Complex machine validations – multiphysics simulation
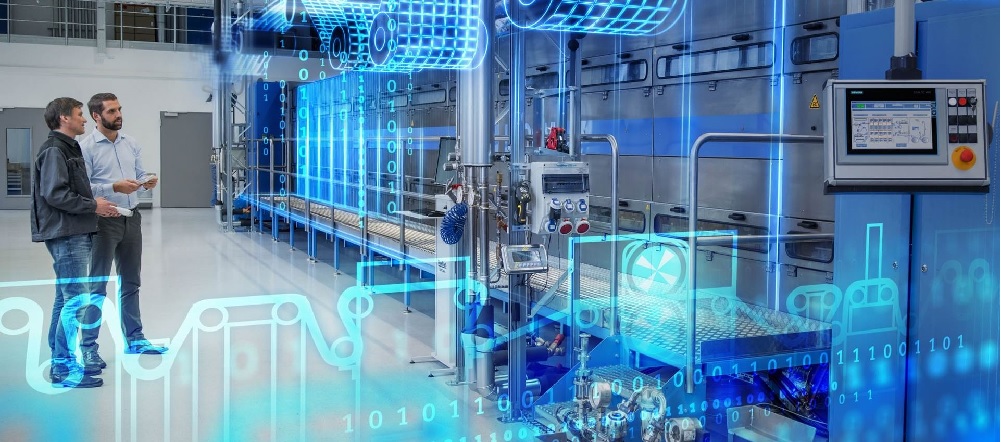
In a recent article in Plant Engineering, Rahul Garg, Vice President for Industrial Machinery & SMB Program Digital transformation at Siemens Digital Industries Software discusses how factories and manufacturers globally are looking to digital transformation and innovation to meet customer demands by adopting new technologies. There is a demand for intelligent, flexible, configurable and automated industrial machinery equipment. Therefore, industrial machinery companies must establish new design practices to keep up with complex machines.
>Read the article.
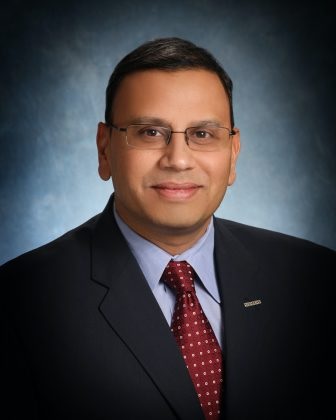
An Intelligent Performance Engineering solution helps to improve simulation, design and connectivity for machine builders. By applying a multi-physics simulation, it balances multi-attribute engineering to deliver a wide range of physics and disciplines.
Multi-physics simulation customizes complex products
Products are now lighter, smaller and customized to meet consumer demands. Multiphysics simulations enable the machine builders to virtually explore the physical interactions of complex products. It tracks interactive data of product performance, safety and longevity. Also, it measures the interactions of fluid force performance, thermal effects, structural integrity and electromagnetic radiation. Optimum consideration is given to all loads simultaneously during real usage simulation. Digital transformation addresses changing customer demands and adopting new technologies – a global concern.
Simulation improves design choices and provides benefits
It is essential to validate the performance of new equipment or modified designs before a machine reaches the customer. It is best to fix problems in the design phase versus product development. “Adopting digital simulation and analysis tools allows original equipment manufacturers (OEMs) to understand how design choices affect a component, device or machine’s performance and failures,” says Rahul Garg. Manufacturers are delivering machines with faster cycle rates and compressed delivery schedules; therefore, teams are motivated to accomplish advanced simulation upfront.
Intelligent Performance Engineering and multi-physics simulation reduces the need for testing and physical prototyping, improving the speed for delivering a final design. “As higher fidelity modeling integrates into design organization, it improves collaboration between experts, permitting each to view their domain cohesively,” added Rahul. Therefore, a machine simulation works across all the environments’ worth considering, with multi-physics uniting experts that attend to end-customer needs while addressing any unexpected discoveries.
Multi-physics simulation – Picanol case study
Picanol, a global leader in textile manufacturing machines, produces optimum weaving machines for the fabrics worn and used daily. They develop highly complex machines that address many needs for fabrics, cotton, silk, jute bags, fiberglass material draperies, upholsteries and car seats. Changing end customer needs require machines to be compliant with performance and speed requests. Therefore, maintaining the entire weaving machine’s structural integrity, vibration and thermal concentrations is essential.
An optimum multi-physics simulation approach analyzes issues separately and sends those results as input for future simulation. Multiphysics simulation provides the ability to determine the best methods to address the challenges of speed, thermal and vibration needs, using innovative tools and capabilities.
Simulation and testing
Properly validating a design require both simulating and testing. “You perform the simulation for testing, and the results provide a helpful indication for knowing the physical sensor placements,” says Rahul. You can apply the physical measurement data to the digital twin to validate it, associating the results from reality to a numerical model.
Virtual sensor results are attained from the simulation model, merging the real measurement results to be in sync with the physical measurement and simulation.
“This holistic approach of simulation and testing provides a competitive advantage for machine builders through a comprehensive top-class suite of validation,” states Rahul.
Read Rahul Garg’s article to learn more.
Simulation software solutions
Siemens Digital Industries Software is driving transformation to enable a digital enterprise where engineering, manufacturing and electronics design meet tomorrow. The Xcelerator portfolio helps companies of all sizes create and leverage digital twins that provide organizations with new insights, opportunities and levels of automation to drive innovation.
For more information on Siemens Digital Industries Software products and services, visit siemens.com/software or follow us on LinkedIn, Twitter, Facebook and Instagram.
Siemens Digital Industries Software – where today meets tomorrow.
Related links
Listen to the IPE Podcast on leveraging machine complexity.
Learn more about Intelligent Performance Engineering.
Rahul Garg is the Vice President for Industrial Machinery & SMB Program, responsible for defining and delivering key strategic initiatives and solutions and global business development. He and his team are responsible for identifying key initiatives and developing solutions for the industry while working closely with industry leading customers and providing thought leadership on new and emerging issues faced by the machinery industry. Rahul’s experience and insight are derived from 25 year career delivering software-based solutions for product engineering and manufacturing innovation for the global manufacturing industry, spanning a career in R&D to program management, sales and P&L management and having focused exclusively on the industrial machinery and heavy equipment industry since 2007.