Component repair with additive manufacturing
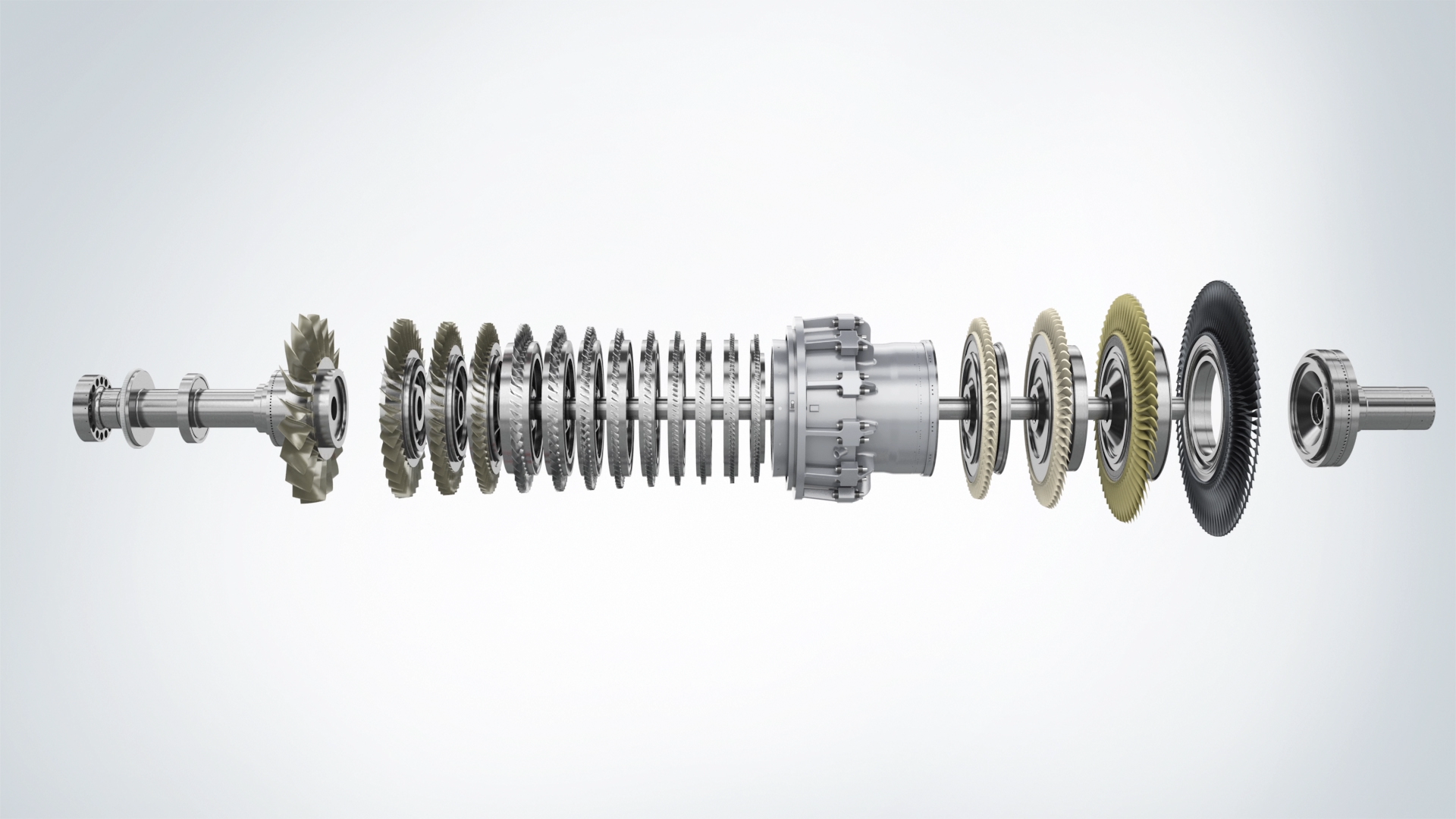
Repair, after a product or facility is created, it is one of the greatest costs of operation after labor. It makes sense, any expense that results in regained operation is an easy decision so long as it costs less than a new system. But for consumable parts, this can become a significant cost to operation. The common solution is to engineer a buffer layer that is easily replaceable – think brake pads on a car or cartridge bearings on a bicycle. This is imperfect however, since it leaves performance on the table eaten up by ease of replacement. Additive manufacturing (AM) could change this dynamic if Siemens Energy’s solution gains popularity.
The gas turbines used for energy generation run at very high temperatures with extremely tight tolerances to achieve high efficiencies. And while this is nothing special in the energy industry, the solution for repair and maintenance is a little different. When working within an abrasive environment the rule of thumb is to make the easier to replace and less expensive component wear, for a gas turbine this means the blades are taking most of the damage. Usually, this means completely replacing a blade when it becomes to damaged for proper operation, but for Siemens Energy this means rebuilding a blade better than before.
By printing the damaged area back, Siemens Energy save whatever material would have been wasted from completely replacing the component and it presents an opportunity to optimize the component for its task. To more adequately compensate for the high temperature environment inside the turbine, cooling channels can be better integrated avoiding the vicious cycle of material loss, overheating and increased material loss. By integrating long-term wear data into a digital twin of the turbine and process, each blade could be independently optimized and more systemic problems can be identified more rapidly – an example might be that at a certain rotational velocity, blade A will make contact with the turbine housing and start the material loss cycle.
With further research into printed porous materials, printed repair could become even more valuable for the tight clearances found in gas turbines and similar environments. Currently, there is work being done to create turbine blades that are purposely long with a less dense lattice structure at the very tip. The idea is to install these long blades and as the turbine spins the excess material will sluff off, eventually creating a perfect seal with the housing. Moving instead to a porous tip could increase thermal dissipation and reduce the likelihood of melting the blade tip, which would result in runaway material loss at high temperatures as before.
The complete potential of additive repair is still largely unexplored, but the benefits could be far-reaching, literally speaking. In remote construction or industrial sites, shipping replacement parts in can be an expensive and time-consuming process because for many of these activities, downtime has a direct line to lost profits. Field repair would no longer mean limping the machinery along until the replacement comes in, it would mean bringing the machine back up to complete operation in a few hours if there is a printer onsite. The infancy of AM keeps some of the more conservative industries at arm’s reach, but the wide possibilities of the technologies are of great significance to those see the benefits as outweighing the risks.
Repair could be a great jumping off point for the adoption of additive manufacturing in businesses around the world, it gets users acquainted with the workflow of AM while still delivering a tangible benefit. The efficacy and usage options will only grow from there as a business finds more ways to optimize their operation with the technology and software solutions to harness it. For more information on how Siemens Energy is implementing additive manufacturing for repair, Metal AM has a great article on the topic.
Siemens Digital Industries Software is driving transformation to enable a digital enterprise where engineering, manufacturing and electronics design meet tomorrow.
Xcelerator, the comprehensive and integrated portfolio of software and services from Siemens Digital Industries Software, helps companies of all sizes create and leverage a comprehensive digital twin that provides organizations with new insights, opportunities and levels of automation to drive innovation.
For more information on Siemens Digital Industries Software products and services, visit siemens.com/software or follow us on LinkedIn, Twitter, Facebook and Instagram.
Siemens Digital Industries Software – Where today meets tomorrow