Use 3D scanning software to address tooling downtime threats
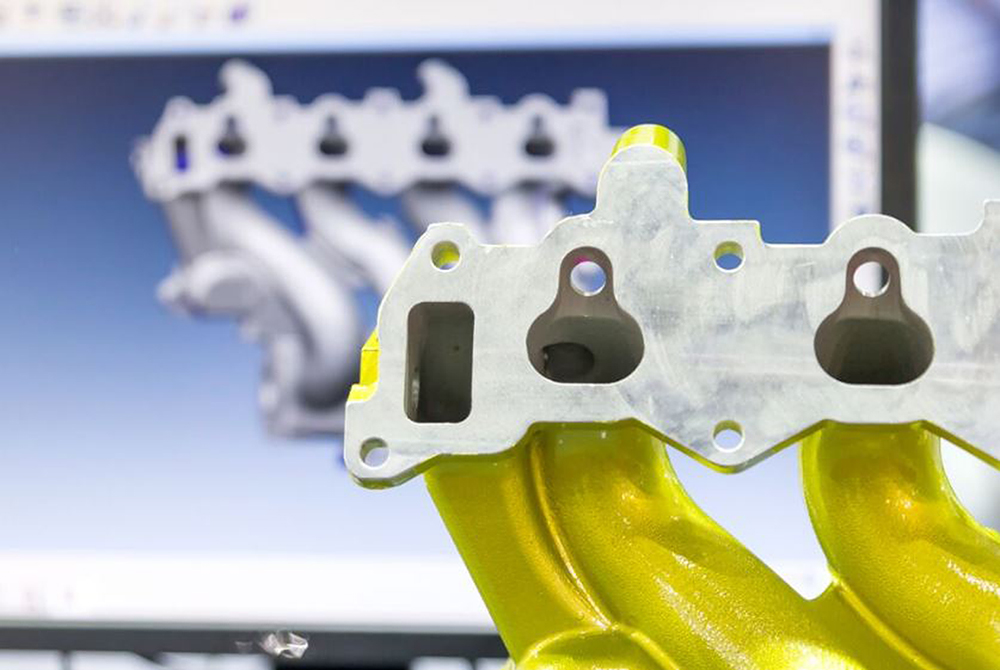
By: Ryan Haylock and Chris Himburg
Tooling failures can spell disaster in today’s just-in-time environment. A typical stamping plant could lose weeks of production when manufacturing tooling breaks, which could mean delayed shipments and lost business.
But savvy manufacturers have found a way to address these potential problems using a technology that’s affordable, easy to obtain and easy to use. More manufacturers are using 3D scanners and 3D scanning software to quickly replace tools, reduce downtime and minimize losses related to failures.
With 3D scanning software, manufacturers can quickly reengineer key tool surfaces. 3D scanners aren’t new, but in past years they may have been too expensive, particularly for smaller machine shops. Fortunately, 3D scanners are much more affordable today, and more manufacturers are reaping the rewards. Let’s take a closer look at why 3D scanners are becoming more important for machine tooling replacement.
Traditional tool replacement is complex
Even minor manufacturing tooling repairs can be time-consuming. Every change to the tool requires testing and verification. The process often calls for outsourcing repairs to a tooling vendor or waiting for a skilled staff technician to fix the tool.
In addition, variations and imperfections can occur during tooling production. Often, the tool must be altered to address shrinking, spring back or warpage, which are commonly not represented in a drawing or CAD file. Qualifying a part to the original specs can be challenging and often requires manual intervention and validation.
Oftentimes, this process requires multiple iterations and rounds of testing to get it right. It’s a lot of guesswork and waiting. Every minute spent dialing in or repairing a tool could add to downtime, which puts plants at risk to miss deliveries and potentially lose market share.
How the digital twin increases accuracy
What if an exact copy of the production tool was available instead of working from a 3D model? 3D scanners are allowing manufacturers to quickly perform digital validation, make digital repairs and capture tool development so they can get their equipment up and running faster.
Manufacturers use 3D scanners to create a digital replica or “twin” of the tool. A digital twin allows manufacturers to conduct comparative analysis so they can match a working, qualified tool with the surface of a damaged tool.
Designers can load the scans into their computer. Advanced 3D scanning software allows them to position the surfaces on top of each other to quickly identify any deformities or damaged surfaces. They can see exactly what they need to fix on the damaged tool. Comparative analysis minimizes rework and modifications because designers have more precise measurements, distances and locations of defects or failures.
The process doesn’t require a highly skilled technician’s eye or years of design experience to troubleshoot a failure and take corrective action. Designers simply compare the archived scan data of the working tool to the failed tool. The process helps manufacturers move fast and focus on responding to customer needs rather than maintenance.
Modern 3D scanners are user-friendly
More manufacturers are realizing the benefits of 3D scanners, but many organizations may wonder whether the technology is appropriate for their operations. A common concern is the availability of qualified workers to operate advanced technologies. Fortunately, 3D scanning software is making scanners much more intuitive than they were in the past; they don’t require significant training or an advanced engineering background to operate.
In addition, manufacturers can easily share the scanned tools across the organization, which is critical for companies that are expanding geographically or have multiple locations. It enables a new level of collaboration and provides a backup of a working part, regardless of where you’re located.
Comparative analysis can mean the difference between weeks and few hours to repair a tool. Learn more about how 3D scanners can reduce the potential for catastrophic tooling failures.
This concludes part one of our series on the key role 3D scanning software plays in preventing downtime. In part two, we discuss how 3D scanners and digital twins allow manufacturers create parts on-demand.
About the authors
Ryan Haylock is an NX design specialist on the Americas channel enablement team and is focused on assisting partners in learning, communicating, and demonstrating the Siemens PLM product suite. Prior to joining Siemens in 2007, Ryan held positions in the semiconductor capital equipment industry supporting corporate initiatives around design reuse & automation, commodity cost reduction, engineering process methodologies & tools, and business readiness. His experiences have helped him learn about the complexity of implementing corporate wide processes, executing against milestones and achieving bottom line results in complex machine design. Since joining Siemens a decade ago, he has continued to focus his efforts on helping customers achieve the value from our products and realize the true potential of PLM. Ryan has a bachelor’s in engineering from Michigan State University and is located in Michigan.
Chris Himburg is CAM Logic’s business development director for additive manufacturing and is a partner of Siemens PLM Software. His focus is on solving real-world manufacturing challenges by pushing 3D printing and 3D scanning technologies to their limits. After running a home theater and IT business, then committing to IT full-time, he followed his heart back to the engineering field where he has helped CAM Logic grow the additive manufacturing and 3D scanning portion of the business. He is a DIY enthusiast who enjoys tinkering and is excited about the future of the manufacturing industry. Chris is based in Michigan.