Cloud-based simulation can simplify automation complexity
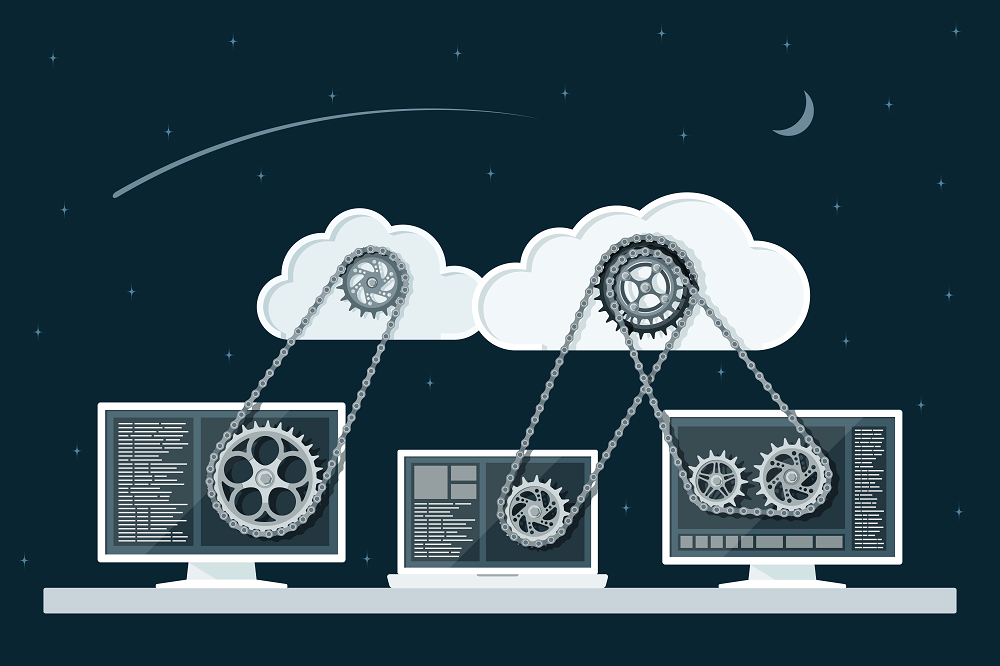
Today’s digital tools and technologies deliver incredible opportunities to manufacturers, but they also introduce enormous complexities into production processes.
Over the years, digital simulations have become a valuable tool used to plan and verify production processes and plant-floor scenarios. Manufacturers use digital simulations across a wide array of industries and for a number of technologies, including robotics, industrial-scale additive manufacturing and automation inside factories and warehouses.
Unfortunately, desktop simulation software, while still valuable, has compounding limitations. In many cases, organizations wind up relying on manual processes—or at least a combination of the manual and automated processes—and don’t unlock the full value of digital technologies.
Another complication is that process simulation increasingly spans different teams and groups, and older software was not designed for this higher level of collaboration and communication. This legacy approach can also push the boundaries on cost constraints, as older systems can be costly to keep up and customize.
Cloud-based simulation is more flexible, scalable and simpler
It’s no accident that the cloud has rolled into the mainstream of business, and the story is no different in the simulation space. Cloud-based applications or services simplify process planning and testing, particularly as manufacturers migrate to an Industry 4.0 approach that encompasses both business and IT.
Cloud-based applications provide endlessly scalable data storage and computing resources. These can be ramped up or down quickly and dynamically, and an organization can customize programming tasks using a platform-as-a-service approach with equipment partners. This makes it easier to create customized production plans rapidly, and as soon as they are required. The result is less downtime for planning and verification.
This approach also delivers an intuitive interface that mimics what consumers have come to rely upon for banking, streaming entertainment and intelligent helpers in their homes. This simplifies processes but also helps a manufacturer deal with nettlesome issues, such as catering to a customer’s specific needs, optimizing global factory assets, and ratcheting up quality control and production efficiency.
Value and connectivity in one platform
Many companies develop point solutions on their own. Often these are standalones without good connectivity to other elements in the process—essentially niche solutions with narrow domains and unique requirements, such as specialized robots or automation concepts.
In contrast, a cloud-based process planning and simulation environment offers a platform for partners and stakeholders to share data, provides a common and standard solution for manufacturers and allows almost anyone to develop solutions and customize apps to specific needs. For companies that have tried to go it alone with siloed solutions, a cloud-based solution can add value to their processes and to their customers by bringing all elements together in one platform.
Transforming simulations
As automation systems become smarter and more flexible, manufacturers reap massive benefits. A RightScale 2017 State of the Cloud Report found that 62 percent of companies using the cloud realize faster access to infrastructure, 58 percent achieve greater scalability, and 56 percent gain higher availability.
More intuitive simulation via cloud-based application interfaces translate into clear benefits as well.
• Reduced human resources costs. It’s no secret that today’s workers, particularly young people, are attracted to innovative and progressive companies. An established industry leader is more likely to attract talent. However, cloud-based process simulation provides other benefits like reducing training costs because cloud-based applications have a more intuitive interface: new employees can learn the technology faster.
• Faster and better production cycles. Organizations using cloud-based digital simulation work faster and more effectively. These manufacturers achieve integrated workflows and more connected data. They also achieve always-on services. Cloud-based applications are up and running at all times, and they are always up-to-date because upgrades and patches take place in the background and don’t interfere with tasks. This approach offers an additional benefit of improving security. Any bug or vulnerability is patched quickly.
• More advanced process analytics. The cloud provides the data storage and computation power needed to run fast data-heavy predictive analytics. The outcome is more detailed and delivers faster simulations across a broader landscape of scenario planning. Pushing the boundaries on process planning opens the door to additional opportunities to pinpoint lower-cost along with more specialized production methods.
• Improved precision in planning and analytics. Organizations that use cloud-based digital simulation methods typically reduced downtime and scrap rates, as well as improved safety with less required human-machine interaction.
Because manufacturers of all shapes and sizes must deal with growing demand for customization and a growing need for speed, efficiency and cost controls, a cloud-based approach to simulations make sense—while delivering dollars. A cloud-based simulation approach drives business process improvements that span quality, costs, safety and security.
This concludes our series on why companies should consider implementing and leveraging cloud-based simulation. Click here to learn more about the topic.
About the author
Gil Chen is passionate about innovative thinking and execution of out-of-the-box ideas. In his current role at Siemens, he leads experiments around Industry 4.0, the factory of the future and innovative manufacturing processes, with robotics and automation systems as his focus and robotic simulation for the automotive industry as his main expertise. He has more than 25 years of experience in PLM in dominant market players and feels lucky to support complex manufacturing challenges and leverage his knowledge to teach others.