Efficient training of AI Vision for factory automation part 3
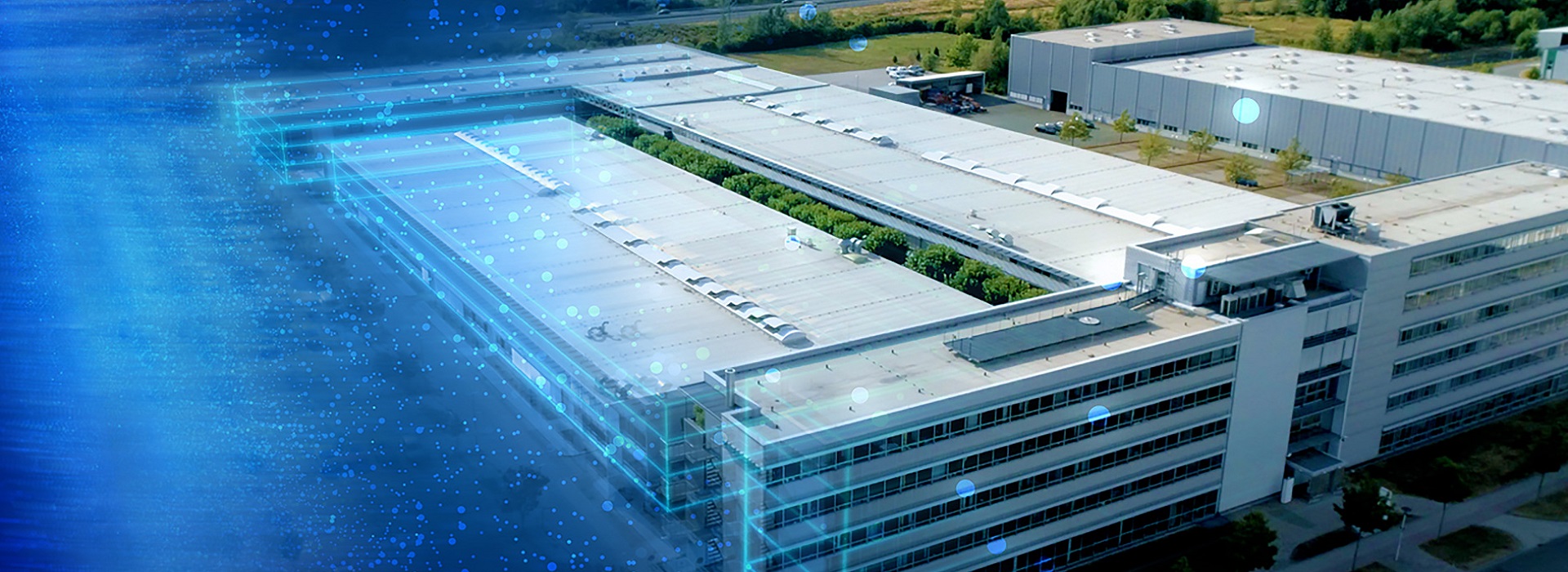
In part 1 of this series, we took a look at the challenges of training Artificial Intelligence (AI) and Machine Learning (ML) algorithms for factory use and then in part 2 we examined the most popular types of AI algorithms in that space – Supervised Learning (SL) and Reinforcement Learning (RL). Now in this final part we’re going to look at the latest advances in AI training, namely the comprehensive digital twin and synthetic data. To read part one, click here and to read part two, click here.
Part 3: The future of AI training
Endowing robots with human-like motor skills and the ability to perform tasks in a natural way is one of the important goals of robotics, with huge potential to boost industrial automation. A promising way to achieve this is by equipping robots with the ability to learn new skills by themselves, similar to how a human would learn. However, acquiring new motor skills is not a simple task. For robots, the continuous exploration space is massive – a robot can be at any given position at any given time and interact with its environment in infinite ways.
Using the comprehensive digital twin of the production system and product, it’s now possible to significantly shorten training and validation times for robotic system with AI/ML and integrated vision systems. This yields more robust and reliable systems with lower training time and resource costs then current real-world training methods.
For industrial AI training in a virtual environment, the actual robot, parts, and camera are replaced with virtual representations—aka the digital twin. Within the virtual environment, it is easy to set up the equipment, capture and annotate images, and devise test scenarios compared to devoting the time and resources of real equipment to the training process. Training the digital twin of the robot in a simulated environment not only accelerates and streamlines the training process, but also provides the ability to train when the real parts and products are physically available, such as the in the case of a new product that hasn’t entered mass production yet.
Now with the comprehensive digital twin of the robot, cameras, and software, engineers can simulate the whole design and training process upfront to check process logic and the layout of the robot station. This gives them an opportunity to improve things such as the robot station layout and gripper design early enough to uncover possible collisions, or to determine if the robot has poor range of motion in the defined workspace. Equally important, optimization of the AI algorithm and the robot control flow can be done completely within the software environment and immediately validated rather than requiring lengthy and expensive real-world testing, a major challenge today when designing or modifying a smart robotics solution.
One of the biggest benefits is combining the digital twin with synthetic data to efficiently train the industrial robotics system. Now it is possible to generate thousands or even millions of unique test cases quickly and automatically that can be used to teach the virtual robot. Using CAD files of the parts the robot will handle, software can generate randomly placed parts based on a physics engine. It then generates synthetic images using the virtual camera just as if the camera is viewing the actual objects on the manufacturing line. Camera pixel resolution, noise, ambient lighting effects, etc., can also be added to the synthetic image generation to mimic the actual camera behavior. The synthetic images can then be channeled to the robot’s image processing and AI training software and used exactly like real images. In addition, synthetic images can be automatically generated with whatever annotations might be required.
Virtual training based on a digital twin and synthetic data provides exciting new avenues for AI development, offering the ability to train AI faster and with more flexibility than ever before. Nearly limitless possibilities can be tested using a digital twin before the best one is deployed to the real robotics system. Leveraging this technology in the future, it could be possible to train an AI algorithm for producing a product, while the product itself is still in the development process, drastically reducing commissioning time. With the digital transformation at the forefront for many companies, the move to digital AI training is a simple one with many benefits that in coming years will revolutionize the way AI is trained and used in the factory.
Siemens Digital Industries Software is driving transformation to enable a digital enterprise where engineering, manufacturing and electronics design meet tomorrow. Xcelerator, the comprehensive and integrated portfolio of software and services from Siemens Digital Industries Software, helps companies of all sizes create and leverage a comprehensive digital twin that provides organizations with new insights, opportunities and levels of automation to drive innovation.
For more information on Siemens Digital Industries Software products and services, visit siemens.com/software or follow us on LinkedIn, Twitter, Facebook and Instagram.
Siemens Digital Industries Software – Where today meets tomorrow.