Expanding material choice for additive
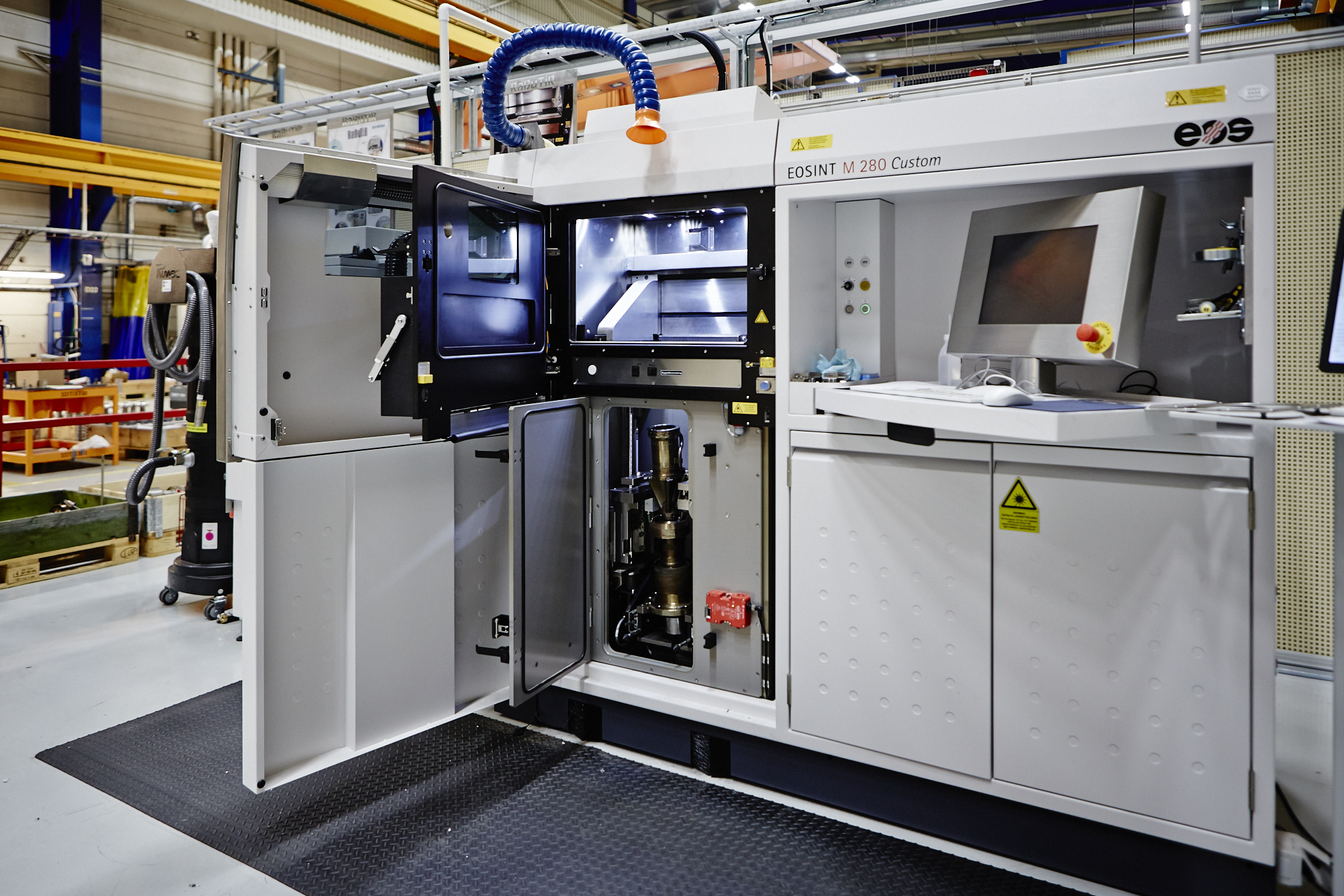
Additive manufacturing (AM) has drastically changed the world of manufacturing and design. AM is unlike any other methods for production for many reasons. The first and most obvious is that, instead of removing, deforming or binding materials together, AM deposits material – the closest analogue would be growing industrial diamonds in a laboratory. This difference contributes to AM’s unique ability to create internal structures and many of the others benefits AM has. But despite the advantages available to today, the technology is still in its infancy, especially in the way of material options.
Granted, the traditional manufacturing methods have had thousands of years to diversify the number of usable materials. Worked gold has been found as far back as the Paleolithic period; other precious metals and tin were also adopted widely near 3,000 BCE for use in jewelry, tools and weapons. These remained the options until the Iron Age, with the introduction of ferrous metals and improved techniques. The last major acceleration in metallurgy for manufacturing came from the industrial revolutions around the globe – providing faster and cheaper experimentation with automation.
AM is still very early on in this journey, but there are a few points to remember:
- Additive manufacturing is applicable to more than just metals – different processes can be used to create things of plastic, amorphous materials like cement and ceramics, composites and metals
- Additive manufacturing is being accelerated by the computational revolution – computer processing poser and sophisticated software are helping us learn about AM faster than we ever could on our own
- Additive manufacturing is built on previous achievements – while the intricacies may still escape us, the foundational knowledge used in AM is well understood and we are not learning from nothing
Also accelerating AM’s expansion and adoption is the influence of at-home hobbyists, or makers, along with traditional research institutions. Search for 3D printing on YouTube and one will find thousands of videos of makers using plastics, resins and even metals for their projects. And while many of these projects are innovative in their material selection, the cutting edge is coming from research institutions.
One such innovation has come from the combined world of academia and government research – additive manufacturing of silicon carbide. The process has quickly been picked up by universities to validate the process, but the implication for high temperature applications is huge. There is still research needed on how these printed structures interact in their most common environment – a nuclear reactor – compared to traditional ceramic production methods. It is unknown how prolonged neutron bombardment will impact the structures, but Oak Ridge National Labs has picked up the project – likely with extensive testing in their test reactors.
Regardless of the efficacy in nuclear engineering, the research on silicon carbide and the printing of ceramic materials is a great sign for the adoption of new materials for this production technique. For reference, complex amorphous structures – think optical glass – was not mastered until the seventeenth century after first encountering the creation of glass near 2500 BCE. In effect, AM combined with comprehensive software has accelerated the mastering of amorphous material production from millennia to decades.
Material selection can greatly improve a design, whether it is chosen for weight, thermal properties or even aesthetic. And while additive manufacturing is still developing its usable material list, computational power is accelerating that pool by the day. For more information on how Siemens is evolving additive technology, check out our website and check back here for some of the greatest leaps for the technology as an end-to-end solution for complex designs.
Siemens Digital Industries Software is driving transformation to enable a digital enterprise where engineering, manufacturing and electronics design meet tomorrow.
Xcelerator, the comprehensive and integrated portfolio of software and services from Siemens Digital Industries Software, helps companies of all sizes create and leverage a comprehensive digital twin that provides organizations with new insights, opportunities and levels of automation to drive innovation.
For more information on Siemens Digital Industries Software products and services, visit siemens.com/software or follow us on LinkedIn, Twitter, Facebook and Instagram.
Siemens Digital Industries Software
– Where today meets tomorrow.