Barriers to adopting additive manufacturing (Part 4) – open territory, technical challenges and design
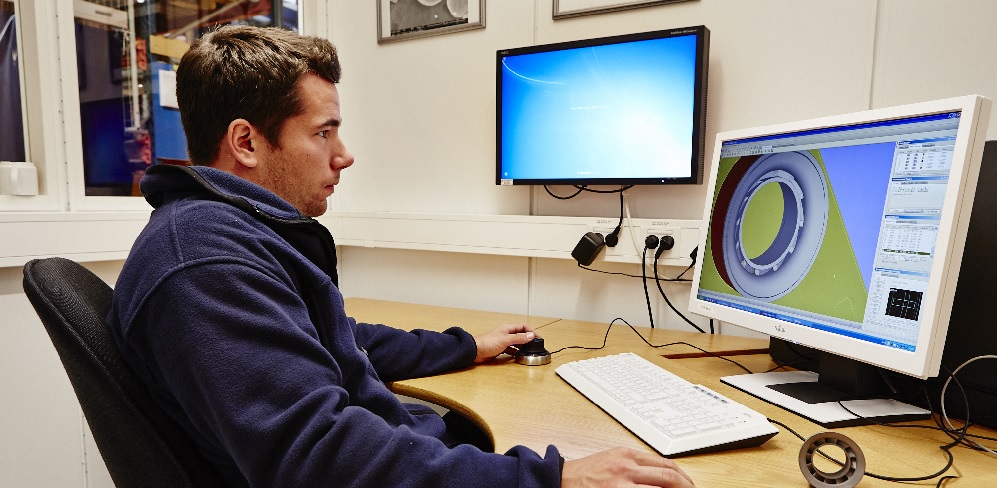
In parts one, two and three of this series on the barriers to adopting additive manufacturing, we discussed some of the industry’s challenges that hinder the full adoption of additive manufacturing. We also visit the Virtual Additive Manufacturing Experience Center where you can witness the additive manfacturing process in action virtually or physically.
In this fourth blog, we discuss how additive manufacturing (AM) or 3D printing is a greenfield of opportunity – it’s brand new.
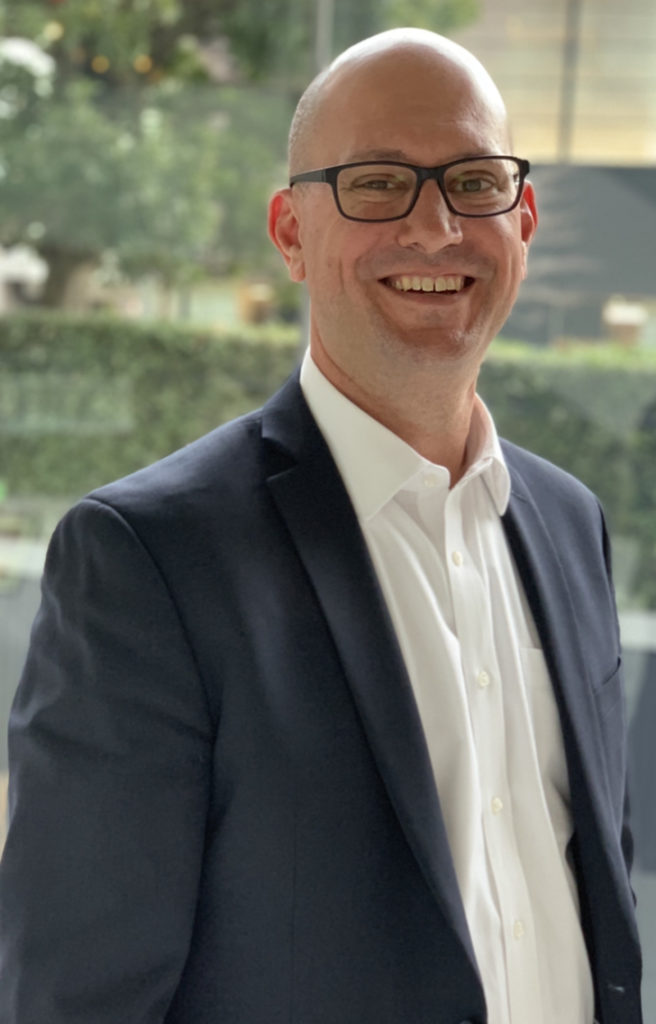
It’s rare to work on a technology where almost everybody’s at the same level of knowledge – learning from scratch. It can have a game-changing impact on numerous industries. Additive manufacturing helps companies transform the products they offer to the market, including their manufacturing process, supply chains and how they produce products. Ultimately, it helps companies achieve a new type of business model – transformative, with value by the company that delivers and offers access.
Additive manufacturing’s potential impact is exciting. As engineers, this potential, combined with the numerous industries, motivates us to develop and offer capabilities and solutions for an inspiring space to work. This mindset includes design tools and engineering development from a simulation perspective – its manufacturing, production and data analytics.
It’s digital technology. We have tools at our fingertips to re-imagine products in a digital environment and realize them in 3D. It’s fascinating. This potential drives us to wake up in the morning and see what’s going on, including working with a vast community of experts with a broad knowledge of various disciplines. We are continually learning more, which continues to motivate us.
Additive manufacturing – technical challenges
However, with exciting new technologies come several technical challenges. These AM barriers can hinder a company from scaling up to additive for production use – and they’re facing these areas all across the process, from idea to service. So, our vision for additive manufacturing is a direct result of the feedback that we’re getting from customers about these challenges.
We are addressing severe problems. The predominant obstacles include design, virtual production and realizing the parts to produce while servicing those parts. Customers want to know if a part is viable for additive manufacturing and design the ideal functional part.
This need evokes many other pertinent questions, including:
- How do we address the massive, costly potential of different types of materials for parts?
- How do we ensure that our parts are qualified?
- How do we minimize the high-failure rate of 3D printed parts?
- How do we scale up the volume to hit the parts’ demand and the quantities of parts?
- How do we orchestrate production in an additive manufacturing factory that requires 3D printers and post-processing equipment?
- How do we connect all of the different pieces of equipment on the shop floor?
- How do we automate and improve additive manufacturing factory efficiency?
- Can we detect when a problem occurs on the printer, and what to do about it?
- Can we collect the machines’ data to analyze the process where parts are being produced and determine the quality during inline part production?
These questions can be summarized by asking how to deliver quality design for additive parts on time and at scale. The answer lies in addressing the many challenges through industrial-strength capabilities that ultimately enable customers to use additive manufacturing in a production environment. As we continue working with customers to develop solutions, we are also developing projects to ensure they deliver value to their parts’ exact geometry.
Additive manufacturing value – optimal designs
Additive manufacturing delivers tremendous value when companies use it to produce new designs that offer significant functionality and personalization. Simulation-driven design tools provide improved products with enhanced functional performance, effectively helping engineers automate the parts and shapes to achieve target performance objectives. These solutions automate parts’ design and engineering to optimize mass and strength, including thermal and flow characteristics.
Siemens is looking to combine performance with production cost and material utilization optimizations. This arrangement provides a positive impact on the product’s performance economically – promoting the ideal functional parts’ designs. To leverage these capabilities requires defining how to create and engineer the design (within the system), including digital representations of the product and CAD assemblies. This includes designing optimal parts for products without CAD geometry via reverse engineering tools that scan products to determine the design envelope for a part. Subsequently, it results in the same automated capabilities to produce the design and shape to deliver the targeted performance objectives.
With our Xcelerator suite of products, Siemens Digital Industries Software brings the industrial additive vision to life, providing the know-how to the additive software process to create parts and products once thought unthinkable. Within businesses across both software and hardware industries, Siemens’ significant network of partners focuses on building an ecosystem around the customers’ needs and strategic endeavors, concentrating on industrializing additive manufacturing.
This is the fourth blog in a series by Aaron Frankel, providing his expertise on additive manufacturing in a changing industry. Check out more blogs and podcasts discussing additive manufacturing and how it’s going to transform our world.
Related Links:
– Barriers to adopting additive manufacturing (Part 1 – Blog)
– Barriers to adopting additive manufacturing (Part 2 – Blog)
– Barriers to adopting additive manufacturing (Part 3 – Blog)
– Podcast series: Additive manufacturing – an industrial revolution (Part 1)
– Podcast series: Additive manufacturing – an industrial revolution (Part 2)
About the author
Aaron Frankel is vice president of Siemens additive manufacturing software program. He has over 20 years of experience in the PLM software industry and has held various positions in engineering services, product management, and marketing – all focused on helping manufacturers take advantage of the latest digital design and manufacturing technology.