Visionary manufacturers are rethinking enterprise architecture
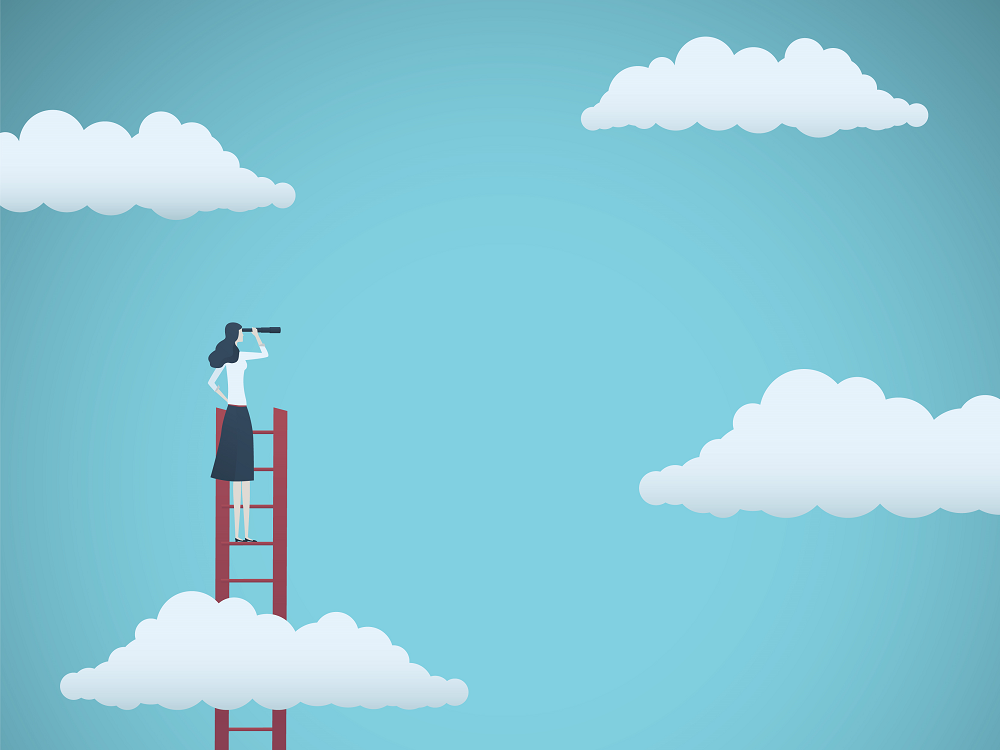
By: Alex Allison and Josh Ray
Digitalization has caused a groundswell of ongoing change. Emerging technologies push one another forward, helping businesses create new business models and new value-adding opportunities. Leading business thinkers know that the digitalization of internal processes is one of the greatest areas of opportunity for businesses.
Nowhere is this more obvious than in manufacturing, as next-generation smart products and processes wirelessly integrate data and consolidate control at limitless scale. In most cases, traditional manufacturing technology is obsolete simply because most older machines, hardware and software were not designed for the massive amounts of data and Internet of Things (IoT) networking that are required for competitive operations these days.
In fact, PWC says that out of 2,000 manufacturers, 86 percent expect to see cost reductions and revenue gains from digitalization over the next five years.
Conversely, manufacturers that don’t embrace digitalization fast enough risk being left behind. In a survey of more than 500 C-suite executives across Europe and the U.S., two-thirds said they believe that 40 percent of Fortune 500 companies will no longer exist in 10 years due to digital disruption. Over half (53 percent) said they were concerned about competition from disruptive businesses.
Still, for many on the path to digitalization, there’s a bump in the road: Enterprise Systems Architecture (ESA). ESA, or a company’s overall IT systems and architecture, supports traditional manufacturing processes and is built on core applications such as enterprise resource planning (ERP), manufacturing execution system (MES), product-lifecycle management (PLM) and customer-relationship management (CRM).
ESAs have traditionally been siloed by function, location, file systems and other boundaries. Many manufacturers still rely on legacy infrastructure that can’t integrate with connected devices, applications or modern security protocols—all important building blocks of a digital enterprise.
To survive disruption and unlock better performance, visionary manufacturing leaders are looking to connect the data and workflows contained in these silos and integrate new advanced capabilities into their core systems. This requires a reexamination of ESA, including individual systems and their contextual relationship within the organization.
Trends behind the ESA disruption
What are ESAs biggest pressure points?
Emerging technologies. To start, emerging technologies, which include the IoT, cloud services, predictive analytics, machine learning and automation, give manufacturers access to data (analytics, documents, orders, invoices, etc.) on a scale that never existed before, providing better insight and control. For example, research by the MPI Group found that 69 percent of manufacturers credit their use of IoT technologies for increasing profitability by streamlining processes in document management, warehousing, logistics and packaging.
That’s good news for manufacturers but potentially bad news for their ESAs. Legacy ESAs lack the capabilities to handle the vast amounts of data that emerging technologies generate, use and process. This hampers modern competitive needs for agile operations, fast customer response and intuitive user experience.
Smart manufacturing. Another trend weighing heavily on ESAs is smart manufacturing. Smart manufacturing aims to integrate intelligence into machines, parts, materials, products, buildings and supply chains to create a connected, open, end-to-end process and infrastructure. It’s the force behind “lights-out factories” that are entirely automated; industrial systems (like fluid or temperature controls) that learn how to adjust themselves when needed; and entirely new products and processes such as intelligent engine components produced digitally via additive manufacturing.
Pioneering companies are uncovering valuable information by integrating machines, computers and data that have traditionally operated separately. The true end-to-end systems integration enables manufacturers to establish virtual operations, monitor the shop floor, and optimize operations within the factory and along the supply chain.
For example, Siemens used smart-manufacturing principles to standardize labeling across its global factories to drive new levels of efficiency. The label management system was integrated with PLM, MES and ERP systems and deployed on a private Siemens Cloud. The system enables the use of universal label templates that can be printed with data from any of the business systems. This flexibility enables factories to maintain fewer template variations, process fewer change requests and enjoy improved label consistency and compliance.
Integration with Siemens’s other business systems has also enhanced productivity. Label printing has been reduced from eight seconds to 300 milliseconds, automation has eliminated the need for multiple printers and the company’s Service Delivery group has improved its implementation speed.
Data is the new oil
Today, data is what prompts action—not systems. Harnessing information from countless data streams and converting it to business insight drives more efficient decision-making, better planning and a safer, more automated environment for workers through the use of remote control, intelligent processes, digital twins, augmented reality and other abstractions of physical production and products.
Industrial manufacturers ready to shape the future of their organizations and create a foundation for digital business must ensure their ESA is up to modern standards. This will help protect transformation budgets from wasteful IT spending, support technology decisions from a holistic, enterprise point of view, attract and retain key talent, and bring differentiating products and services to market faster.
This concludes part one of our series on enterprise system architecture. In part two, we discuss how to create a future-ready framework in your enterprise’s architecture.
About the authors
Alex Allison is an account orchestrator with Siemens PLM Software and has been with the company since 2013. In his current role, he is responsible for maintaining relationships with electronics and high-tech companies on the Eastern seaboard. Alex began his career in the semiconductor industry, specializing in manufacturing systems. He has experience around OCM, managing complex enterprise system architecture, and ensuring customers have the right solutions and processes that will result in transformational efficiencies throughout their business.
Josh Ray is an account development executive for Siemens PLM Software. He began his career in the manufacturing software organization. Josh is passionate about people and technology, and his current role is to support business development in the industrial machinery and medical device industries. Josh works with companies to increase awareness and adoption of technologies across their innovation and product lifecycle. He regularly engages with C-level executives in this role, which inspires his drive to gain a deeper understanding of industry trends and the obstacles companies currently face.