Leveraging MES solutions beyond production
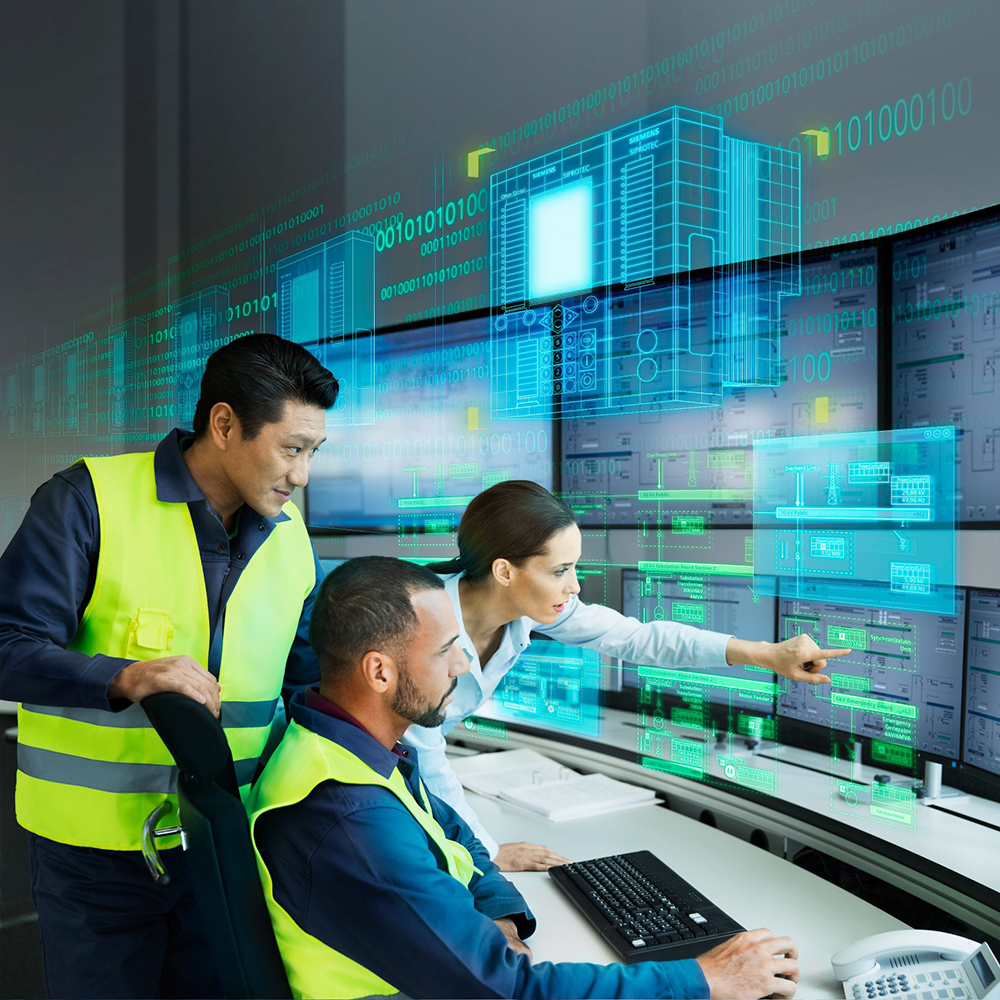
Expand your imagination in what you can do with simulation, primarily as related to your manufacturing execution system: how much could you improve your product output?
The typical process is early planning, simulation and production, after which, simulation is forgotten. However, there is still value in simulation which companies are leaving on the table; they view it as only being applicable in the design and engineering phase, as opposed to it also offering production value. The ability to forecast potentially avoidable mistakes that otherwise would be found and addressed later in production can help you solidify a position in the marketplace and improve your processes and products.
At PLM World 2018 in Germany, a booth displayed the concept of a time machine which integrates your manufacturing execution system (MES) with simulation. It took real execution data and inputted that information into the simulation. The virtual world was leveraged to solve real-world production issues and evaluate what-if scenarios to improve manufacturing quality and efficiency – all before it physically went into production.
These scenarios could include evaluating resource changes (both human and machine), assembly process changes, material logistics changes, analyzing defects and addressing shop floor issues. The value of these evaluations serves to improve your product output via simulation results.
Simulation beyond design
Manufacturing simulation tools provide companies with the ability to fully virtualize their manufacturing process. This comprehensive approach improves product quality and reduces time to market for new products. However, when you move from the virtual world to real-world execution, simulation is typically not part of that process.
However, conventional simulation does not bring you to 100 percent completion. There is a remaining, crucial element of real-world issues which involves collecting data while the product is built and recoding defects, which are not being captured in the virtual world.
When you address these issues, you bring that data back for full analysis to help you fix the problems. Elements of human behavior are captured ‒ actual operation times for analysis against planned build times from simulation.
MES solutions – value and challenges
Manufacturers are not benefitting from the higher value which can be retrieved from the simulation environment. There are advantages to using the automated interaction of virtual and real data as opposed to conventional, manual interventions.
Though simulation is not typically a tool used to help solve product issues like product defects, overruns, material logistics and production line layout, the digital thread is inherently required as this is happening late in the process. Data must be mature and maintained from design through production. If an issue is evaluated in simulation it could involve design engineering, production engineering or a collaboration of both.
Additionally, it would help if you collaborate with areas of the digital thread, working in concert with simulation. For example, a design needs to produce quality models for the simulation environment, while manufacturing engineering needs to build quality reusable simulations. In turn, production can leverage the simulation of both of these by providing the necessary feedback such as non-conformance, shop floor issues and product assemblies to enrich the product lifecycle.
The final benefit
A simulation environment can assist you as you step you through the MES, becoming a training tool or aid for shop floor operators. Simulation with MES solutions can bring you one step closer to what you might encounter in the real world, thus making it the ideal realm for solving potential problems before you physically begin producing your product – saving you time, money and improving the overall product.
Click here to learn more about MES.
About the author
Louis Hughes is a presales consultant and solution architect for Siemens PLM Software. He works closely with the aerospace and defense, heavy equipment, automotive, and electronic industries in the U.S. and abroad. Louis has been working in the PLM and manufacturing space and helping customer connect the digital thread between PLM, ERP, and MES for more than 12 years.