Continuous validation for aerospace development
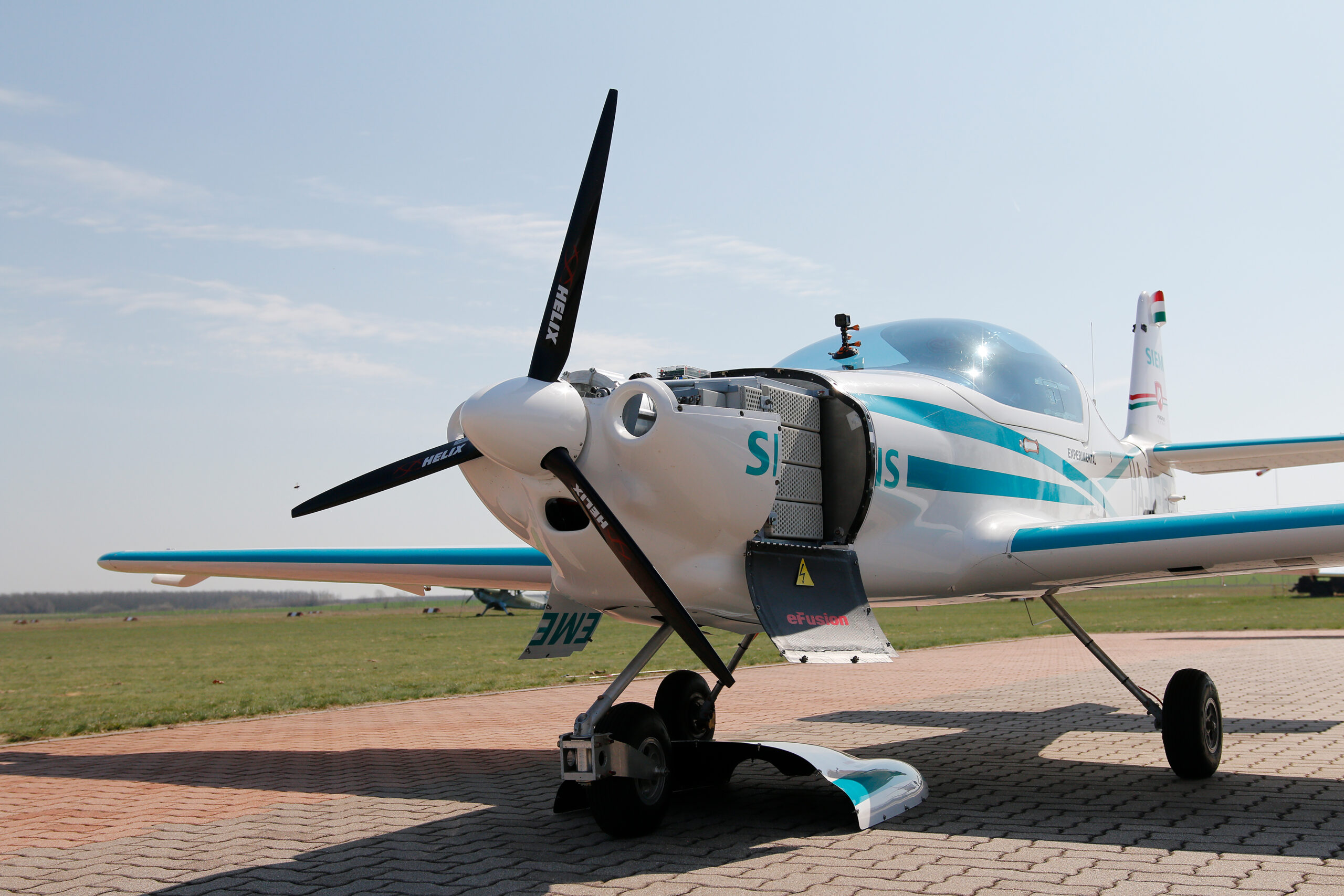
The complexity of an aircraft’s architecture is not solely in it millions of lines of software, nor the orchestration of mechanical systems giving humans flight, but the interconnectivity of these systems with everything else inside the craft. Design for many industries, including aerospace, has been dominated by the same process – make a plan, design each system in it’s respective department, integrate until you find a problem, re-design and repeat until the product meets the requirements set out in the beginning of the process. For less complex products this can result in reasonable delivery times and development costs, but as the number of interconnected systems grows so too does the possibility of expensive delays and reworks. Fortunately this is not an inevitable endeavor, the right methodology and tools can improve multi-disciplinary integrations – the continuous validation in the model-based systems engineering (MBSE) workflow is one such tactic.
Simultaneous design
Interdisciplinary designs rely on multiple engineering teams to work simultaneously on different systems of the product. For a modern commercial airliner those teams are likely to encompass four main categories – mechanical engineering, electrical engineering, electronics design and software development. But none of these groups can work without context of the the others. To understand that requirement, we’ll examine a simplified wing design.
Mechanical engineers will be tasked with the structures of the wing, which would include the supports, control surfaces, mounting positions for motors or other components as well as the composition of the wing surface. Electrical engineers would be working on the wiring harnesses, that are increasingly growing as electrical control systems replace mechanical ones. And there might be some intervention by electronics and software groups to control some of the systems within the wing. Without understanding between departments, the mechanical engineers could present a wing design the does not account for how the wire harness will be routed through the wing to reach the control systems or even the engine if it is an electrified aircraft. This is a very common hurdle to the integration process, a wing design may have passthroughs for the wire harness, but they did not account for the increased size of the connector compared to the wire bundle.
Earlier problems are easier problems
Continuous validation does not prevent errors all together, but it catches users when they make decisions that impact other systems. This prevents teams from committing changes to the design and not realizing the problems with it until late stages of development where alterations are even more costly in time and capital. Should the electronics team switch to a new aileron controller, it is important to to understand how that impacts the cabling needed by the electrical engineering team as well as how that changes the role of software for initiating a control surface motion.
The process is not strictly about discrete changes either, an important aspect of continuous validation is simulating the complete system of systems. Not all changes that impact other systems result in a complete failure, often it can be at the cost of reduced performance or some other metric. Balancing the performance or viability of each change manually would make this entire process unproductive, instead simulation is leveraged to understand the best mixture to reach the design requirements of the product. An electric aircraft, for instance, requires heavy batteries to store energy for propulsion. Adding or removing batteries does not have a linear impact on the range, as the total weight of a craft drops the energy required to more the craft does as well resulting in more miles of flight per battery. The inverse is also true, as adding batteries has diminishing returns on the range of the craft.
Validate the validation
All of this planning, coordination and balancing of design is only as good as the simulation models be implemented. While a purely digital evaluation of aircraft worthiness is an intriguing prospect, that is just not feasible. The models used for simulation need to be validated against real-world conditions to ensure their accuracy. In terms of the digital twin, it is closing the loop on the virtual aircraft. Enabling this in practice requires meticulous traceability of every process, design change and test to know why a decision was made, how it impacts the greater system and whether it was the optimal choice for the product. MBSE provides a framework for this kind of thinking, it is not a product or a tool in the formal sense, but it provides companies insight into their products well before the design is finalized.
For a more in-depth look at how mechanical systems, electrical ones and software intertwine within aerospace development projects, there is a great article on the topic from CAD&Ritnytt magazine out of Sweden by Dale Tutt. It examines how structural design is still a very important part of aerospace design, even with the continued emphasis on software and electronics – because even if planes are becoming flying computers, they still need wings and mechanical systems to fly.
Siemens Digital Industries Software is driving transformation to enable a digital enterprise where engineering, manufacturing and electronics design meet tomorrow.
Xcelerator, the comprehensive and integrated portfolio of software and services from Siemens Digital Industries Software, helps companies of all sizes create and leverage a comprehensive digital twin that provides organizations with new insights, opportunities and levels of automation to drive innovation.
For more information on Siemens Digital Industries Software products and services, visit siemens.com/software or follow us on LinkedIn, Twitter, Facebook and Instagram.
Siemens Digital Industries Software – Where today meets tomorrow