How smart engineering can solve heavy equipment challenges
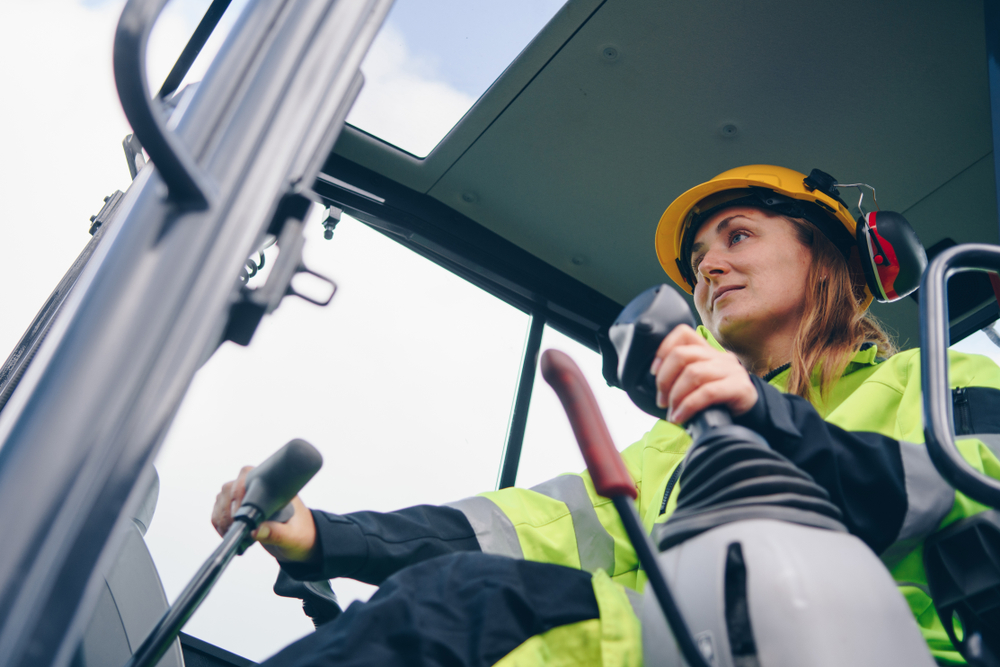
Smart engineering is data-driven engineering that optimizes historic and real-time data in all stages of a product’s life. It can be applied throughout the spectrum of heavy equipment markets and is driving change in all stages of product lifecycle management.
Within the heavy equipment vertical, smart engineering enables the capture of data throughout a machine’s active life. The data informs operations, maintenance and an ongoing design-refinement loop. Most meaningful for equipment users, smart engineering makes it possible to include high-value features, such as predictive maintenance, remote diagnostics and product customization.
In fact, heavy equipment users benefit in multiple ways:
• More productive, reliable equipment. Real-time awareness of what’s going on with equipment and cues for maintenance or repair keep projects on time and ensure task accuracy. It also means that OEM and services can manage spare parts inventory and ensure that needed parts are on hand at the right time.
• More autonomous equipment. Smart machines can: precisely manage construction or grade a foundation or other surface; traverse a predetermined safe path repeatedly from mine to crusher and plow entire fields with minimal direction; reset hydraulic pressure and flow for each attachment based on prior coding, digital inputs and sensors that detect the environment and equipment applications.
• Less skill and physical effort required. With fewer farmers, miners and construction workers than in the past, machines that perform tasks, which well-trained users previously managed, allow new operators to get to work without an apprenticeship or mentoring, and they relieve fatigue among veteran operators. Additionally, the data-driven design has produced intuitive controls that may resemble consumer handheld devices. That familiarity smooths the learning curve for new entrants to the industry and makes equipment control easier for older operators.
• Safer working conditions. Integration of sensors, such as forward-looking infrared imaging and radar, dramatically improves safety in the dark or other conditions with limited visibility. Because environmental factors commonly affect heavy equipment operations, control system-level field and weather condition inputs via sensor models alleviate safety concerns as well as productivity concerns.
Smarter machines are less expensive to operate and maintain
The necessary components for smart machine capability are: digital simulation for creating a digital twin; sensors for testing and monitoring; Internet of Things (IoT) networking; and PLM software to orchestrate connectivity and action.
By making machines smarter, manufacturers gain leverage in reducing the total cost of ownership and performance for machine users. Leveling a road today requires surveyors with laser transits to evaluate the grade compared to the plan. Smarter machines can integrate the 3D grade plan into the dig profile and optimize fuel usage by moving the most dirt in one pass based on the calculation.
Smart machines have a sensor inside the excavator or bucket that automatically meets the grading component. As earth goes up or down, the sensor recognizes its level and brings the grader down to automatically provide the final finish. Sometimes gyroscopic sensors act to ensure the excavator moves in the right direction and has a smooth finish. The smarter machine saves labor, time and materials to reduce the cost of ownership.
Smart engineering is transforming farming
Farming, one of the world’s oldest industries, remains competitive and dynamic. Soil additives, genetically modified seeds, better planting strategies and highly productive agricultural equipment have practically tripled yields over the past 60 years.
Farmers want to keep the momentum going, so Netherlands-based AGCO adopted Siemens PLM technology to automate boom height adjustment, minimize vehicle-induced boom vibrations, and extend ride time and fertilizer distribution on its Challenger RoGator 600 crop sprayers.
The sprayers travel 30 kilometers (19 miles) per hour and feature boom arms of up to 36 meters (118 feet) to accommodate vast acreages. The boom arms cannot bounce or bend, lest nutrients or insecticide indiscriminately distribute. Also, the boom arms must hover just so above the crop.
Using sensor data and applications in the Siemens PLM suite, AGCO designed automated and cab-controlled adjustments to accommodate for varying field terrain and crop heights. This data emphasizes operator comfort, and it addresses the issue of new operators who lacked the experience with manual boom adjustments, as well as fatigued farmers who spent long days on the sprayer to ensure the job is complete.
Making heavy machinery work easier
Heavy machinery equipment manufacturers that offer autonomous or semiautonomous functions, customized capabilities or remote monitoring and proactive service will be ahead of competitors. Users will seek out these features as they look to complete projects faster, with higher accuracy and with fewer resources.
Fortunately, smart engineering offers a path for increasing manufacturing efficiency and creating marketable differentiation in the heavy machinery equipment market.
This concludes part one of our series on smart engineering in the heavy equipment industry. In part two, we discuss how smart engineering enables better heavy equipment design and getting to the market faster.
About the author
Rahul Garg is the vice president for industrial machinery and heavy equipment industry at Siemens PLM Software, responsible for global business development. He and his team are responsible for identifying and delivering strategic initiatives and developing solutions for the industry, working closely with industry-leading customers and providing thought leadership on new, emerging issues facing the machinery industry. Rahul’s experience and insights are derived from a 25 year career of delivering software-based solutions for product engineering and manufacturing innovation for the global manufacturing industry. He has held leadership positions in multiple areas, including research and development, program management, sales and P&L management, having focused exclusively on the industrial machinery and heavy equipment industry since 2007.