Smarter manufacturing with 3D printing and a digital twin
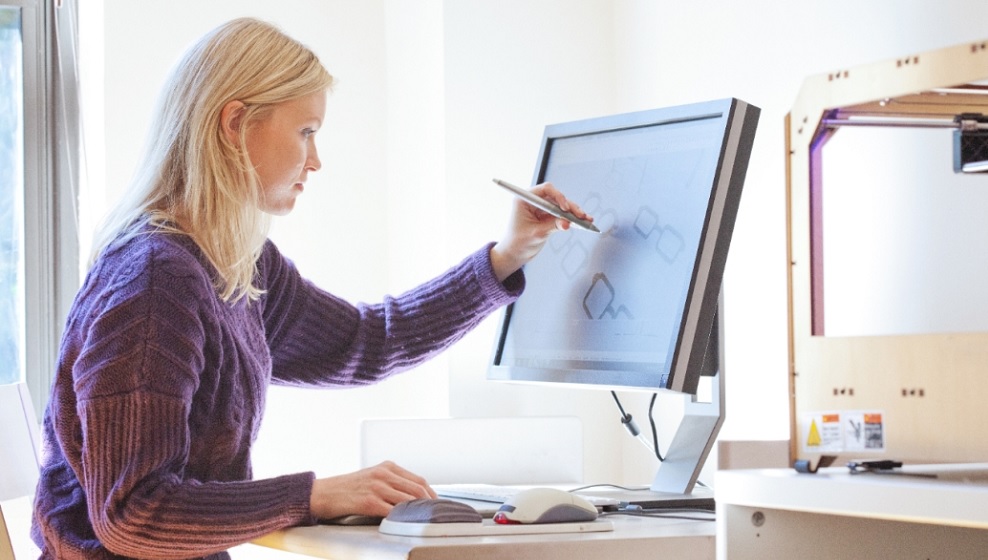
Additive manufacturing (AM) is becoming mainstream with compelling benefits —faster and more flexible than conventional manufacturing approaches. Also, it executes fewer constraints on product design, supporting the design freedom that comes from not integrating or considering manufacturing methods like welding, sheet metal and casting. This process allows engineers to focus on the minimum material needed for the design. It also provides the ability to consolidate multiple separate parts to create a single additive component, thus eliminating the cost of precision machining individual parts.
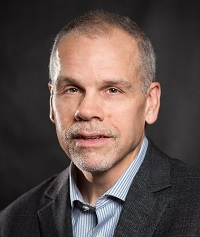
In an Industrial Machinery Digest article, Bill Davis, Director of Industrial Machinery and Heavy Equipment Solutions at Siemens Digital Industries Software, discusses how additive manufacturing, or 3D printing, provides multiple manufacturing benefits. These include faster, flexible manufacturing methods with fewer design constraints that allow the design freedom to integrate welding, sheet metal and casting.
>Read the article to learn more.
Engineers can now design with the minimum materials necessary, using additive manufacturing to combine separate parts as a single additive component, eliminating the cost of machining each part.
However, there are challenges in manufacturing and delivering high-quality AM parts at an industrial scale. There is a need for a tightly integrated and closed-loop design—simulate—manufacture flow to achieve quality additive products while minimizing design iterations.
Before printing, designs must endure rigorous simulations of the printing process to mitigate risks, optimize the printing and improve yield. This method expands the full breadth of variables affecting the additive outcome, including the mixture of virgin and recycled print material, ambient humidity, machine parameters and more. Also, most companies must fit AM machinery into existing facilities, integrating it with traditional manufacturing processes.
Implementing a comprehensive digital twin is essential to this process, including the initial simulation design, production and testing, to return additive manufacturing positively.
The digital twin is vital to construct and execute additive parts while managing delivery, manufacturing, operations and quality of manufacturing operations management. In addition, these components deliver awareness for harmonizing activities to provide accurate parts.
Siemens Digital Industries Software is driving transformation to enable a digital enterprise where engineering, manufacturing and electronics design meet tomorrow. The Xcelerator portfolio helps companies of all sizes create and leverage digital twins that provide organizations with new insights, opportunities and levels of automation to drive innovation.
For more information on Siemens Digital Industries Software products and services, visit www.sw.siemens.com or follow us on LinkedIn, Twitter, Facebook and Instagram.
Siemens Digital Industries Software – Where today meets tomorrow.
Related links:
Listen to the Smart Manufacturing podcast on this topic.
About our experts:
Bill Davis is Solution Director of Industrial Machinery and Heavy Equipment Industry for Siemens Digital Industries Software. His experience and insights have been acquired from a career spanning 30 years in engineering and operations management with machinery and heavy equipment companies. Bill holds a master’s degree in Business Administration from Marquette University, with a concentration in Operations Management and Strategic Marketing, as well as a Bachelor of Science degree in Mechanical Engineering from Milwaukee School of Engineering.
Rahul Garg is the Vice President for Industrial Machinery & SMB Program, responsible for defining and delivering key strategic initiatives and solutions and global business development. He and his team are responsible for identifying key initiatives and developing solutions for the industry while working closely with industry leading customers and providing thought leadership on new and emerging issues faced by the machinery industry. Rahul’s experience and insight are derived from 25 year career delivering software-based solutions for product engineering and manufacturing innovation for the global manufacturing industry, spanning a career in R&D to program management, sales and P&L management and having focused exclusively on the industrial machinery and heavy equipment industry since 2007.