IIoT – A story of options and how to balance them – IoT miniseries ep. 3
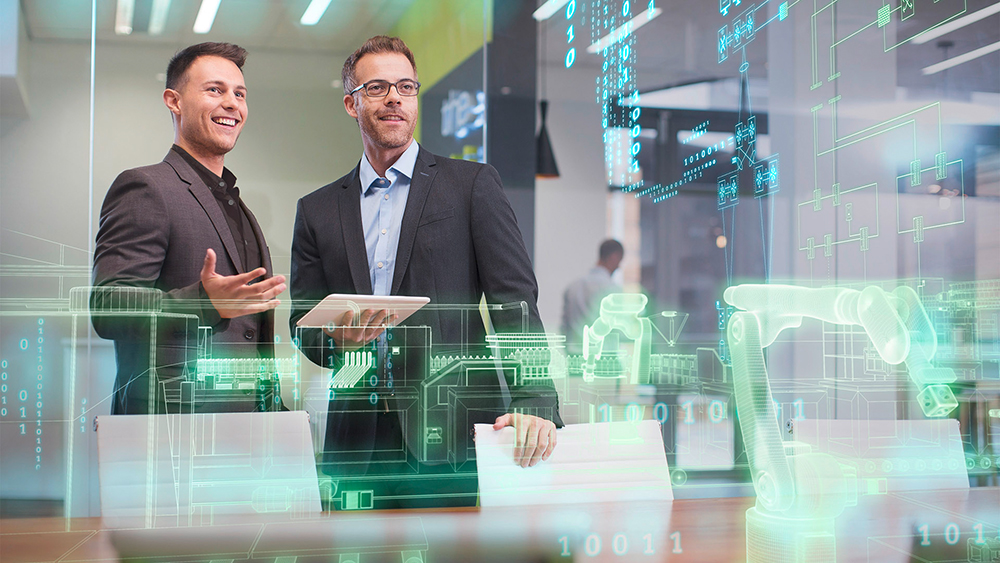
The industrial machinery sector has never stopped evolving. Many of the major leaps came in the industrial revolutions, but between each of these time periods the innovative continue their work creating the framework for the next revolution. Often descried as one of these revolutionary technologies, the industrial internet of things (IIoT) is full of possible applications in the field. But finding the best application can be difficult when there are so many disparate paths to success.
In episode three of the podcast miniseries – Future-proof with the IoT – the guests cover many of the decisions that need to be evaluated and understood when implementing the internet of thing (IoT) in an industrial environment. Often the most daunting of these decisions is where to start, there are many valuable processes that the IoT enables, but not all make sense for new installations. Another common point of discussion is whether to use an edge-based infrastructure or a cloud-based one, both have their benefits and understanding how they align with your implementation goal is essential in deciding which to implement.
Where to start
The decision of what to implement first in regard to IoT can be a paralyzing one for some customers. Many believe that their solutions should be large and complicated, able to capture everything that happens in a facility. But that neglects the learning and experience needed to be able to implement any of it successfully. If you are hiring a third party to install, calibrate and manage it all, it is doable but expensive. For a company looking for a more in-house solution it is best to start simple and learn from mistakes, then shift to more complex data flows not just as experience grows but as the need reveals itself.
A common first step, and a highly recommended one, is to enable condition monitoring. It is a fairly simple process compared to some of the flashier implementations of IoT, but it is a foundational process for many of the higher level optimizations and automations capable within an IoT system. Condition monitoring is also likely a capability readily available to machines made in the last few years, meaning there will be less up-front investment while learning how to use the IoT. Whether condition monitoring is your companies first step or not, it would be prudent to understand that even small implementations can create massive improvements while reducing the possibility of a failed project wasting time and investment.
How to build it
Centralized versus distributed networks is a decades long conundrum, but the answer is no more definitive today than it was in the beginning. The only architectural changes have been to the breadth of functionality to each choice. In today’s vocabulary the struggle is between edge devices and cloud infrastructure. Some applications requiring high data privacy may be wary of cloud breaches and others requiring manipulation of huge data sets may balk at the cost of a in-house compute infrastructure. And as with most things in life the optimal choice between edge and cloud is likely somewhere in-between.
Edge can provide ultra-low latency solutions, which are critical to machines using that data in real time. But when you want to look at the data at a facility level it is far more efficient to spin up compute power on a cloud service than it would be to use your own centralized computer network. The options to connect these two technologies are near limitless, but finding the right solution is the hard part.
For a full discussion of where to start your adoption of IoT practices, whether the infrastructure should be localized or in the cloud, as well as other topics on the implementation balance that is IoT make sure to listen to the complete third episode. If you’re not quite ready to tackle these questions, it might be wise to start with episodes one and two to understand how the IoT is meeting the common struggles of industrial machinery.
Siemens Digital Industries Software is driving transformation to enable a digital enterprise where engineering, manufacturing and electronics design meet tomorrow.
Xcelerator, the comprehensive and integrated portfolio of software and services from Siemens Digital Industries Software, helps companies of all sizes create and leverage a comprehensive digital twin that provides organizations with new insights, opportunities and levels of automation to drive innovation.
For more information on Siemens Digital Industries Software products and services, visit siemens.com/software or follow us on LinkedIn, Twitter, Facebook and Instagram.
Siemens Digital Industries Software – Where today meets tomorrow
Jörg Ludwig – Since 2018, Jörg has been in the sales enablement team for MindSphere and since October 2020 also for Mendix, globally responsible for the creation of learning paths, enablement sessions, and value selling trainings and workshops. Prior to Siemens, Jörg ran his own business as a Value Selling trainer and coach for more than 7 years. He gained Sales experience and expertise from over 16 years in global Software Sales organizations.
Heiko Dickas – Heiko is the Team Leader of the digitalization team since the beginning of 2017 in the Bad Neustadt motor factory. His scope is being an enabler for the production unit in terms of digitalization. Heiko has been with Siemens for more than 30 years in different functions.
Colm Gavin – With over 20 years of experience in the Siemens Digital Factory, Colm works on business development for digitalization topics as they pertain to Siemens SW and Factory Automation, specifically virtual commissioning, Industrial IoT, Industrial Edge and AI topics.
Matthias Lutz – Matthias joined Siemens 14 years ago, starting in supply chain and procurement department. In 2015, he moved to the industrial customer service organization, focusing on industrial IoT and digital services.
Sebastian Oeder – Sebastian is Head of the production unit main motors in the Bad Neustadt motor factory. He has a background as a production manager at Siemens Energy and as a consultant at Siemens Corporate Technology.