3D printing for energy applications
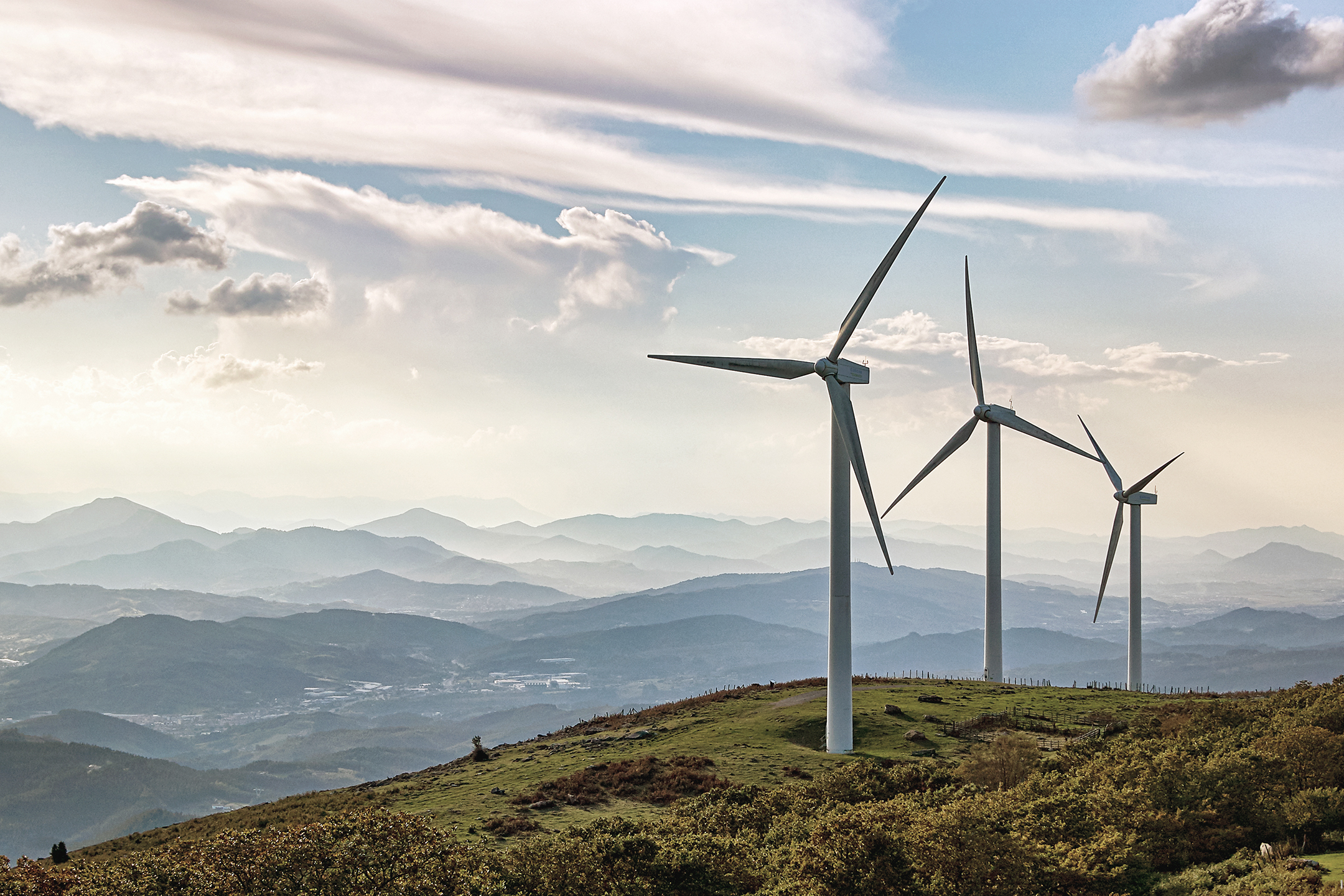
Ashley Eckhoff is back with another interview on what is happening with additive manufacturing (AM) technologies in different industries around the globe. Closing out the end of March, he talked with two Siemens experts from the energy and utilities space to find out what is happening today and what the future may look like in the next couple years. It is a great episode, John Nixon and John Lusty have a very fun demeanor, and I’d recommend checking out their series if you want more of the story beyond AM. But if you’re looking for a quick run down of what’s happening at the crossroads of additive and energy here are a few of the major points of this fantastic conversation.
Possibly the most important application of additive manufacturing in the energy and utilities space stems from the lifetime of these facilities. An electricity generation plant or chemical refinery is operating for 40 to 60 years, and it is constantly being improved over that lifetime. Systems are repaired and entirely new capacity added. Keeping a stock of custom-made parts for maybe not 60 years, but 25 to 40 years is a financially unsustainable decision for many operations. Not only are these parts one-of-a-kind, but they are also often massive, and hand built. AM provides a better solution, all that needs to be retained over that lifetime is the geometry of the component. Best case solution though is that a digital twin of the facility is available, and the printing requirements can be pulled directly from that resource.
As an extension of AM for component replacement, digital solutions can provide better overall performance to a system. If a pump needs to be replaced for a coolant or fluid loop, the blade geometry can be custom fit to the performance requirements of the system with topology optimization. Fluidic drag can be reduced in pipes and fittings to reduce the pump power needed, which also lowers the energy input to the system. But possibly the most interesting examples of increased system performance in the energy sector from AM are fluid-optimized heat exchangers. Nearly every energy system or chemical process requires a heat exchanger at some point in the loop. For thermal power plants (nuclear, thermal solar, gas-fired, etc.) the converted heat energy needs to be moved out of the system and towards the generator, which is more likely than not a high-pressure steam turbine. The efficiency of that heat exchanger has a direct, and often great, impact on the overall efficiency of the system. More power per unit fuel is great by nearly any metric.
And lastly, margins are extremely important for the energy industry. If your company is generating power for sale to the grid, you have to match your output to the requirements of the grid. At the same time fuel costs can fluctuate with the market, forcing companies to eat costs at time until it can be recouped later. If operating costs can be reduced as much as possible, it makes these variable numbers less of a fiscal challenge in the long run. And as regulation tightens around some parts of the industry, savings now will have a benefit beyond direct financial incentive. Lower input and higher efficiencies mean lower emissions which impact the environment and even the balance sheet depending on the region. That doesn’t only apply to traditional fossil power either, the folks at Siemens Energy are continuously working to make the wind mills more power efficient. Capturing more of the available energy through better blade shapes or materials, lighter weight gears inside to limit losses from inertia, and much more.
Even if you are not as fascinated by our energy infrastructure as I am, this is a great episode. And if one of the major topics here sparked some interest you can find a lot more of the discussion in the episode. These three guys also talk business on what it means to implement digital solutions for pulling in a younger workforce and capturing some of the knowledge of the retiring generation. Thanks for reading and I hope you found this topic as interesting as I did.
Siemens Digital Industries Software is driving transformation to enable a digital enterprise where engineering, manufacturing and electronics design meet tomorrow. Xcelerator, the comprehensive and integrated portfolio of software and services from Siemens Digital Industries Software, helps companies of all sizes create and leverage a comprehensive digital twin that provides organizations with new insights, opportunities and levels of automation to drive innovation.
For more information on Siemens Digital Industries Software products and services, visit siemens.com/software or follow us on LinkedIn, Twitter, Facebook and Instagram.
Siemens Digital Industries Software – Where today meets tomorrow