Why the aerospace industry must adopt condition-based maintenance
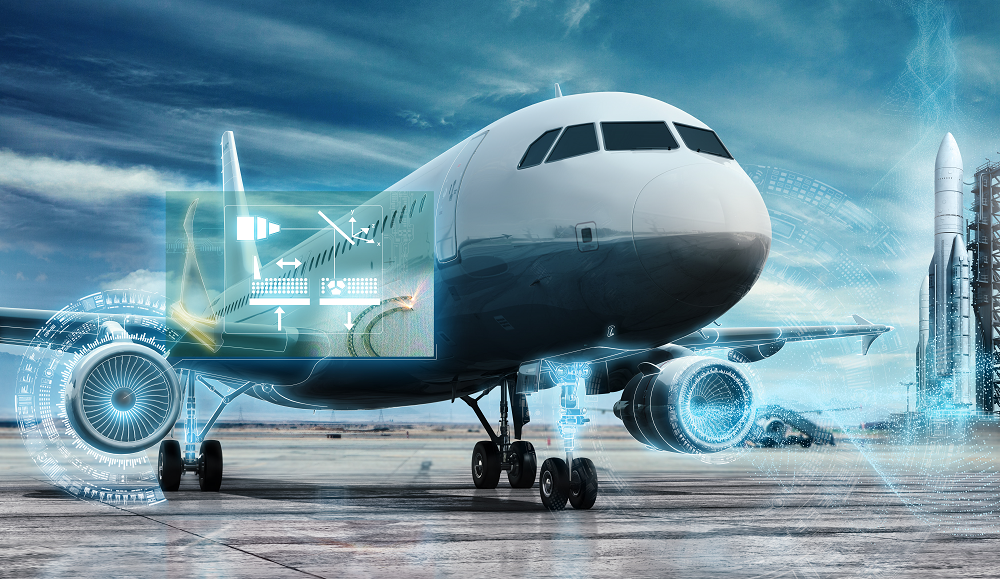
By: Dave Chan and John Cunneen
When the aerospace industry adopts condition-based maintenance and predictive maintenance methods, the cost of owning and operating aircraft is minimized, downtime is reduced and airworthiness is easier to prove.
Unfortunately, many companies seem to simply go through the motions and use antiquated and increasingly unreliable methods to track reliability, and as a result, spend more downtime than needed to conduct unnecessary maintenance. This not only increases costs but more importantly, it places the safety of the aircraft at risk.
In our previous blogs, we discussed the cost of certification and the increasing burdens placed on aircraft companies to prove, through certification documentation, that their aircraft met the government safety standards established in countries and regions worldwide. We also discussed some of the digital tools available to help manage this process, lower costs, decrease time-to-market and increase availability/readiness.
Digitalization can ease the burden of designing and manufacturing an aircraft, but it’s also a pivotal strategy to implement these digital tools to increase the efficiency of maintaining, repairing and operating the aircraft.
Major industries such as maritime and oil and gas are using condition-based maintenance to lower costs and reduce downtime. With the maritime industry, just like the aerospace industry, reliability, availability, maintainability, and safety (RAMS) are key in keeping a maritime fleet operational. A ship’s onboard electrical equipment already includes embedded sensors and can provide insight on temperature, pressure, current power and switchboards. This allows access to real-time information and makes implementing condition-based maintenance (CBM) easier. These sensors conduct tasks such as monitoring for potential defects such as hull corrosion, so shipowners know what spare parts are needed, rather than investing in parts that may sit on shelves unused for years.
A house of cards
An aircraft’s design and safety are like a house of cards. If you change one thing or move one piece, it can impact hundreds or thousands of other things. A spreadsheet is ineffective at recording all the changes and incapable of providing an impact and root cause analysis. The right digital tools allow this information to be stored and shared across multiple locations, as aerospace maintenance and repairs likely won’t occur in one single location.
Accessing correct information is critical as 70 to 80 percent of the cost of ownership of an aircraft is in the maintenance burden. Reducing or optimizing maintenance in any capacity lessens the burden while increasing aircraft availability. In fact, maintenance has become such a major, long-term investment that manufacturers are starting to make maintenance part of the acquisition package and finding not only an additional revenue stream but gaining access to data they can use for future design and development.
Aerospace systems are becoming more complex and the identification of all the risks becomes increasingly important. Manual processes are becoming obsolete as the challenge to manage and trace the relationships among millions of components becomes impractical outside of a model-based system engineering environment.
Managing the airworthiness process within the digital thread gives maintainers the capability needed to assist the process in verification and validation to ensure safety and reliability, such as:
• Tracking modifications
• Keeping record of suitable parts, but not original parts being used
• Predictive maintenance and troubleshooting effectively
• Closing the loop between “designed” reliability and “demonstrated” actual reliability in the field
Just like airworthiness needs to be considered in all parts of the design phase, the same holds true for aerospace maintenance and repair phases. The digital thread puts every aspect of aircraft design, manufacturing, maintenance and repair in a single integrated process that can close the loop on FRACAS (failure, reporting analysis, and corrective action system). This integrated digital process helps identify the predicted failure points and provides feedback to the required activities to ensure aircraft safety and reliability. And as a functional digital twin of this system, the owner-operators can take data from the assets in the field and determine if the aircraft or part is actually getting the reliability it’s expected to get. If not, further analysis can be completed and the maintenance schedule changed.
Using data to determine maintenance
There’s a significant amount of data available in an aircraft, but how can maintainers use it to improve aerospace maintenance and repair procedures? It’s more than collecting data from the aircraft; it must include external factors like weather, temperatures and other environmental conditions. The dry, extreme temperatures of Phoenix in the summertime will impact parts differently than frigid winter conditions in Alaska.
Big data and IoT information can identify all the data from an aircraft, but it’s not a matter of taking the 800,000+ data points and giving it to data scientists hoping they’ll find the areas of impending failures. At the core of it, you need a model that will identify, analyze and define the data.
With a fully integrated digital enterprise solution, aerospace companies can achieve greater benefits from the digital tools to develop their aircraft systems and take advantage of its ability to digitally predict the associated risks. Safety and reliability tracking is becoming too complex for traditional manual processes, which is why having a fully integrated digital enterprise is key to link everything in design and development to verification and validation to predictive maintenance.
Legacy platform systems analysis was performed independently and not within a systems engineering approach, and many of those experienced engineers have already left or are getting closer to their retirement phase. The upcoming maintainers simply don’t have the experience as the older people do as aircraft are becoming more complex. It’s a major safety crisis as these two paths converge.
If the aerospace industry can use the digital tools for condition-based maintenance and predictive maintenance, they can ensure aircraft continuously meet airworthiness and are ready and available when needed.
For more information on Siemens A&D software and solutions, please visit our aerospace industry blog.
(This blog post was created with material provided by Chris Stecki, CEO of PHM Technology.)
About the authors:
Dave Chan is a technical account manager supporting the aerospace, defense and federal business for Siemens PLM Software. His career with Siemens PLM Software started in 1996, and he has driven customer success with the adoption of digitalization and digital engineering solutions for numerous commercial and federal customers. Dave has been in the engineering software business for more than 22 years. He has a bachelor’s degree in industrial engineering degree from Lehigh University.
John Cunneen is a business development consultant for Siemens PLM Software’s Aerospace, Defense, Federal, and Marine division. He leads efforts to uncover, develop, and respond to industry and government requirements pertaining to all aspects of product and system lifecycle management and provides thought leadership to customers. John has been an avid general aviation pilot since 1987, earned a Bachelor of Science in aerospace engineering from Arizona State University in 1989, and has been a key part of Siemens PLM Software since 1999.
Comments