White paper: Advanced machine engineering transforms the machine building industry
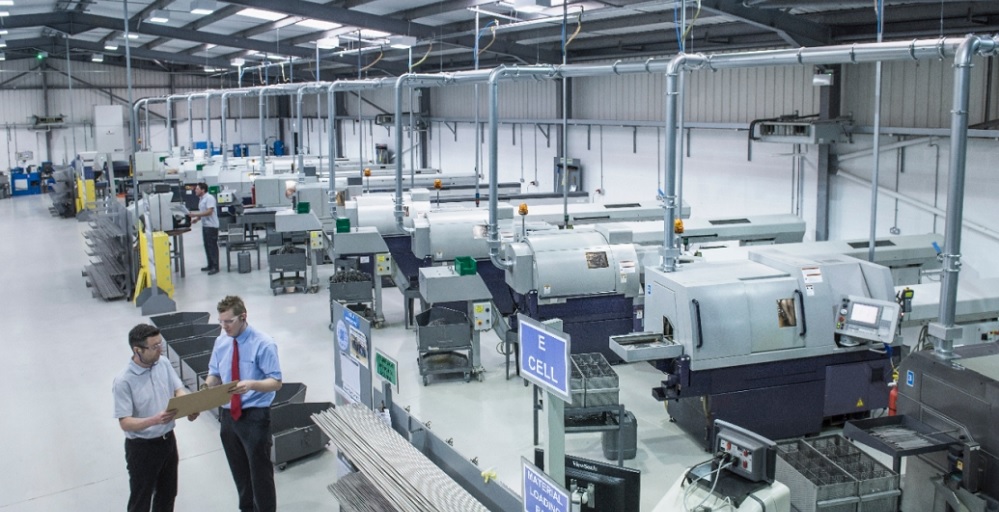
With machines becoming more sophisticated, equipment builders have the challenge to meet cost, quality, timing and functional requirements essential to their customer’s needs.
Machine complexity is also increasing, with a wide array of domains for designing intricate devices, including mechanical, hydraulic, pneumatic, electrical, electronic and software. The relationships between these domains include the diverse implementation of business models by machine builders to further meet essential needs.
Fully supporting products throughout their lifecycles necessitates having digital thread connectivity from concept to completion. Machine complexity requires a guarantee of clear, concise and valid data, with advanced business processes like simulation and virtual commissioning to validate products before building, thus reducing costs and risks during physical commissioning while also improving profitability for machine builders and customers.
Implementing a multi-disciplinary design
Machinery design is determined by mechanical parts, assemblies and modern CAD tools. The energy to operate machines is provided by electrical power, with software-driven electronic system variations to govern sophisticated, changing processes.
Electric motors and control devices are at the core of most modern machines due to their efficiency and sustainability. Complex machines use microprocessors and software to manage sophisticated equipment that includes controllers and sensors. Most machinery applications are configured from commercial off-the-shelf (COTS) components. Then software creates the logical and physical design using schematic diagramming with a CAD application.
Also, embedded software operates on machine controllers in real-time, interfacing and controlling the physical operation. Then desktop computers manage machine modules and production lines, providing local reporting and analysis. This process feeds data to the factory and enterprise-level applications through sensors and the internet of things (IoT).
Using machine design business processes and configuration management
A modular design confirms that the interface between modules is consistent for increasing the capability or capacity. The mechanical and physical domain connection points need to match; therefore, the input and output of a module must meet those connecting requirements. So, while the electrical side wiring harnesses must connect, it’s also essential that the electronic signals and power conductors align. Confirming that the embedded controllers operate as a single unit across modules without adapting each installation’s software is critical.
Another essential element is configuration management (CM), which verifies that the correct part revisions are listed in the bill of materials (BOM) while also confirming the drawings delivered to manufacturing and suppliers possess matching revision levels in the parts. This process can result in design, production and operational issues.
Performing correctly the first time is always more efficient than doing it over. In CIMdata’s consulting practice, they witness many errors that trace back to poorly defined and managed configurations. This scenario causes incorrect versions of parts or software, furthering failures or mistakes. Products include supply chains, operating condition variability and design complexity from non-mechanical domains, making the process more difficult for companies to understand. Therefore, configurations have many interconnections to manage and comprehend. Several hurdles common to this process include dealing with regulatory, safety and cost issues.
We live and work in a highly competitive economy, forcing product manufacturers to improve via machine and information technology implementation. Thus, machine and equipment builders struggle to address customer demand’s cost, quality, timing and functionality requirements. Beyond the core multi-disciplinary design and configuration management support, there is a need for end-to-end virtual commissioning and the simulation of controllers and software necessary to support it. All these capabilities corroborate, for more time available for innovation to ensure customer satisfaction and machine builder profitability and success.
View the CIMdata white paper for more information.
Attend webinar to learn more about the Advanced Machine Engineering solution and how a virtual multi-view BOM approach can provide early product validation and verification and improve all areas of machine design and manufacturing.
Siemens Digital Industries Software is driving transformation to enable a digital enterprise where engineering, manufacturing and electronics design meet tomorrow. The Xcelerator portfolio helps companies of all sizes create and leverage digital twins that provide organizations with new insights, opportunities and levels of automation to drive innovation.
For more information on Siemens Digital Industries Software products and services, visit siemens.com/software or follow us on LinkedIn, Twitter, Facebook and Instagram.
Siemens Digital Industries Software – where today meets tomorrow.