Replacement manufacturing with additive
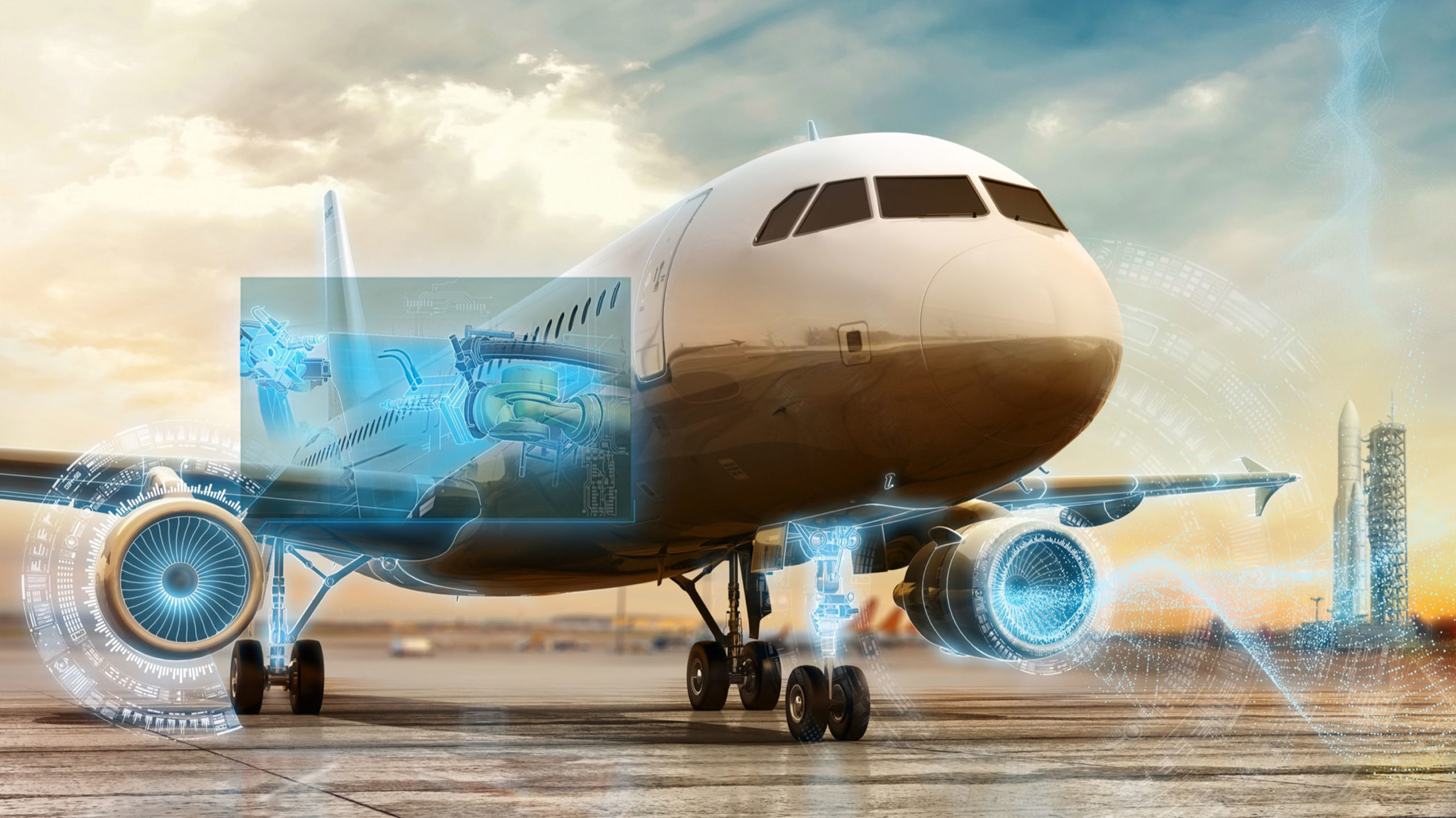
In an article from Aviation Today, Woodrow Bellamy III brings up an interesting facet of additive manufacturing (AM) that is growing within the aerospace industry – replacement manufacturing. Aircraft are already being designed with an emphasis on AM components, General Electrics Aviation’s GE9X engines are expected to take off in 2022 with 300 3D printed parts, Dassault’s Falcon 20G already uses 3D printed bearing housings and many other companies are working on how to implement the technology into their new aircraft, but some are looking backwards for inspiration.
Airbus’ passenger A320 took to the skies over 30 years ago and while many are still flying just fine, replacement parts are becoming harder to find. To deal with this shortage, one of Airbus’ subsidiaries – Satair – looked to AM as an answer. As Airbus could not receive replacement wingtip fences on the A320 from the original manufacturer of the casted parts, Satair chose to make them in-house with AM.
The next step was recertifying the part in titanium, a common metal used for AM in aerospace. This process still took less time than waiting out the supply woes. And in the future, with more widespread adoption of AM, this process could be condensed making AM replacements a more beneficial route to aircraft OEMs. Without needing to hang on to bulky casting materials, and OEM could theoretically repair any aircraft it makes while maintaining a lower operating budget.
In the future this could even mean that aircraft hubs deploy a fully commissioned printer on-site to replace worn parts. But more important in the short term is that more AM parts are being qualified for use and faith in the technology is increasing. Eventually the more ground-breaking technologies will be able to find widespread adoption – internal lattices for light-weighting, topology optimized parts for efficiency or part-consolidated sub-systems to reduce overall complexity.

“Our software is being used to design parts from standard brackets, to airframe components, to jet engine components and systems. When it comes to additive, aerospace companies are utilizing the technology for some very innovative solutions to complex problems. These innovations are enabled by the way that additive allows for the manufacturing of very complex geometries with the pinpoint precision necessary in the aerospace industry.” -Aaron Frankel, Vice President of Siemens’ additive manufacturing software program
“Additive offers the potential to reduce weight and improve part functionality, for example, the reduced pressure drop in hydraulic systems or improved efficiency of engines. The development of greener aircraft could also benefit from the possibilities that additive manufacturing offers as some technical solutions might be so complex that they cannot be manufactured by conventional machining.” – Felix Hammerschmidt, head of additive manufacturing solutions for Satair
Siemens Digital Industries Software is driving transformation to enable a digital enterprise where engineering, manufacturing and electronics design meet tomorrow.
Xcelerator, the comprehensive and integrated portfolio of software and services from Siemens Digital Industries Software, helps companies of all sizes create and leverage a comprehensive digital twin that provides organizations with new insights, opportunities and levels of automation to drive innovation.
Also, for more information on Siemens Digital Industries Software products and services, visit siemens.com/software or follow us on LinkedIn, Twitter, Facebook and Instagram.
Siemens Digital Industries Software – where today meets tomorrow.