Make me a drone: the ideation
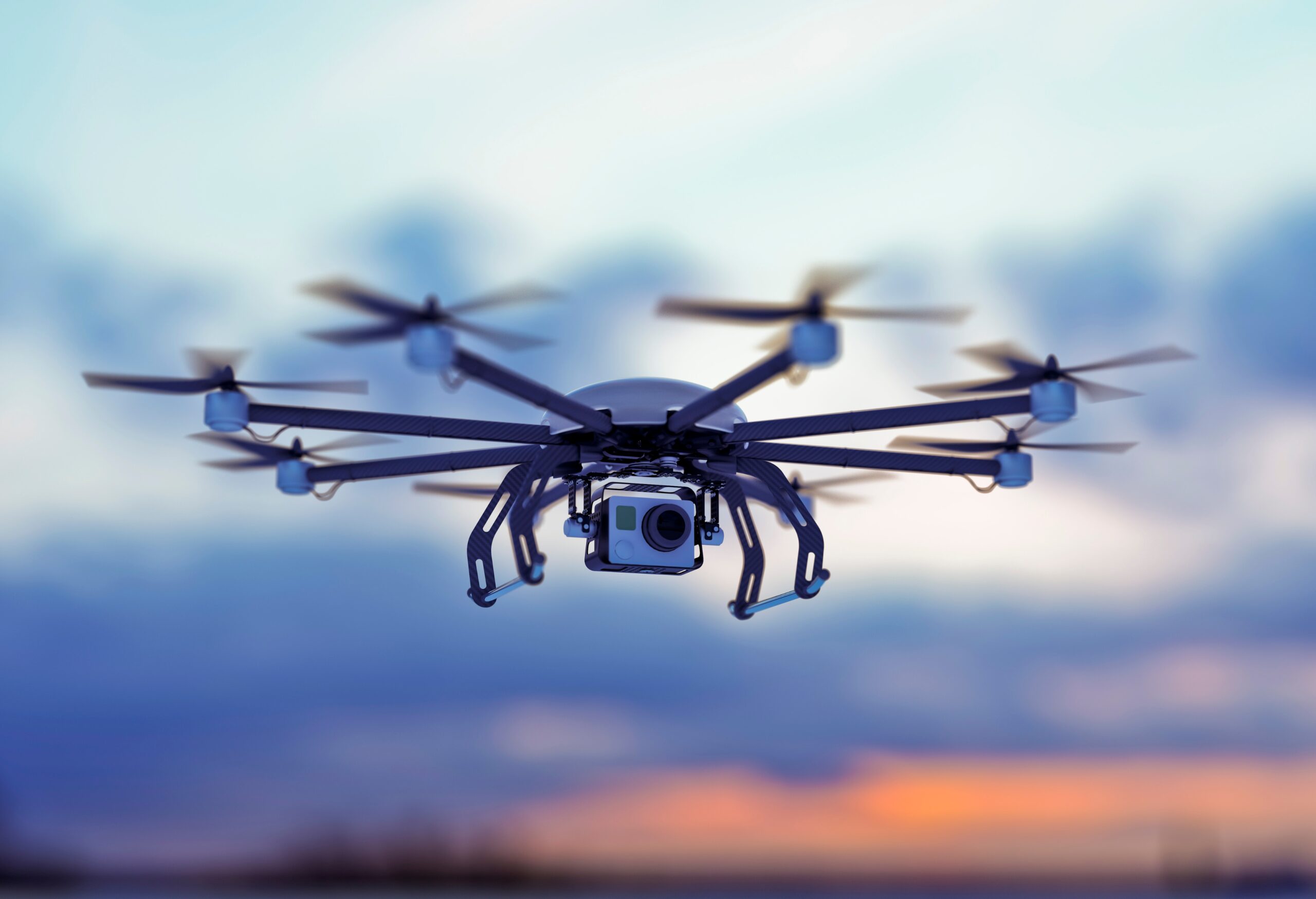
To take a look at the entire lifecycle of a product and the future of manufacturing, the Thought Leadership team here at Siemens Software decided to examine it through the lens of a thought experiment. The premise: what if you could tell a computer to make you a drone? What would that development process look like with a truly digitalized solution? The introduction to this new series from our team can be found here, but without diving into too much detail we have divided the process of an automatically manufactured drone into five key phases – ideation and concept creation, automated design and verification, intelligent marketplaces, artificial intelligence driven factories, and lifecycle. We’re calling the series “Make me a drone.”
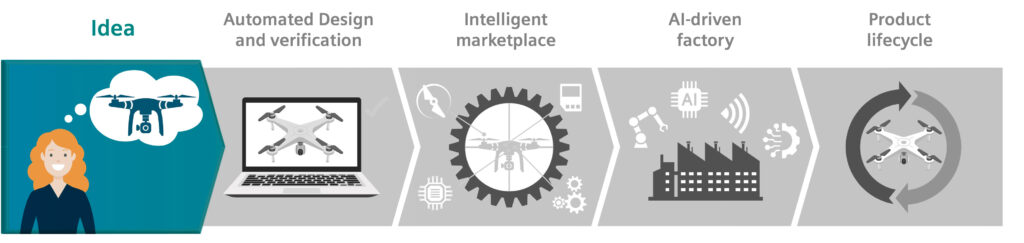
In this blog, we are focusing on the initial ‘Idea’ phase of the drone development. A drone can have a variety of system features depending on the application – a photography drone may require higher quality image capture, more stabilization at the cost of speed, and autonomy functions to follow a subject as they move. That is very different from the drones people choose to race which rely on low latency video connections, accurate controls, and higher top speeds. Communicating these requirements is the first step is creating a fully custom drone.
Model-Based Systems Engineering (MBSE) is that starting point for today’s innovative and smart products. As products and programs grow in complexity, next-generation MBSE tools enable seamless interoperability of models through product development and across its lifecycle. It all starts with the product definition, deciding what is important to the project, or in this case the drone.
The customer demands are captured as requirements that feed an automated development system, in turn defining the system architecture. With these inputs from the customer, the automated development system would generate a system architecture. The system architecture would include all the performance requirements of the customer, as well as regulatory standards, manufacturing processes, and plans for validating the project throughout development. The generated architecture is then federated to each of the relevant development domains required to create the drone – software, mechanical, electronics, and cabling – as specifications or as features to implement. These requirements may include electronics design and component selection, mechanical specifications for the propulsion system and manufacturing process, and software development to integrate the electronic components and supply an interface for controlling the drone. As the system architecture is refined by the development domains, which will be covered in a subsequent issue in this series, the changes are validated ensuring they still meet the requirements of the customer.
For such an integrated piece of technology, drone development requires continuous communication between development domains, in MBSE this is often called connected engineering and organic cooperation. This communication ensures that any change one development domain makes doesn’t inadvertently take the product outside the scope of another domain. For example, if the body of the drone is to be 3D printed, manufacturing needs to know where subsystems will fit in the model. Motors, flight controllers, and camera systems all can change the center of balance in the drone, but they may also require specialized cooling channels to prevent overheating or melting in the worst case. These challenges are understood and testing in the digital environment with multi-physics simulations and a variety of other system models to validate the drone meets the needs of all the development stakeholders.
Everything after the initial input from the customer is managed by MBSE in the digital twin to align the many different processes happening in the background of developing such a complex product like a drone. The MBSE solution provides the different product engineering disciplines—electrical, mechanical, software and cabling—the flexibility to define and optimize their systems while cooperatively developing the interfaces between them. MBSE connects all the sources of data and experts to create a comprehensive digital twin of the product and harnesses the digital enterprise to weave together engineering, manufacturing and even outside suppliers to add value at every step of development. This single source of truth of the digital twin enables earlier and continuous verification to the overarching product architecture even as the design moves into manufacturing and eventually into the real world. The data and requirements created in the concept or ideation phases of development act as guiderails for the rest of development to ensure the right product gets manufactured the right way.
We will cover each of these specific processes as they arise in a standard product lifecycle and now that we have an idea of what needs to be manufacturing it is time to start designing and analyzing the results.
We are looking forward to sharing more content in support of our thought experiment. By working with experts across Siemens we’ll report their insights to you and provide our own perspectives on potential future developments. If you want to follow our journey, look for collateral with the “Make me a drone” label.