Implementing smart manufacturing for a smart factory
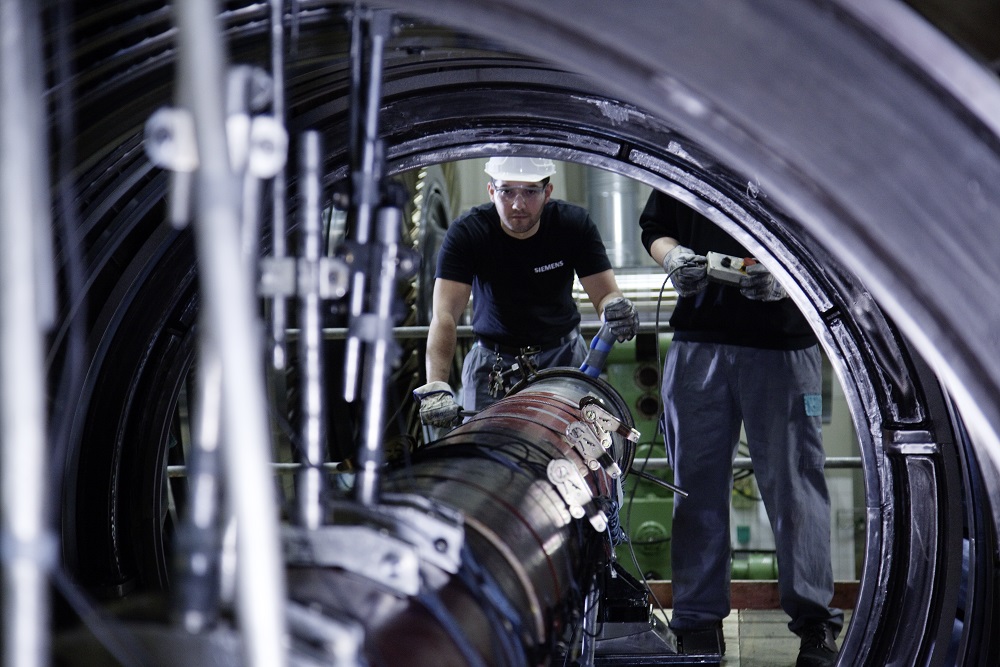
With new strides and technological advancements propelling the manufacturing industry to greater innovations, it’s essential to understand how improving machinery operations is dependent upon making your factory smarter.
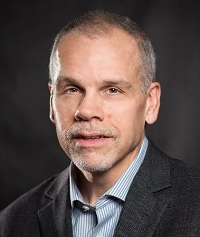
A substantial contributor to this series is our resident expert, Bill Davis, who is the Director of Industrial Machinery and Heavy Equipment Solutions at Siemens Digital Industries Software. Bill’s expertise in this industry expands over 30 years, with 20 years as an engineer.
We continue this topic by having him explain the dynamics of smart manufacturing and smart factories.
Below, is a transcript excerpt from the final portion of this podcast series:
This podcast series stresses the importance of simulation for both the manufacturing environment and the machine build.
Blake (interviewer): A part of taking advantage of being smarter in manufacturing and operations is the assembly layout. For example, you’ve got five machines in one location, ten machines somewhere else, and they’re all very similar, but they also have variance. So, how do you ensure that the correct parts are in the right location on the assembly floor at the appropriate time?
Bill: You need to have a software solution that lets you simulate the machine location on the floor and how to get materials to them. It’s process simulation, which is a novel idea to ensure eliminating high-traffic zones to areas of delay in receiving materials. There’s a need to improve optimization in how the work cell is located, and in the machine builder. However, how do you ensure you’re putting the right materials needed and defined by the manufacturing bill of materials? Also, how do you ensure the materials are arranged on the floor for optimization assembly?
Everything needs to be within an arm’s reach, so it’s not just the shop layout and simulation, but also process simulation. What’s often overlooked are conflicts in the order of operation. Machinery is about putting ten pounds of functionality into a five-pound bag. So, the assembly process is a compromise that’s a result of the design. However, as we look at all the trends towards adaptability, predictability and extendibility, it’s vital to view the human factor for the assembly process and decipher the necessary tools to achieving high quality.
For example, we’ve got a machine assembly that’s inside a frame, and you can’t physically move the torque wrench to get to the right spot, so that’s a quality problem. However, being able to simulate that in the early part of the design process will help us get first-time quality with the ability to make changes when it costs less. So, you can move an element of that frame two or three inches to the right or left and torque the bolt properly.
We need the shop layout capability and process simulation at the human factor level to be aware of problems. Sometimes these problems don’t manifest themselves until there’s a problem in the field. For example, a bolt that seems like it was appropriately torqued can loosen up and cause other failures. However, the root cause is the capability of the assembly process. So, being able to simulate it as part of the design process is crucial for continuous improvement into the development process. And, it’s not just looking at the individual assembly and machine assembly process but scheduling multiple machines and multiple product lines at the same time.
In my previous role, we had high variability in shop floor requirements. One machining center would require a 20 x 20-foot space, and another a
10 x 30-foot space, creating a jigsaw puzzle in terms of the process. There was a physical scheduling challenge throughout the shop in backing it through the part manufacturing. The assembly process for scheduling software capability is vital to know the number of users on each machine and the floor space utilization.
This information culminates in knowing factor acceptance or a side acceptance test. Routinely, a customer comes in and checks out the machine and is elated with its performance, thus signing on the bottom line for us to deliver it. However, simulation can involve the programmer sitting in front of the machine and testing many operating conditions in a stressful environment. The more complex the machine, the higher the probability of not having time to test everything, including the assurance that the machine PLC code meets all requirements.
You need to have software that allows simulating the upfront design process in the software development piece. Thus, simulating the PLC code on the machine floor, running through the use-cases effectively to validate that the codes perform in the way the simulation indicates. You can focus on areas of challenge that you may not be able to simulate, to bring that machine into a commissionable state quickly.
Every time a machine is sitting idle or being tested, it allows time for potential cash. So, the less time in commissioning and debugging, the more rapidly you can get the machine to the customer and perform simulation for movement of parts and kinematics.
These are items performed from an assembly management operations perspective, to drive value for the company and efficiency in generating more cash flow, reducing margin erosion by errors and quality problems. And, none of this could occur without the executable digital twin.
Blake: Do you have examples or use-cases where companies have implemented the simulation and seen a reduction in errors or a reduction in time, while gaining an increase in cash flow? Without mentioning company names, do we have examples of improved metrics?
Bill: Absolutely! So, there’s a company that’s a Siemens customer and software user that is embracing the digital twin in digitalization of their machining and manufacturing centers. Also, there’s a packaging machinery company that builds bags or boxes in packaging a product, whether it’s chips or bags, and putting them into boxes using the digital twin for the design to increase their production speed-building the world’s fastest packaging machinery.
The extra-cost they spent is justified by having the world’s fastest machine and embracing the digital twin for software development, virtual commissioning and software validation. The programmer evaluated the machine, testing it out to ensure it didn’t collide and then hit the go button, moving the pick head to the right, then to the left, colliding with the frame. So, by leveraging our software from an automation perspective, they’re able to:
- Validate that the machine is functioning to perform the required tasks.
- Increase the speed of the machine due to the servo-motor, driving it to greater capabilities.
Therefore, at higher speeds and greater reliability they understand the limits of what the program should be accomplishing and align with the statement from the VP of Engineering that, “they would rather the machines collide in the digital twin than in the real one.”
Therefore, driving that validation verification through the design perspective creates greater efficiency on the shop floor and allows for executing more machines, witnessing a 20 percent improvement in the overall capacity of their machine shop and operations due to minimizing the time previously spent in validation, verification and commissioning. Though that time was not eliminated entirely, it was minimized, so the gains translated to an increase in machines sales.
Blake: That’s a great example, Bill. Let’s move into the quality of parts manufacturing and how Siemens ensures quality through their portfolio of offerings.
Bill: When we look at Siemens Digital Industries Software portfolio of software products, we’re offering design and simulation products, data management of the lifecycle, operations management software and manufacturing engineering software. So, it includes both the CAM piece and the scheduling piece from shop floor management. However, what’s crucial is that we have closed-loop quality. So, we take the information from the management of the digital twin and the component quality, whether it’s a supplier piece or an actual physical piece, and we build that into our manufacturing process. This is merely one portion of the closed-loop operations management quality inspection process.
Also, we can automate the inspection process by linking the coordinate measuring machines to the database so that we can program the inspection points which are critical to quality measurements, translating those back and retaining them into statistical process control documentation. We can handle that from a part process in quality measurements so that incoming material inspections can be handled in the same way as our software. Then, we have software capability to ensure the validation of the process to confirm people are trained in executing it. So, the hallmarks of quality are people, process and product.
It’s important that we talk about these in three contexts – the product itself, the process defined (assembly or machining) and to ensure that people can execute the process and its capability. Therefore, when you have an error, is it an error in the machine’s capability of making the part to the required specifications or is it the inabilities of the person executing the machine in hindering the quality? We need software capabilities in both areas: machine capability and qualified people.
To increase the IQ of your quality process, a closed-loop manufacturing process is what we’re discussing, and it ensures consistency by establishing the digital twin that encompasses the full manufacturing process. This eliminates the risks because it identifies where your critical failure points are to know the critical quality points in the product, trace it back to the process and certify people.
The digital twin provides flexibility and increased efficiency to know that you can’t execute the same thing in the same way every time. Also, you need adaptable alternatives based on research constraints. The digital twin includes the manufacturing process which is crucial for quickly evaluating your alternatives, determining the impact on the schedule and adapting it to the changing conditions on the floor.
Blake: We thank Bill for his contribution to this series. It has been a pleasure to gain his insight and expertise throughout this entire conversation on smart manufacturing and its effect on the manufacturing industry.
We are looking forward to hearing Bill Davis’ expertise on
an upcoming podcast series slated for January 2020 on
advanced
machine engineering solutions.
To learn more about the competitive advantages of smart manufacturing for industrial machinery, listen to all of our smart manufacturing podcasts or begin reading the first blog in this series.
This concludes the final blog in this current series on smart manufacturing and the trends impacting the industry.
About our expert:
Bill
Davis is the acting Industrial Machinery and Heavy Equipment
Industry leader for Siemens Digital Industries Software. His experience and insights
have been acquired from a career spanning 30 years in engineering and
operations management with machinery and heavy equipment companies. Bill
holds a master’s degree in Business Administration from Marquette University,
with a concentration in Operations Management and Strategic Marketing, as
well as a Bachelor of Science degree in Mechanical Engineering from
Milwaukee School of
Engineering.