. So, what really makes this work? Let’s talk about the technology that makes this work so that we can get it to our customers to see those benefits.
So, Michael, what are your thoughts?
Michael: From my point of view, with the machine builders we need to start with the design process. What are the challenges machine builders have? And that’s industry-domain specific. In general, designing the machines, and going into a new domain we talk with the machine, and then we can enable or teach the machine builder to use the Siemens simulation portfolio.
Combining this with our expertise on drives and motors, as Raul said regarding Mechatronic. We are educating and enabling them to utilize their “fly the machine before it’s built” methodology. That’s one topic. The other topic is that many things we are doing with machine builders, and being in a very close contact with machine, there is also learning on our side in terms of where our portfolio has barriers and hurdles in terms of integration, workflows at the machine builders, and we are internally feeding this with the portfolio responsible organizations to make it possible for machine builders to apply our portfolio on automation and simulation.
Machine builders are the experts in their domain and the final evaluation of how the digital twin model fits to reality. So, that’s something machine builders need to explore by themselves, and we enable them to do this in the most efficient manner. In the past, we had standard applications on machine functionality across the cutter and we are enhancing these applications with the automation part of that application, combined with a digital twin and the basic model for simulation.
This is just one target to make for the machine, but it’s easy to use our portfolio to reduce the time to market for the machine builder and not have to invent the wheel again but rely on proven functionality we can provide and then modify and add the machine builder or technology-specific add-ons for differentiation in the market.
Rahul: Yes, you hit upon some very good points there, Michael. I think the last key point about having libraries which have already been well evaluated and tested. These libraries then can be used to create your complete mechatronic digital twin.
It allows you to evaluate your digital twin for energy flows, trying to look at simulating and converting live with the rollers, the winders, the clampers, and all of these different sub applications. Then putting them all together and in an easy set up Lego block manner, with obviously some level of intelligence through an A1B digital twin format using Amesim and then taking it all the way up to 3D complete physics with the kinematic motion model using an XMCD as a 3D evaluation tool.
That really helps simplify the process for machine builders in great ways, and to put it in the context of a managed environment. We can manage the machine life cycle as you deliver variances of that machine to various customers. So, when your automation projects manage your electrical design elements, you manage the changes as you make them.
So, two years from now, if you need to do something different, you know what has been done during the initial design phase. Then you can make the appropriate changes quickly and reflect it, and your ongoing updates for the end customer as well.
It’s bringing in the simulation capabilities, the automation capabilities, and the PLM backbone with teams that are bringing those three capabilities together to help differentiate and/or help machine builders take their business, design, and engineering operations to the next level.
Dale: I like how you characterize that full life cycle and how you leverage that information throughout the entire life cycle of the design and into your manufacturing and maintenance facility and how you upgrade and optimize it in the future.
So let’s talk about one of the concepts with the digital twin and factory operations together with convergence of information technology and operational technology. Michael, are we approaching an integrated digital thread from the machine and factory design into actual operations? And what benefit can this provide for our customers as they go forward?
Michael: Yes, for machine builders we are working on the concept of Industrial Operation X that all the machines are looking into with the big classical motion Control Automation PLC in the concept of totally integrated automation for things you cannot automate today, for which you need to connect to new technologies. There are two key elements:
- Using IT connectivity in all aspects, but also applying AI technologies, plus domain-specific technologies. This is driving us in terms of how we want to develop our portfolio. We can enable new dimensions of automation that make it possible across systems to bring the functionality together for a specific machine and domain, and we are at a starting point there where we talk about the future of machine building with our customers. It is uncertain what is going to happen in the next three to five years, but with our capabilities and with our mission, we are capable to take our machine builders and technology from today to connect new technologies and take them on the journey into an innovative future.
- We have the capabilities that we can demonstrate in a simulation that are first examples of very powerful edge applications. AI and SMS are new technologies that will change automation concepts of machines and the capabilities of machine builders and manufacturers into the future, to deal with the global challenges we have on this planet.
Rahul: Well said, Michael. This is quite exciting to me in terms of what’s out there in the future. I would characterize some of the things Michael was highlighting by breaking it up into two steps as well.
The first, is having more performance insights. So, you have a transparent way to understand what’s happening and to effectively increase productivity. It helps you get performance insights at a machine level, a line level, and a plant level, and use that to understand what’s going on to make precise decisions to optimize the machine availability and performance.
This is something that companies are already beginning to understand and appreciate this value. And we are beginning to adopt it and get this concept of taking it to the next level by bringing in more AI into the process and the whole concept of an executable digital twin which moves into zero downtime, as that’s the obvious goal, though not practical it is the reason zero downtime is giving us even more.
It is providing a better understanding of intelligent automation and being able to quickly evaluate what’s occurring, and using that information to optimize the performance in real time. We have customers beginning to look at this for some smaller applications where they’re trying to detect missed functions that could be happening inside the performance of the machine and using real time information to make changes on a real time basis.
So the performance can be optimized without any human intervention. These are exciting capabilities that are available now and being evaluated for adoption with the performance-based engineering and performance evaluation and the executable digital twin, which brings in more automation and artificial intelligence capabilities. [End of podcast02]
Siemens Digital Industries Software helps organizations of all sizes digitally transform using software, hardware and services from the Siemens Xcelerator business platform. Siemens’ software and the comprehensive digital twin enable companies to optimize their design, engineering and manufacturing processes to turn today’s ideas into the sustainable products of the future. From chips to entire systems, from product to process, across all industries. Siemens Digital Industries Software – Accelerating transformation.