Product lifecycle data for a truly A&D digital program management
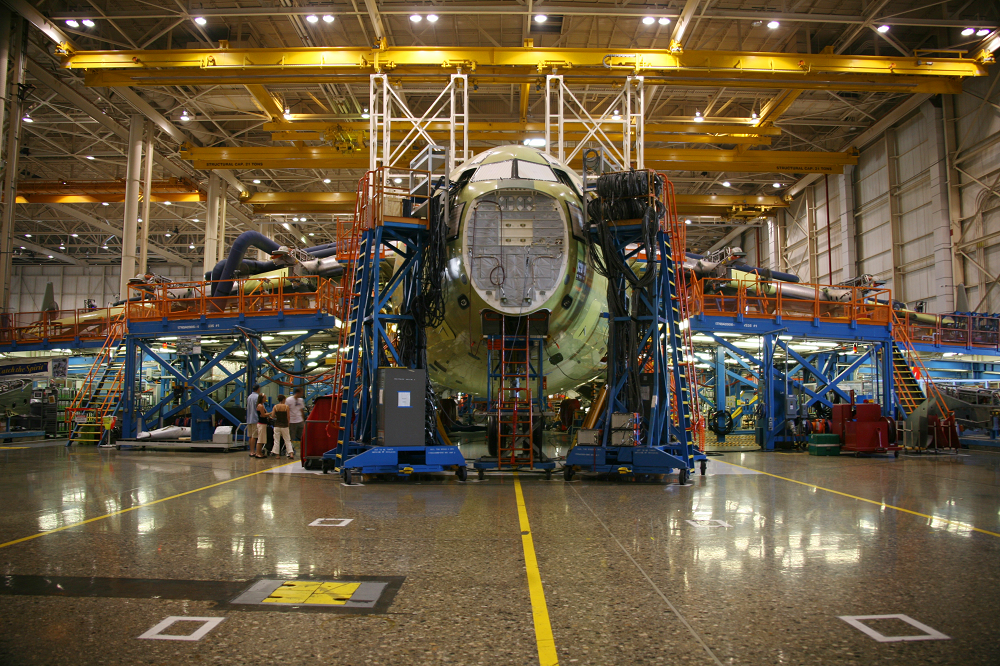
If you’re a program manager at an aerospace and defense company, you’re probably a spreadsheet expert. It’s common for aerospace and defense (A&D) program managers to use huge spreadsheets—some with as many as 40 columns and 10,000 rows—to manage independent product schedules and product programs. Unfortunately, this practice slows down workflow and weighs on quality.
Manual data entry and management ensures errors, risking accuracy and lost time. Just verifying, for example, that activities are scheduled to meet what could be 40,000 FAA compliance requirements can monopolize hours of a program manager’s time.
By contrast, when all product program data are in one widely accessible management platform, A&D programs become easier to manage and can yield higher profit margins and support longer-term revenue streams.
The reason why program managers use spreadsheets is that traditional program management software is a mix of point solutions that maintain separate sets of data, a model that some think “still works.” But it doesn’t work if you ask the most burning questions challenging A&D companies that want to stay competitive:
Can your program management processes and technology tools meet changing market demands now and tomorrow? Can they deliver on technical, cost and schedule requirements so that you can protect and grow profitability?
A&D buyers expect cost savings, fast response and anticipation of their needs based on disruptive trends such as Industry 4.0, Big Data-powered predictive guidance and the ability to access vast amounts of intellectual property data. But for many A&D companies to respond, they will need to expand their definition of “digital program management.”
If A&D companies want to respond to the forces changing their industry, they must expand what their definition of “digital program management” encompasses.What truly digital program management means
Program managers have witnessed the advantages of digital automation in production, and they know that manufacturing in general is heading toward digitally-automated and data-driven process planning and management.
Too often, however, they and their companies assume their product programs are truly digital because they have adopted a digital twin design model in engineering and manufacturing; they may even have some limited integrated data among systems. But truthfully, that’s just the beginning of digital program management.
Leaders in this area streamline program management processes by using a digital thread—an always-on, always up-to-date knowledge base tied to each program that’s available to all decision makers all the time. In this thread are all product records, from testing to potentially in-field services and redesigns. Increasingly, these A&D leaders are using product lifecycle management (PLM) as their digital program management platform because modern PLM solutions inherently create an end-to-end, integrated real-time digital thread that lives throughout a product’s life. The digital twin is just one component in that thread.
This comprehensive data—within a comprehensive program management platform—enables complete traceability of requirements from design to manufacture, and provides the knowledge base needed to manage an A&D product through its 30- to 40-year life. Throughout, program managers can easily tap the information to test the effect of any change or learn why previous engineering changes were made.
True, many manufacturers maintain much of this information now, but it’s not integrated, up-to-date and widely available to product-focused specialists. The applications and technology to power such a system have become available only in the past four to five years.
Reducing the time and expense of change
For most manufacturers, the primary goal of program management is to control costs and stay on schedule, while meeting all technical requirements. That’s especially true of A&D manufacturers.
Analysis by consulting firm Deloitte notes that one-time charges in the industry spiked in 2015, hitting $10.3 billion, up from $5.0 billion in 2014. While analysts expect the growth of one-time charges to continue to ease, they say program delays, cost overruns and funding issues will continue to plague the industry in the near-term.
High design change rates tend to occur when the product first enters production, and again when it enters service. Adopting technologies and implementing processes that enable more complete virtual testing at all stages of production can dramatically reduce these change rates.
Similarly, because A&D manufacturers build products that remain in service for decades, they continuously look for ways to make them better, faster and cheaper throughout that span. So, for example, when a program manager wants to eliminate some inspections to speed production and reduce costs, engineers must be able to answer the question: What breaks if these inspections are taken out?
With a traditional system, the only way an engineer can confidently respond to such a change request is to hunt for offline data. That’s hugely expensive and often not possible. With the digital thread, all data related to the product, including certification data and design tolerances, is easily available to make the best-informed decisions.
Further, A&D products may last 30 to 40 years, but they don’t stay the same. As products are maintained and upgraded, the digital thread enables feedback loops to capture information needed to develop new products and product enhancements, and rapidly remedy field issues.
For true digital program management, the digital thread addresses the challenges of delivering products that meet all technical and performance requirements at-cost and on-schedule. This digital thread will allow program managers to spend more time creating value-added capabilities—and a new competitive advantage.
This completes part one of our series on the value of the digital thread. In part two, we discuss how to power the A&D industry’s business agility through digital integration.
About the author
Dave Riemer is the Vice President of Aerospace and Defense Strategy for Siemens PLM Software. He is responsible for using Siemens PLM’s resources to provide value-added solutions for the Aerospace and Defense Industry. He has more than 35 years of experience in the industry. Riemer was previously the Vice President of Science and Engineering at ATK Aerospace Systems, where he was responsible for all technology in the company’s systems group, including development of the Ares I first stage booster and all engineering activities on the Space Shuttle Reusable Solid Rocket Motor, missile defense systems, strategic missile and commercial satellite solid rocket boosters. Riemer spent nearly three decades at Raytheon Aircraft, where he was responsible for product development and airworthiness of all aircraft, including military trainer aircraft and aircraft, and he held leadership positions for the missile business and cryogenic business divisions. He began his career at General Dynamics in the Convair Division as a Thermodynamics Engineer. Riemer holds a Bachelor of Science degree in computer science, with minors in mechanical engineering and finance, as well as a Master of Science degree in mechanical engineering, from the University of Utah.