The effects of COVID-19 on the automotive industry: The Future Car bonus episode with Nand Kochhar
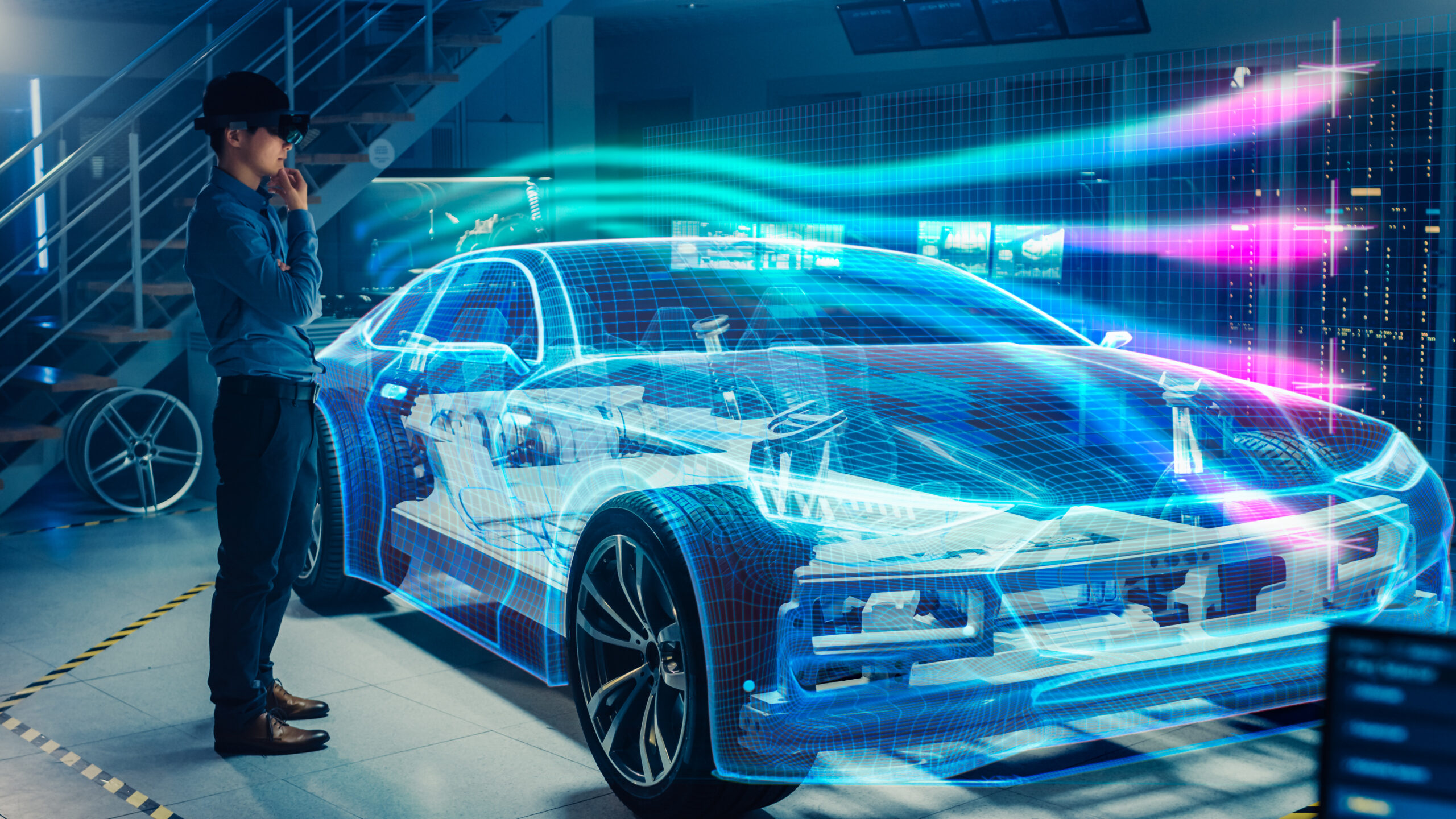
The entire automotive value chain has experienced immense pressure during the global COVID-19 pandemic. Automotive manufacturers have had to rethink how they design, verify and manufacture new vehicles. In particular, they have had to develop new ways of working while protecting the safety of their employees, families and communities.
Some of the most important steps to slowing the spread of COVID-19, such as physical distancing, have led companies to close or limit access to their offices and facilities. These restrictions, while necessary, present substantial challenges for automakers. Office buildings, factories, and testing, certification and homologation facilities either were closed or reorganized to support physical separation between employees. Vehicle design and engineering staff have had to find ways to maintain a collaborative, productive work environment while being physically separated from colleagues. Meanwhile, production facilities have undergone large-scale changes to maintain manufacturing activities while keeping operators safe.

Digitalization enables a smarter way forward
Through this transition, enterprise digitalization has proven to be critical for teams adjusting to new ways of working. Companies with pre-existing and robust digital backbones were ready and able to send their design and engineering staff home with little disruption to their work flows. These companies were also able to adapt their production facilities more quickly to accommodate for social distancing and other pandemic safety measures.
In vehicle design, automotive manufacturers have developed novel applications of virtual technologies to better support their staff, customers and partners. For instance, automakers have used VR and AR to enable virtual design reviews where the key stakeholders examine the design in a shared virtual space. The chief designers, engineers and other key stakeholders can thoroughly discuss, evaluate and make highly informed decisions on vehicle designs as if they were in the same room, even when working from home. And again, we have seen that those companies with strong digital foundations have been able to trial, refine and scale these new methodologies with greater ease, and thus realize the value more quickly.
On the manufacturing side, modern software solutions enable production engineers to virtually plan and design production stations, lines and even entire facilities before physically implementing any changes. The virtual copy of a station, line or facility, known as a digital twin, can then be simulated to verify, validate, troubleshoot and optimize production designs for safety and efficiency before any machinery is commissioned or facilities reorganized. Virtual production planning and design solutions can even simulate human operators, enabling the production design to account for ergonomics and physical distancing requirements.
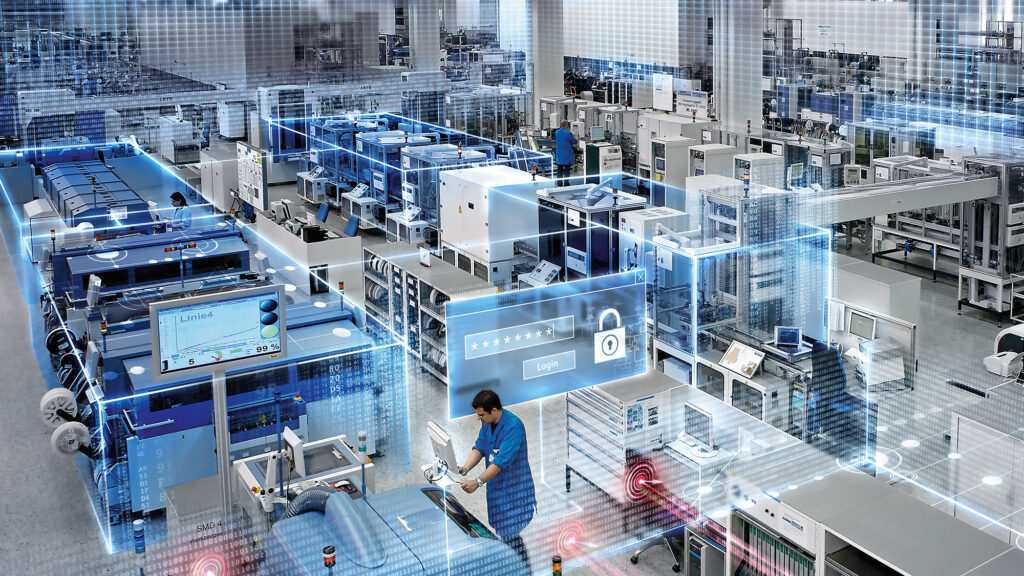
A robust digitalization strategy, however, should extend beyond vehicle and production design. Integrated solutions from product and production design through product lifecycle management (PLM), manufacturing operations management (MOM) and enterprise resource planning (ERP) create a complete digital thread from product design into the supply chain. Such a comprehensive digital thread can help companies turn complexity, whether from operating during a pandemic or from the requirements of next generation products, into competitive advantage by streamlining operations and improving collaboration throughout their supply chains.
In particular, enabling more frequent and effective collaboration throughout the supply chain will be critical as OEMs and suppliers continue to recover production output and prepare for unforeseen future disruptions. Better communication among partners also will help enable OEMs and their suppliers to coordinate the ramp-up of production capabilities with market demand to avoid both excesses and shortages of product. Collaboration also facilitates the sharing of experiences and key lessons learned while adapting to the pandemic. These experiences can help inform disaster recovery plans, allowing companies to incorporate a realistic estimation of how they will react to emergency situations.
You can hear about all of this and more in a new series of podcasts on The Future Car, from Siemens Digital Industries Software. The series covers all aspects of today’s automotive industry, and how it will continue to evolve in the future. You can listen to the first episode right at the top of this blog, or below. Stay tuned in the future to catch the rest of the series!