Expand design space exploration with intelligent automation
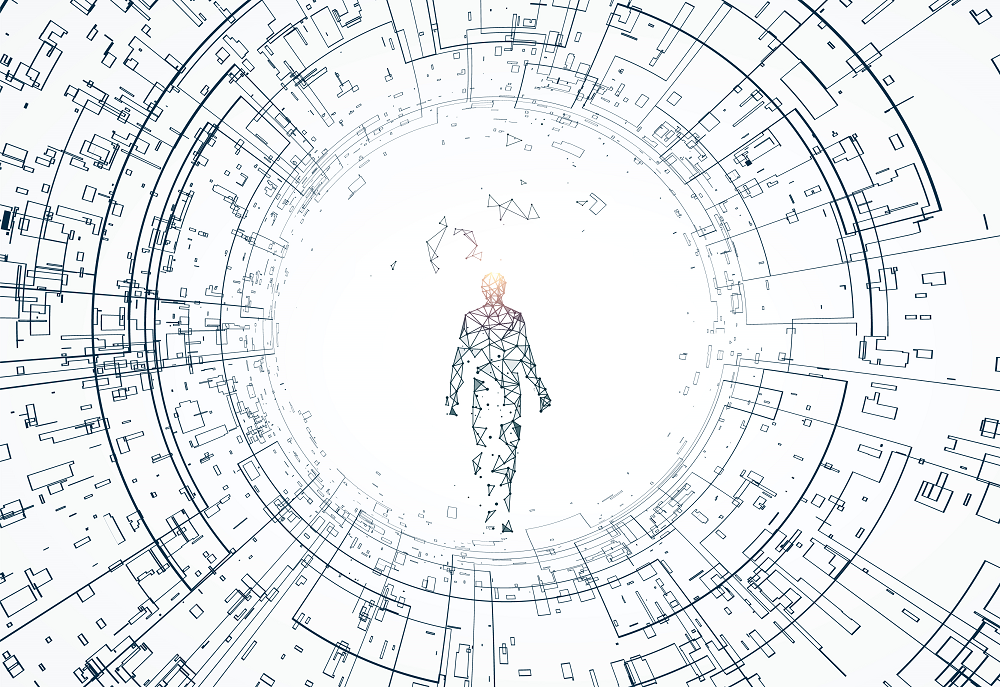
What if your product development team had a genie in a bottle that could pop out and optimise virtual prototypes every time your team tried something new?
No highly trained optimisation specialists. No time-consuming automation scripts to write. No complex analysis of multiple parameters.
SNAP! Here’s your optimised prototype data.
The product-development process would be faster, easier and more effective, and costs would likely drop, too. The potentially bigger gain, though, would be wider adoption of design space exploration (DSE) by essentially flipping the simulation process so it is less about meeting minimum requirements and more about building knowledge, impressing customers and breaking new ground.
With more time and resources to push innovation boundaries, design teams could use simulation to identify new ways to solve existing challenges and envision new products that previously would have gone undiscovered.
Easier, faster and more affordable design optimisation
What many people don’t know is that the “genie in a bottle” exists and is better known as intelligent automation: that is, software-driven processing that can quickly integrate and assess disparate data sets, and then make decisions and perform tasks that humans alone need hours or days to accomplish.
It’s a new type of software capability becoming more commonplace across businesses. In the finance function, for example, intelligent automation is shrinking how long the monthly “closing of the books” takes from days to minutes. It’s also the power behind generative design.
For digital product or system simulations, intelligent automation can:
• Integrate data from any and all simulation programs in use
• Perform computational analysis to optimise the model in minutes
• Feed the optimised model data back into the simulation programs in use
Intelligent automation is added to the simulation process through modern DSE software, which comes as an out-of-the-box solution with drag-and-drop workflows that run in parallel with existing workflows. This is a significant change because it makes design space exploration feasible and cost-effective for any project.
Moving from design optimisation specialists to intelligent software
Traditionally, DSE has been limited to product designs where miniscule differences can have a substantial impact on performance—and return on investment for both the company and its customer. Think Formula 1 race cars, where eking out the last few percentage points of power means the difference between winning and losing; or aerospace engines, where more efficient jets save on fuel costs and reduce environmental impact.
Without intelligent automation, DSE consumes more time and resources than it’s worth for most designs. Engineers, analysts and optimisation specialists, each working with different types of software and data sets, work together on studies in which products are designed, tested and reviewed in an iterative process. Automating the process generally requires the costly and time-consuming writing of customised software code.
With intelligent DSE, engineers with little specialised training or experience in design space exploration can discover optimal designs in less time than specialised teams following the traditional process. Intelligent DSE can be used more frequently, if not always, and even in mature industries.
Carving out a profitable niche with DSE
For example, take Becker Marine Systems. The company has carved out a niche in the commercial shipping industry by making customised energy-saving devices used on older ships that are less energy-efficient than newer ones.
Becker Mewis Duct, a simple piece of equipment, reduces fuel consumption by about 5 percent by enabling a vessel to travel faster at a given power level. The cost savings could be as much as $500,000—a result of using 2,000 tons less fuel.
For each duct, the design team draws on 40 design parameters to create a unique duct specified for each vessel’s hull. Without this fine-tuning, the duct would not deliver the energy savings each client specifies. Additionally, the team works on a strict timeline because physical tests in a towing tank are scheduled in advance and can’t be missed.
Success depends on rapid virtual prototyping using a DSE solution with intelligent automation. The fast, minimal-resource solution is what makes each Becker Mewis Duct unique—and thus highly effective and valued—despite the maturity of the marine market and the time constraints on the process.
“From the moment we receive the order, we typically have six weeks to find the required energy savings,” says Steve Leonard, head of R&D for Becker’s product engineering and development subsidiary. “If we can’t improve the energy efficiency of a given vessel within the allotted time, then basically we have failed. There are no second chances.”
Intelligent automation makes design space exploration the new standard
Though it can seem magical, DSE software with intelligent automation capability is real and currently available. Becoming more widespread in use, it soon will become the new standard: it requires a relatively low investment compared with the outsized benefits, and it can be deployed within existing design workflows with no disruption.
No longer will design space exploration be just for the highly advanced industries like aerospace and Formula 1. With regular application of DSE, design teams can consistently deliver the best possible design and create new, high-value solutions for a wider array of product and projects. If you’re already doing design simulation, why stop at the first design that passes an arbitrary benchmark, when for no more time you could get to the “best” design?
This concludes part one of our series on design innovation. In part two, we discuss how to go beyond the typical design space exploration strategy.
About the author
Bruce Jackson is an account orchestrator for Siemens PLM Software and works closely with aerospace and defence companies in the U.K. He has been working in the PLM and CAE space for more than 25 years and is currently working with companies across Europe to help them achieve productivity gains through digitalisation.