Additive manufacturing and 3D implants
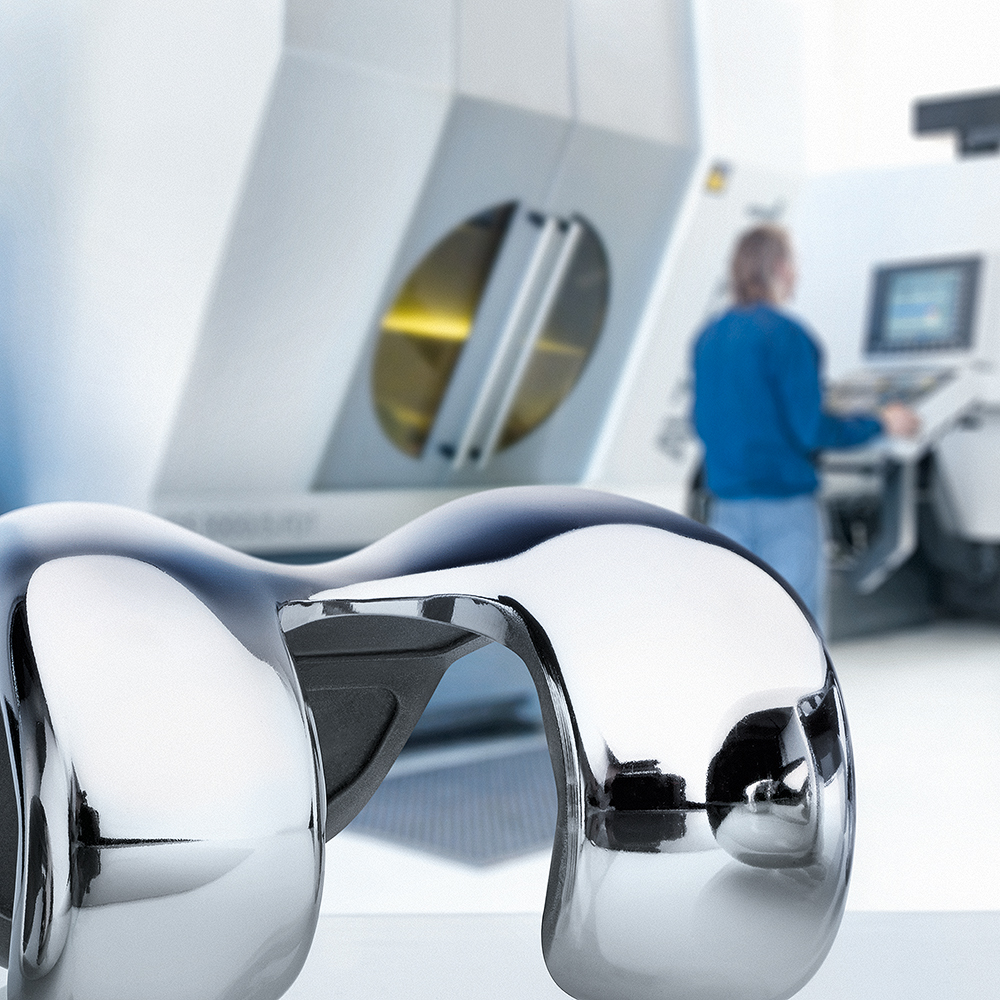
Over the last decade, additive manufacturing, or 3D printing, is continuing to ascend to new heights of innovation in printing layer upon layer in mass volume, repeatable quality and creating products never thought imaginable. Every industry is affected by this manufacturing revolution in parts modernization, including the medical field, which is seeing enormous strides in providing superior strength, longevity and personalization to medical implant technology.
Better matching of implants equates to fewer corrective surgeries. So, Siemens enables an image-to-implant solution that automates manufacturing in an engineering-to-order process for developing and personalizing products and therapies.
Most medical devices design for mass production and produce standard sizes and shapes to best accommodate the mass of patients. Moreover, this process reinforces the traditional concept of an off-the-shelf product and is not supportive of the personalization of design for manufacturing outside the mass customization framework. However, true customization works with the patient’s anatomy, requiring fewer invasive measures.
Ideally designed for 3D technology, medical devices need organic shapes and methods to adapt to personalization – requiring significantly more complicated structures than typical engineering parts or devices. Surgeons can now create knee replacements based upon a specialized template specially designed for the patient’s anatomy with benefits including:
- Improved alignment
- Reduction in bleeding
- Minimization of bone and tissue removal
- Less instrumentation
- Better recovery time
- Decreased pain
- Reduction in the occurrence of infection
The process of customization begins with information garnered from a patient’s CT or MRI scans. This serves to directly migrate into creating tailored devices using distinct multi-sided mesh surfaces for representing efficient processing of intricate organic shapes. Also, this thwarts the incidence of complicated conversion issues, thus improving the integration of surface details.
The stark contrast of mass production to a personalized approach is on full display in the design and manufacturing devices that complement a patient’s unique anatomy. The result is multiple benefits for both the surgeon and the patient.
The entire engineering progression is automated in a process chain for planning, designing and manufacturing patient-specific devices. This is achievable with a comprehensive approach via Siemens’ specialized systems and state-of-the-art CAD/CAM software. Creating implant solutions ensures medical device companies can carefully develop first-rate customizable products and remedies while safeguarding full government and industry compliance regulations.
Additive manufacturing is a crucial ingredient to this recipe, continuing to be a mature option for modern manufacturing and rapid prototyping. It assists in alleviating the complexities with innovative manufacturing of complex surfaces, shapes and automation of CAM and CMM inspection processes.
For example, the creation of internal lattice structures serves to provide lightweight, durable parts and surfaces with increased detailing that enhances strength, functionality and ergonomics. Also, there are improvements to materials, equipment and processes.
Some of Siemens’ most renowned work is the 3D printing technology it produces in tailor-made hearing aids.
Moreover, they are partnering with some of the foremost medical device manufacturers to implement CAD/CAM technology for the effective design and manufacturing of superior tailored orthopedic solutions.
Learn more about the accomplishments of additive manufacturing and medical implant technology.
About the author:
Blake Snodgrass is a writer for the Thought Leadership team at Siemens which supports several venues, including the Thought Leadership Community blog. Blake has a Bachelor of Arts degree in Mass Communications and more than 25 years of experience with roles in technical writing, marketing communications, user-experience design and content development.