Starting a 3D printing program
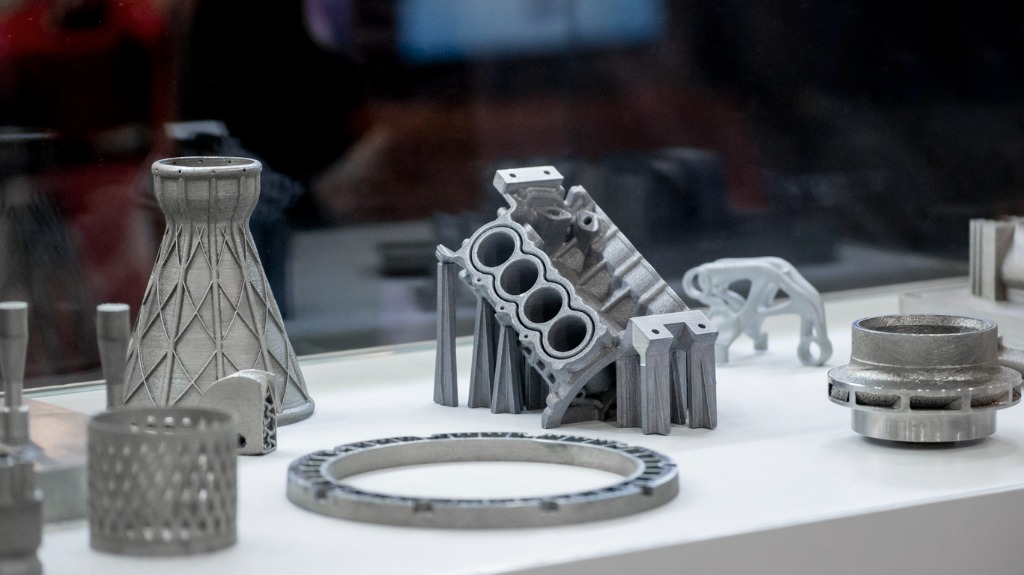
Starting any new manufacturing program requires planning, organization, and time. 3D printing is no different, but the common characterization of it being a silver bullet is more of a detriment to adoption than an incentive. Partially because it is untrue, just like every manufacturing process additive manufacturing (AM) has use case where it is best implemented, but the more important effect for today’s discussion is that seeing 3D printing as a silver bullet presents it as a monolithic endeavor. To help mitigate this perception one of Siemens Software’s AM experts – Ashley Eckhoff – authored a plan for manufacturers to gain confidence with AM at their own pace. His tips follow three distinct steps to adoption.
Low-pressure experience
Knowledge is arguably the most important part of a manufacturing process, for CNC you need to know what bit speed is needed for a specific metal or even finish, you need to know how quickly molten metal can be poured into a mold to prevent material distortion and for AM you need to know things like laser beam intensity or a variety of other variables. Gaining this experience is invaluable to quality manufacturing, but to prevent the mistakes that are bound to occur from impacting the greater business, it can be very wise to start with small projects. Even the creation of secondary products used in production rather than as the product can be a great entry point. And with this trial run you will need multiple groups working together – the designers, analysts, product engineers and managers – so that they can distribute their experiences to the wider organization as AM is adopted.
Experiment to innovate
A large portion of 3D printing’s value proposition is to create something that is one of a kind, faster than any traditional manufacturing technique. If everything made with 3D printing is similar, the long-term solution would be to invest in something more skewed towards mass-production, like injection molding or casting. Creative design with AM adds greater value to the business through new solutions to problems, but it also expands the experience-base of the users. It pushes engineers, designers and manufacturers to get as close to the manufacturing bounds as possible and defines these for future projects. Some companies even promote “print-a-thon” competitions for employees to breed creativity and experience with the tools, similar to what software companies do with “hackathons.”
Master the replaceable
As 3D printing becomes a normal experience in daily work, many companies adopt its use for low-risk applications in development. A common practice is to use printed parts as manufacturing aids and guides for other manufacturing operations on-site. Printing parts for manufacturing processes has a number of benefits. It provides experience using existing 3D models as an input for design, creating a clamping mechanism that perfectly holds a component requires exact geometry. Printing these components on-site can rapidly accelerate the development process by eliminating the wait time to receive the parts from a distributer. And from a business perspective all of the parts being printed could feasibly be replace by an existing component if the printed version does not deliver the desired performance. This last benefit has been valuable in the industrial machinery space as a broken part can be printed and used while the replacement is in transit, greatly improving up-time.
Not all steps are big
Bringing in a new tool to production doesn’t mean that you can only use that tool, nor does it mean that you have to be perfect with it at the start. 3D printing can be adopted at your own pace, but it still requires a first step no matter how small. Adoption is about learning the process, learning what the possibilities are and learning how it fits into your workflow. For a more in-depth analysis of how to incrementally adopt 3D printing, I would highly recommend Ashley Eckhoff’s article in Digital Engineering 24/7.
Siemens Digital Industries Software is driving transformation to enable a digital enterprise where engineering, manufacturing and electronics design meet tomorrow. Xcelerator, the comprehensive and integrated portfolio of software and services from Siemens Digital Industries Software, helps companies of all sizes create and leverage a comprehensive digital twin that provides organizations with new insights, opportunities and levels of automation to drive innovation.
For more information on Siemens Digital Industries Software products and services, visit siemens.com/software or follow us on LinkedIn, Twitter, Facebook and Instagram.
Siemens Digital Industries Software – Where today meets tomorrow