Benefits of additive manufacturing in design
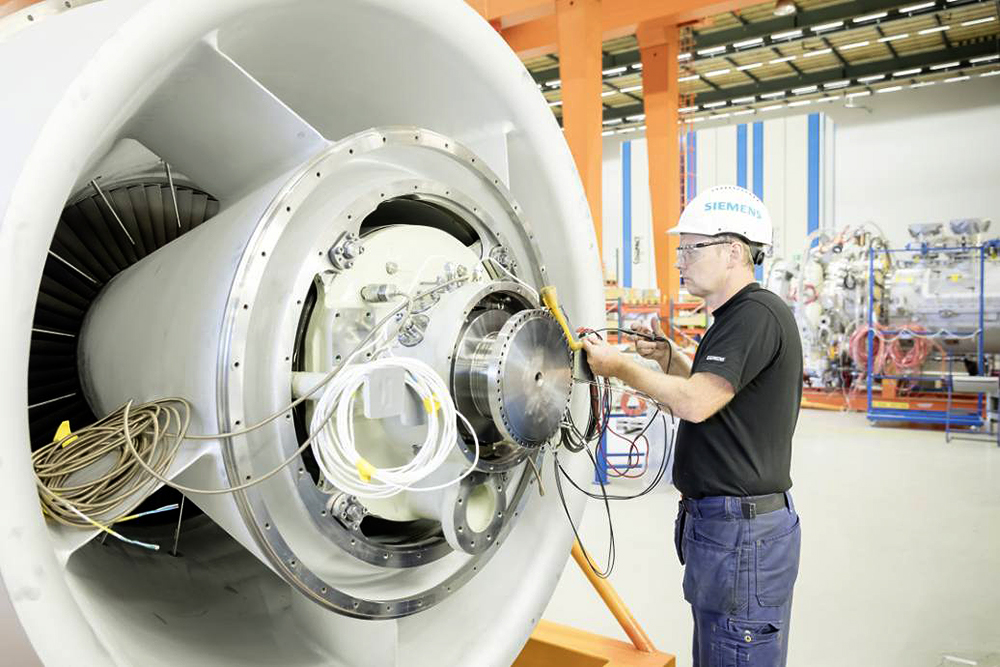
The benefits of additive manufacturing (AM) are clearly seen at a centuries-old factory in Finspång, Sweden where technology is entering the modern industrial age with gas turbine production, prototyping spare parts on-demand and burner tip repair.
Additive manufacturing technology is showcased in this specialized, automated facility producing world-class, efficient and reliable gas turbines, with 95 percent of production being exported. The beauty of this setup is everything in one place for comprehensive design, production, testing and aftermarket support.
Design benefits offered by additive manufacturing
The original turbine burner head design called for 13 individual pieces to be machined and welded together. The resulting burner was roughly 800 mm in length and was built using a complicated manual manufacturing process.
As the Siemens team in Finspång gained knowledge about the additive manufacturing process, it envisioned other uses for the technology. Engineers investigated a complete redesign of the burner head that could consolidate the 13 individual parts into one single unit and considered how they might incorporate special features that could only be additively manufactured.
One essential requirement of burner design is a low mass. By designing for additive manufacturing, the team found that the burner walls could be made slimmer for improved temperature responsiveness and that lattices could be introduced to make the burner stronger at a lower weight, resulting in less thermal inertia. The lattice structure inside the tip also allows for more effective cooling of the burner tip.
The additive manufacturing design delivered a stronger, more agile product for the turbine’s heating and cooling cycle, enabling less aggressive heating and cooling routine. This increases the burner’s lifetime and lessens the oxidation and crack formation which typically damages burners. The team also achieved a 22 percent weight reduction and is working to further refine the design to attain a 50 percent weight reduction.
As the Finspång team’s knowledge of additive manufacturing evolves, its ability to take advantage of the technology’s potential continues to grow.
“I can compare this technology with a snowball. As you form a snowball, it gets bigger and bigger,” said Vladimir Navrotsky, technology and innovation manager of Siemens Service Distributed Generation and Oil and Gas. “There’s a positive enhancement with this ball. The same can be said about additive manufacturing enabling at the same time enhancement of the components’ functionality, design and manufacturing time reduction, materials reduction, and component lifecycle cost improvement.”
The state of the art: industrializing additive manufacturing
As additive manufacturing capabilities at the Finspång facility evolved, it became clear that true industrial production would require more than just adding new machines to boost production volume.
The Siemens team quickly discovered that to repeatably produce high-quality parts required a well-defined process, with a strong software foundation. As the AM process moved from prototyping to repair and through production, the software was key to industrializing the AM process.
The software was the catalyst that allowed the team to design the energy products that will be required in the future at the required volume. The use of Siemens NX Additive Manufacturing software, combined with process knowledge from years of prototyping and repairing burners, enabled the team to produce redesigned, quality burner parts at scale.
Moving from prototyping and repair to production required a large investment in new production facilities and hardware, as well as investments in the software required to run those machines and ensure that the production process adapted smoothly to the new demand. Not only were multiple Siemens software offerings used in the design and manufacturing process, but Teamcenter managed the part and process data. This helped the process to expand and adjust as the facility’s needs grew.
The software’s reach extended from the initial design to shop floor management, wherein the manufacturing operations management software tracked material usage, ensuring that the right mix of new and recycled materials was used for the process at hand. These complex software setups were necessary to run a cost-effective, efficient operation.
“At our facility in Finspång, we truly have a real digital thread all the way from upfront design to the manufacturer on the shop floor,” said Dave Madeley, senior strategist and additive manufacturing key expert for Siemens.
The integrated software system allowed the Finspång engineers to reimagine the burner design with an additive manufacturing mindset and to produce burners with the required quality for such a demanding application. As the volume increased to meet production needs, simulation tools and shop floor execution software became lynchpins in the operation. Without the backing of proper software, the evolution from prototyping to serial production would not have been possible.
The adoption of additive manufacturing: lessons learned
With a greater understanding of additive manufacturing, Siemens is more empowered to engage with other industries and customers to find the software they need based on the revolutionary work being done at Finspång.
Collaboration was key to developing the additive manufacturing process and technology to repair gas turbine burners. By removing internal barriers, collaborating through technology and developing trusted partnerships, a path was paved for innovation. Siemens believes that what was done at Finspång can help other industries advance their additive manufacturing operations on an industrial scale.
“With technology as new as this, and that’s moving as quickly as it is, it makes sense to form working relationships with other companies that are near the same development stage as you,” Madeley said. “It makes sense to form an ecosystem to connect people.”
The work at Finspång continues to prove how revolutionary additive manufacturing can be. It is now a matter of taking this knowledge and experience into the design of full gas turbine components or subassemblies. The process of moving not just a manufacturing operation, but also a design organization and shop floor operation, from prototyping to production, is an experience that Siemens believes will pay off throughout the company.
Additive manufacturing integration will also provide new delivery methods and solutions to companies. Siemens’ work manufacturing products at an industrial scale can help companies to better understand their machines’ ability and capacity to print, as well as to understand the knowledge required to ensure the necessary support is available wherever additive manufacturing systems are operational.
There are many complex problems facing the industrialization of additive manufacturing. However, technology is an important part of the fourth industrial revolution, or Industry 4.0. From a cost perspective, whether it is used as a rapid prototyping tool or as a manufacturing technology on an industrial scale, the potential benefits are monumental, and companies across the world are working to understand the role additive manufacturing will play in their processes.
“The worst thing a company can do is nothing, because additive manufacturing and, in particular, industrial-scale additive manufacturing, will make organizations of all sizes more competitive,” said Andreas Graichen, group manager for the Additive Manufacturing Centre of Competence at Finspång. “Products will be built and manufactured faster, smarter, stronger and, in some cases, at a lower cost”.
This concludes part three in a series on the industrialization of additive manufacturing at the factory in Finspång, Sweden – where today meets tomorrow. In part four we will be will discussing the vision and future of additive manufacturing. View the additive manufacturing overview of this series.