Future-ready framework for enterprise system architecture
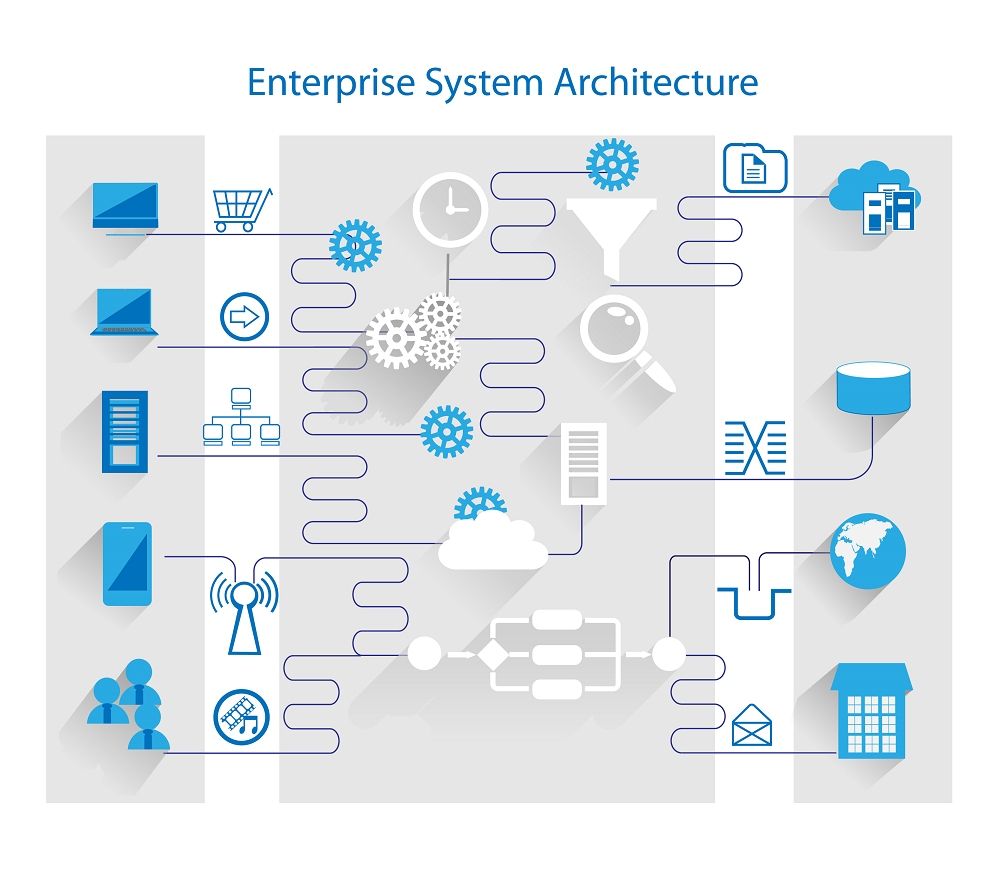
By: Alex Allison and Josh Ray
Effectively managing and updating your enterprise system architecture, the overall IT system architecture of an organization, is key to competitive business operations. Today, that means shifting the architecture away from silo-centric tasks and toward facilitation of cross-functional collaboration. Because of this, successful modernization isn’t just about technology: It requires a change of culture.
A modern enterprise system architecture can seamlessly connect core enterprise applications such as manufacturing execution system (MES), enterprise resource planning (ERP) and customer-relationship management (CRM) with one another and with other information systems to support an open, automated and collaborative environment. The outcome is a scalable ecosystem of applications and end users sharing data with one another and with machinery/devices on the Internet of Things. This architecture orchestrates the information flow and helps generate up-to-date insights from the process data. These insights could include predictive planning; real-time visibility and traceability for assets, goods and services; and visibility into machine and process tasks along the product lifecycle.
Modernizing your enterprise system architecture is a multi-stakeholder project, one that requires manufacturing leaders to ask big-picture questions that help assess whether an organization is indeed ready for change, the pace of change that’s acceptable and the knowledge needed for effective planning and execution.
Driving transformation starts with a planning framework, and putting the transformation in motion begins by asking planning questions like these:
Do I have the support I need? Stakeholder buy-in is key to enterprise system architecture success. Develop a vision of the business value that will be delivered. Assess your company leadership’s understanding of the technology gap. Consider creating a gap analysis to demonstrate needs.
What are my limitations? Identify contingencies based on your company size, available budget, current strategic plans and other factors specific to your organization.
Who needs to be involved? Map your current state and future state together with representation from functions in the enterprise that contribute to or use product data, and which understand the value of modernizing your enterprise system architecture. This will help ensure you meet stakeholders’ needs while avoiding making decisions in a vacuum or moving problems downstream.
What changes will best prepare us to adapt to fast-changing conditions? Consider future states, including the potential for organizational cloud adoption or regulatory and compliance changes, that may arise with smart manufacturing production and product models where standards currently lack. Smart manufacturing integrates intelligence into actual machines, parts, materials, products, buildings and supply chains, and then applies that intelligence within a connected, open, end-to-end process and infrastructure.
Turn to knowledgeable partners to help. For example, many cloud vendors have product roadmaps that can meet a company where they are today and be adjusted without major disruption when the cloud journey takes a different turn. This helps provide for resiliency in enterprise architecture design and modernization.
What resources should I tap to help? Don’t let fear of the unknown blind your organization when it comes to modernizing your enterprise architecture. Instead, join online communities that share best practices and knowledge between providers and practitioners.
Consider industrial-scale additive manufacturing (ISAM) as an example. ISAM holds tremendous potential for highly innovative industrial design, sourcing and production. It’s one of the most promising opportunities associated with smart manufacturing because it’s an entirely digital production model from end to end.
Though the technology and resources exist for ISAM, adoption has been slow as product designers, procurement specialists, production engineers and other front-line roles struggle to tap into quickly evolving technologies and techniques in the AM market. To combat the knowledge gap, we created the Siemens Additive Manufacturing Network, a cloud-based open-platform service that links a trusted network of major players together to work jointly to advance AM industrialization.
What does success look like? Seek out examples of widespread industry adoption or case studies that support enterprise system architecture modernization with demonstrated measurable results.
For example, in the electronics industry, software to manage the product lifecycle is the system of choice because of its ability to combat inefficient end-to-end processes, fragmented data systems, mounting product complexity and stringent regulations.
One specific case example to look to as a reason for adopting this software is FLEX, an electronics-manufacturing service provider headquartered in Singapore that has been operating a plant in Guadalajara, Mexico, since 1997. The Guadalajara plant struggled to improve production efficiency, optimize systems engineering, address global competition and provide high-quality end products in shorter lead times for the injection-molding business. After implementing software that enabled the company to offer integrated solutions to its clients—ranging from design, repair and maintenance to actual production—production lead times were reduced from four months to five weeks; effective implementation of new techniques such as in-mold labeling were introduced; more complex work could be taken on; new business opportunities developed; and, the plant gained recognition for superior quality standards.
Once your organization has answered these questions, it will be on the road to making a sea change in its enterprise architecture. That means better outcomes lie ahead, such as reduced costs and more informed decision-making, as well as increased agility through faster project planning and execution.
This concludes part two of our series on enterprise system architecture. In part three, we discuss kickstarting effective change management.
About the authors
Alex Allison is an account orchestrator with Siemens PLM Software and has been with the company since 2013. In his current role, he is responsible for maintaining relationships with electronics and high-tech companies on the Eastern seaboard. Alex began his career in the semiconductor industry, specializing in manufacturing systems. He has experience around OCM, managing complex enterprise system architecture, and ensuring customers have the right solutions and processes that will result in transformational efficiencies throughout their business.
Josh Ray is an account development executive for Siemens PLM Software. He began his career in the manufacturing software organization. Josh is passionate about people and technology, and his current role is to support business development in the industrial machinery and medical device industries. Josh works with companies to increase awareness and adoption of technologies across their innovation and product lifecycle. He regularly engages with C-level executives in this role, which inspires his drive to gain a deeper understanding of industry trends and the obstacles companies currently face.