Multi-disciplinary design is a game changer for machine engineering
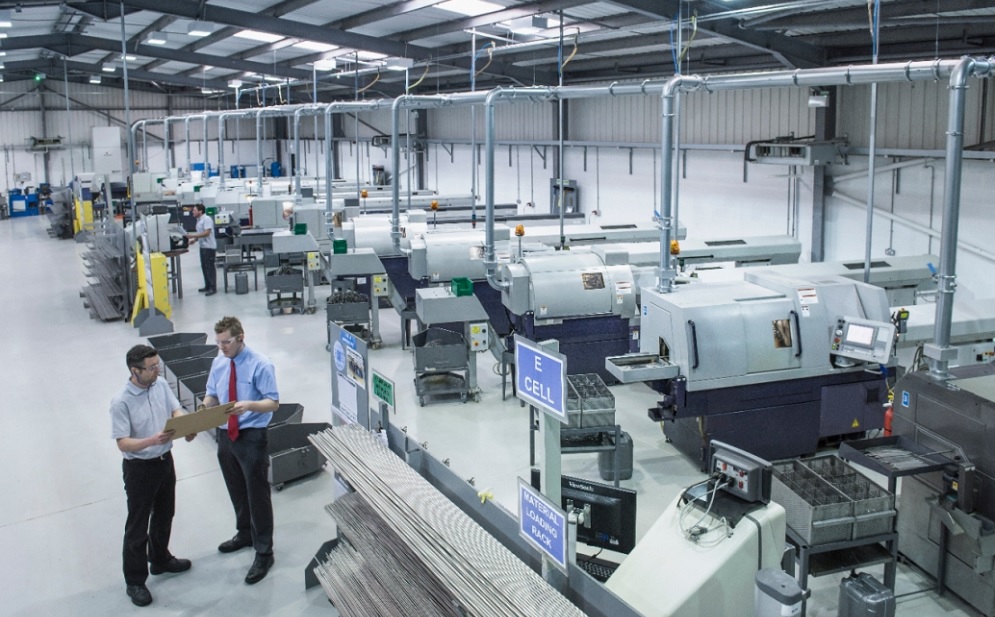
In a recent article in Digital Engineering 247, Rahul Garg, Vice President of Industrial Machinery and the SMB Program for Siemens Digital Industries Software, discusses the current complexity of building modern machines, which require software to be a part of the equation. The industrial machinery industry relied on mechanical computer-aided design (CAD) and the functioning assembly and arrangement in the past. However, machines have become more sophisticated in the last couple of decades, requiring a multi-disciplinary design process.
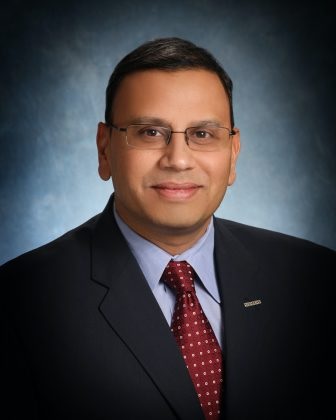
>Read the article.
Machine manufacturers are leveraging a multi-disciplinary design to spur manufacturing to greater efficiency. A multi-disciplinary design evaluates machine-building complexities, including engineering design and manufacturing.
Software and machine complexity
Formerly, the machine was viewed as a mechanical piece of equipment, like cars or planes. As a result, the manufacturing infrastructure usually had the mechanical design existing in one area and the electrical design, schematics, and software development in another place. However, now software is essential to adapt to shop-floor conditions, with machines responding to real-time sensor readings, like a cylinder extending and retracting based on differential pressure and flow regulation. Therefore, software becomes a game-changer in this environment for machine designers, providing valuable capabilities and features.
A multi-disciplinary design approach combines the capabilities and skillsets to propel mechanical engineering to a more collaborative environment, establishing an integrated approach and compressing timelines to move sophisticated machines to market. So, there is a significant effort to provide simulation into the design process, which incorporates a multi-discipline domain, finite element analysis, computational fluid dynamics, vibration, and harshness.
Additionally, machine builders depend on a comprehensive digital twin representing the physical machine, including the performance and manufacturing recipe. This setup includes the mechanical, electrical, hydraulic, fluid, pneumatics, design domains, performance, simulation, and automation code. And the digital twin incorporates the manufacturing and the entire service life of a machine.
Learn more in Rahul’s DE 247 article.
Software solutions
Siemens Digital Industries Software drives the transformation to enable a digital enterprise where engineering, manufacturing, and electronics design meet tomorrow.
Xcelerator is a comprehensive, integrated portfolio of software, services and an application development platform. The portfolio accelerates the transformation of businesses into digital enterprises. It unlocks a powerful industrial network effect – essential requirements to leverage complexity as a competitive advantage, no matter the industry or company, to transition seamlessly to create tomorrow’s complex, efficient machines.
About the author
Rahul Garg is Vice President of Industrial Machinery and the SMB Program for Siemens Digital Industries Software. He and his team are responsible for identifying and delivering strategic initiatives and developing solutions for the industry, working closely with industry-leading customers and providing thought leadership on new, emerging issues facing the machinery industry. Rahul’s experience and insights are derived from a 25-year career of delivering software-based solutions for product engineering and manufacturing innovation for the global manufacturing industry. He has held leadership positions in multiple areas, including research and development, program management, sales and P&L management, having focused exclusively on the industrial machinery and heavy equipment industry since 2007. Rahul holds a master’s degree in Computer Science from Wayne State University, with a concentration in Operations Management and Strategic Marketing, as well as a Bachelor of Computer Engineering degree in Computer Engineering from Bombay University.