Leverage new technologies to optimize machine shop operations – eBook
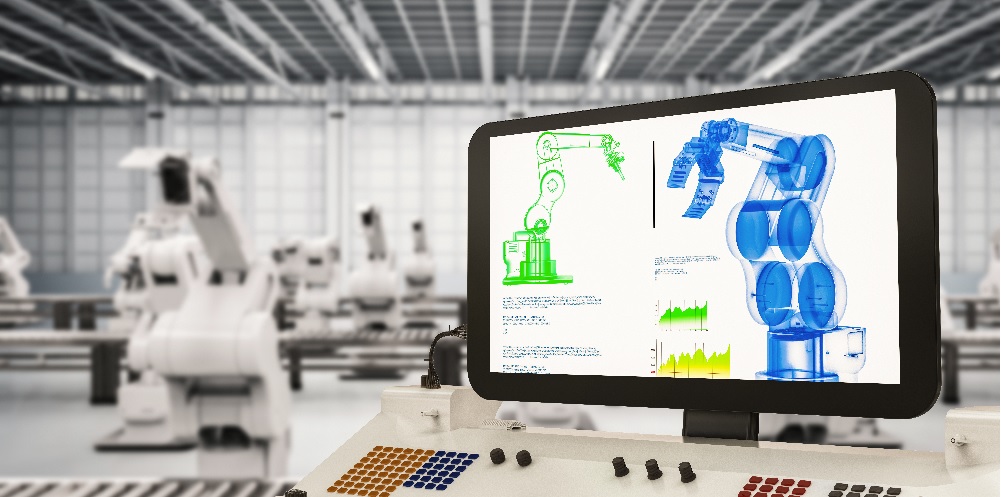
It’s not an easy task to run a machine shop in today’s economic landscape. Global competition is intense, and customers are demanding the highest quality with tight delivery schedules.
Though manufacturing opportunities are readily available, it takes highly skilled organizations to profit from them. Additionally, there are many technical challenges, including high friction model processing, toolpath creation difficulties, unreliable G-code verification and low reuse levels of machining knowledge. However, the modern, digitalized machine shop can address these hurdles.
Innovative technologies like Digital Part Production help to qualify the digital journey for machinists to seamlessly prepare and manipulate CAD application models, developing top-quality automated toolpaths, thus simulating the execution resulting in G-code that standardizes the NC knowledge to reuse across the entire process.
Download our eBook.
This eBook’s focus is on the following issues:
- Publishing and contextualizing the NC Machining study findings.
- Introducing a network of technologies that address modern machine shop needs.
- Proposing practical recommendations for the next steps.
There are many challenges in running a machine shop. Using the right technologies makes it easier and more powerful. It’s expensive for machine shops to address tool breakage and turnaround times. When unexpected tool breakage occurs, the result is a significant delay in time-to-delivery. Also, unexpected tool wear requires machine shops to resort to manual post-machine quality work, creating further delays. Therefore, it is crucial to lowering machine times, as they directly relate to time-to-delivery and can affect the machining work, depending on the type of work and the overall process.
Customer acceptance rate
Also, customer acceptance rates, though not time-oriented, are fiscally related. Parts must pass quality measures or return to the machine shop. To meet customer requirements, they need reconditioning, causing delays in time-to-delivery – otherwise, they’re scrapped. These thrown away parts must be machined using new raw materials, which increases cost without a corresponding rise in revenue. Therefore, some contracts have financial penalties for exceeding certain return thresholds. So, increasing customer acceptance rates contains many fiscal implications.
Time wasting issues
The objective of a machine shop is to improve operations and increase revenue without over impacting costs, thus making a significant profit. In a 2016 NC Machining Research Study, surveying 215 respondents to assess the strategies and tactics employed in modern machine shops, the explicit focus is on business objectives, standard practices and technologies deployed. So, no one challenge or goal supersedes another, with none exceeding 30 percent. However, there were some common themes among the disparate issues: friction in model import, prep and change. For example, in designing a part, various problems can affect time-to-delivery related to friction and inefficiency both physically and digitally:
- Transferring data between different software (CAD, CAM, CMM) and teams
- Working with demanding customer’s designs and tooling models
- Accommodating internal or external design changes from stakeholders Importing models and gaining solid geometries.
Also, there are changing geometries while preparing toolpath creation, brought on by a model being imported and stripped of its features and parameters, leaving a solid geometry without controls. It’s a time-consuming process to modify these models. Furthermore, after a model release, over half of machine shops rely on standalone CAD/CAM systems, requiring them to repeat the design process, starting with re-importing the model, fixing it and then re-preparing it for machining.
Innovative technologies
The manufacturing landscape is quickly evolving with sophisticated technologies coming to the forefront. 3D printing production is one of these innovations, allowing for opportunities to reduce time-to-delivery. Additive manufacturing, or 3D printing, foresees printing production parts in hours versus merely cutting metal for a day. Amazingly, 37 percent of respondents are experimenting with 3D printing. And, another technology is robotics, where 24 percent of respondents are using it for machine tending and CNC machining. Robotics are performing operations like trimming, polishing and deburring. These traditional and progressive robotic applications in machining increase automation, provide consistent quality, enable more significant machining parts in a single setup and extend operating hours.
Achieving the time-to-delivery goal equates to an increase in revenue. However, it’s not an easy task. There are many hurdles to attaining this objective, including friction in model import, prep and change workflow, making it challenging to prepare a model for toolpaths and accepting the design changes later in the process. Other notable hurdles require innovative technologies to produce higher quality and flexibility using IoT technologies to see a marked improvement.
Machine shop production is a significant challenge, but providing the correct technologies makes it possible and profitable.
Software solutions
Siemens Digital Industries Software drives the transformation to enable a digital enterprise where engineering, manufacturing, and electronics design meet tomorrow with the Xcelerator™ portfolio.
Xcelerator is a comprehensive, integrated portfolio of software, services and an application development platform, accelerating businesses’ transformation into digital enterprises. It unlocks a powerful industrial network effect – essential requirements to leverage complexity as a competitive advantage, no matter the industry or company, to seamlessly create tomorrow’s complex machines.
Related links:
Listen to DPP Podcast01 – an introduction to Digital Part Production
Listen to DPP Podcast02 – highly automated CAM
Listen to DPP Podcast03 – synchronized part production
Listen to DPP Podcast04 – benefits of additive manufacturing