Barriers to adopting additive manufacturing (Part 1)
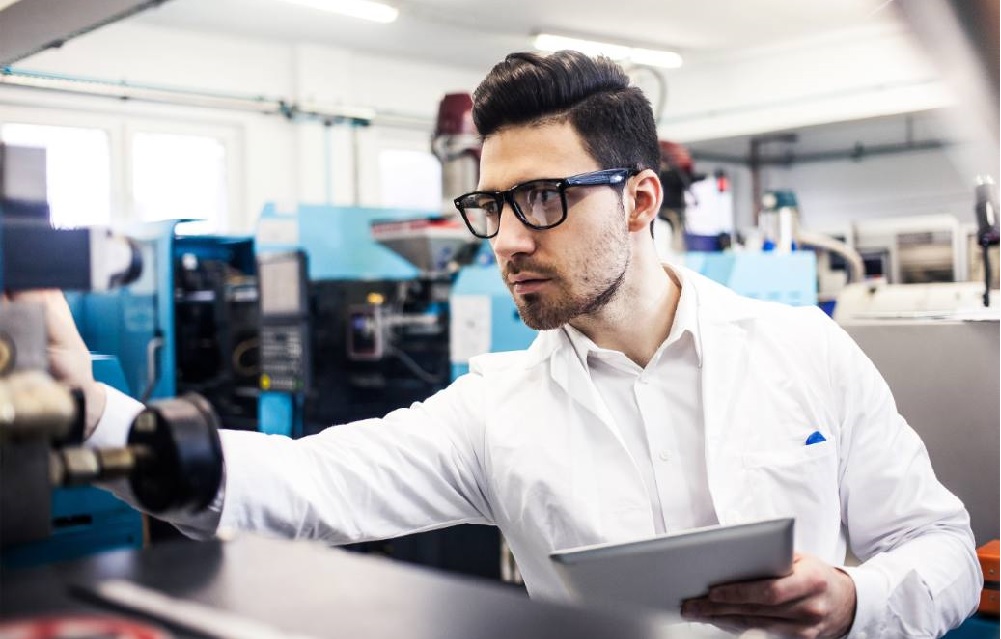
The adoption of additive manufacturing contains tremendous amounts of untapped opportunities for a broad swath of markets, and expectations are very high. The next generation of additive products will be driven into new frontiers of performance and mass individualization. And they will be produced using innovative flexible manufacturing capabilities, capable of supporting a more distributed manufacturing model that will unlock other new business models for companies. However, for this to become a reality, there are some fundamental capabilities and changes of mentality needed to achieve the full potential of additive technologies.
Additive and new possibilities
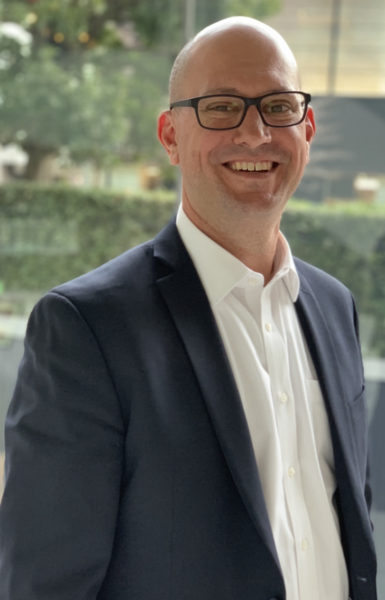
We’re turning a corner with companies beginning to understand what’s possible in additive manufacturing. But for most manufacturers, this will be a process that will take time to navigate as they build up their additive knowledge. For many companies, the first step is to leverage additive when prototyping new products. What is encouraging is we’re witnessing more of these additive prototyping projects being transitioned into full scale manufacturing applications for more extensive production operations.
These types of applications fall into various categories. For example, some companies are looking at leveraging additive from a part consolidation perspective, taking multiple parts and combining them into a single production part that requires a complicated geometry not possible using traditional manufacturing methods. Another area is individualization and personalization of products in higher volumes, most noticeably in the healthcare arena.
Also, companies are deploying additive to improve the performance of the end-product. Lightweighting is a prime example – creating lighter, streamlined, more robust parts or products. Moreover, additive manufacturing could be used to improve thermal and flow optimization. Companies are making their initial forays beyond prototyping into additive for tooling and production aids that enhance their manufacturing operations on the shop floor. And, instead of outsourcing these components, companies are finding they can use 3D printing to produce parts faster, with the strength per the requirements required on the shop floor to further enhance production levels.
These emerging performance capabilities are fueling an interest in printing manufacturing over the past year. Processes like printing tooling give companies an entry point into experimenting with more production-related additive capabilities. It’s now possible to print several jigs and fixtures, working on their output quality, experimenting with materials and their processes without putting the delivery of an actual product at risk. Subsequently, it’s a powerful way for a company to build up a knowledge base and iron-out its additive process without incurring high levels of risk. Even with this progress, the adoption rates of additive manufacturing technologies still seem to be encumbered by numerous extenuating factors.
Moving to higher levels of adoption
For the market to achieve full adoption of additive manufacturing, the industry must address three challenges that hinder its growth. First is to actively overcome the change-resistant culture that exists in so many manufacturing organizations. This mentality sometimes reside in the executive leadership, but not always. Oftentimes upper management is very enthusiastic about additive. So it really comes down to resistance at the program and project leader levels, which makes sense, since they are responsible for delivering products to the market and managing the costs. Being on the frontline and meeting deadlines, they can’t afford the risk. Their current process works, so why fix it. Therefore, it’s essential to focus on helping companies change their culture and perspective up and down the management chain with regards to additive manufacturing.
Secondly, there’s an essential need to contend with inefficient project workflows. We see many additive projects today, where companies are not only trying to get up-to-speed with both additive software and hardware – some are even attempting to connect multiple applications together from various vendors, often leading to a painful to transfer of data between these applications. Whenever a change of this magnitude occurs, the difference and the cost of making the change is magnified by a ripple-effect running through disconnected applications that don’t communicate, thus creating a waste of additive projects.
The third challenge it is contending with a lack of immediate meaningful benefits. If there is a hiccup in a process, we’re seeing costs increase for a company’s time, which can linger and sometimes even compromise product performance. This occurrence casts doubts on pushing additive forward because the results don’t materialize in the short term. Therefore, it becomes difficult to justify the organization’s advancement of additive and its adoption.
With our Xcelerator suite of products, Siemens Digital Industries Software has put in place an approach that helps nuture the adoption of additive, providing an end-to-end additive software process to speed the transition to addtive manufacturing. Morevover, we recognized that Siemens cannot do this alone. That’s why we have built a vast network of partners, both within Siemens businesses and across both software and hardware industries in the market, all focused on building an ecosystem based on our customers’ needs and their strategic endeavors.
When you show companies in the industry useful, real-world examples that focus on tangible benefits of additive for product development and production, a change in thought occurs about the value of additive. I am confident that we will see the momentum begin to shift from resistance to acceptance as we promote more examples of positive results.
This is the first blog in a series by Aaron Frankel, providing his expertise on the challenges of adopting additive manufacturing in a changing industry. We look forward to providing more of his insight via blogs and a podcast series.
Related Links:
– Podcast series: Additive manufacturing – an industrial revolution (Part 1)
– Podcast series: Additive manufacturing – an industrial revolution (Part 2)
– Barriers to adopting additive manufacturing (Part 2 – Blog)
– Barriers to adopting additive manufacturing (Part 3 – Blog)
– Barriers to adopting additive manufacturing (Part 4 – Blog)
– Virtual Additive Manufacturing Experience
About the author:
Aaron Frankel is vice president of Siemens additive manufacturing software program. He has over 20 years of experience in the PLM software industry and has held various positions in engineering services, product management, and marketing – all focused on helping manufacturers take advantage of the latest digital design and manufacturing technology.