Are machine shops at risk of becoming the next Blackberry?
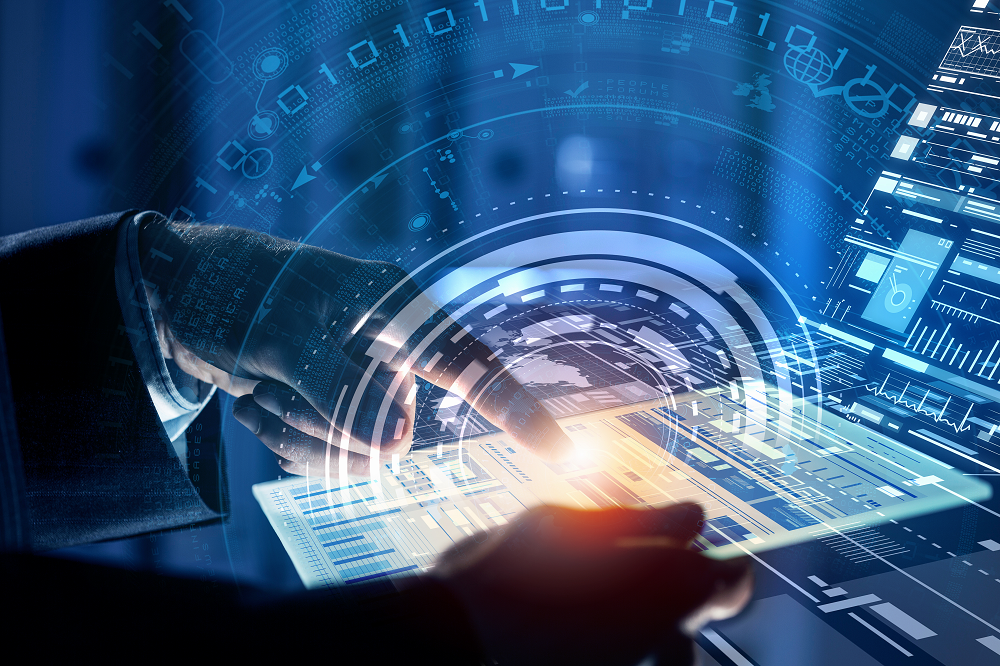
Blackberry. Blockbuster. Kodak. Business history is rife with companies that once led their respective industries, but that have fallen behind or ceased to exist.
The common thread in their demise? A failure to adapt to a fundamental shift in market expectations and customer demand that was driven by competitors that leveraged the latest technology.
• Mobile-phone pioneer Blackberry confidently optimized the QWERTY keyboard and scroll bar, while Apple captured market share with an innovative touchscreen and mobile operating system. (Ironically, now the Apple iPhone is being challenged by smartphone innovations from Samsung—which demonstrates that even the disruptors can be disrupted if they are slow to adapt.)
• Brick-and-mortar retailer Blockbuster ignored Netflix’s digital streaming threat.
• Digital photography inventor Kodak feared cannibalizing its existing film business, leaving its invention for Sony, Nikon, Canon and smartphone manufacturers to exploit.
These companies stumbled in the early years of digitalization, a trend that has since swept through nearly all industries, transforming products and how they’re purchased and delivered. Now leading-edge organizations are deepening digitalization strategies to include how products and services are developed, produced and evolved.
Big and small manufacturers need to change
This latest wave of technological change, Industry 4.0, is redefining service capabilities, competitive requirements and customer expectations throughout the manufacturing supply chain—big and small.
Industry 4.0 technology enables digitalization, where digital technologies are integrated into all business processes, creating an end-to-end system that seamlessly connects the virtual and physical. Digital twins, virtual representations of products, processes and performance, are electronically linked through a digital thread, an always-on, always-accessible feed of real-time data. Available to anyone at any time, the digital thread allows product engineers and operators to work concurrently, because they have immediate access to the information they need.
Industry 4.0 technology is transforming modern-day machine shops no less than new technologies transformed the movie distribution, mobile phone and photography industries. However, recent research suggests that many machine shops are not prepared. Of surveyed machine shops,
• Over 50 percent still rely on standalone CAD and CAM systems
• Fewer than 30 percent manage and control their data
• Approximately 75 percent rely on disconnected CMM inspection processes
• 61 percent still use paper documentation on the shop floor
• Only 37 percent use 3D printing in production
The virtual supply chain is about business, not technology
Too many machine shop owners believe that strategies that helped them succeed in the past will drive their success in the future. Manufacturing expertise has been the competitive advantage of machine shops, but it’s no longer enough. As vital links in an increasingly global supply chain, machine shops must pivot from their traditional internal focus on manipulating materials toward a customer-centric focus on quickly turning around flawless products where and when the customer demands.
A digitalization strategy isn’t only about gee-whiz technology, though often it’s presented as such. Digitalization is about business strategy to run a successful manufacturing operation.
Machine shops that adopt Industry 4.0 technology are better prepared to:
• Win bids over competitors worldwide by delivering higher-quality products faster
• Boost margins by investing in new processes, rather than tinkering with old ones
• Diversify into new markets as they redeploy their manufacturing experts toward innovation and growth
• Cement existing customer relationships with ever-improving demand responsiveness and service
• Enable the adoption of the latest manufacturing technologies, like additive manufacturing, advanced robotics and automation, and emerging technologies such as artificial intelligence and virtual reality
It’s important to note that Blockbuster, Blackberry and Kodak didn’t fail because they weren’t aware of how the new technologies were transforming their industries, or even because they didn’t change. They failed because their response was inappropriate to the challenge.
A Harvard Business Review article, “Why Good Companies Go Bad,” explains:
“The managers of besieged companies usually recognize the threat early, carefully analyze its implications for their business, and unleash a flurry of initiatives in response. For all the activity, though, the companies still falter.
“The problem is not an inability to take action but an inability to take appropriate action.”
Incremental technology improvements are only solving last decade’s problems. Such solutions are not addressing fragmented processes and the data disconnects between costing, design, engineering, production and quality.
Incremental changes to machine shops no longer work. To survive longer than the next decade, they need to become a truly digital machine shop.
Explore step-by-step options
Machine shop owners might think Industry 4.0 technology is out of reach; it’s too costly, too time-consuming and too disruptive. In fact, gradual, step-by-step adoption is possible in the journey to an Industry 4.0 transformation. Siemens PLM solutions can be implemented in stages—a planned and steady roll out that respects the need for immediate ROI and integration into business workflow, yet speeds organizations along the path toward digitalization.
Bottom Line: New market demands require new technological solutions
Machine shop owners face new challenges from the changing market expectations. Their customers will no longer accept mistakes or delays as they did in the past, and demand a responsiveness that can’t be met with inefficient production processes.
Machine shop owners should respond by adopting an end-to-end unified solution—or risk being outmaneuvered by competitors.
This completes part one of our digital machine shop series. In part two, we discuss the benefits of becoming a digital machine shop.
About the author
Sashko Kurciski is a senior marketing manager at Siemens PLM Software. Sashko leads the marketing of the part manufacturing software solutions to help companies transform their production processes through digitalization. He has been in the CAD/CAM/PLM software industry for almost 20 years, working in a range of roles, including product management and software development. Sashko holds a master’s degree in Mechanical Engineering from the University of Arizona and lives in southern California, USA.