From ER to factory floor: AI for a healthier future
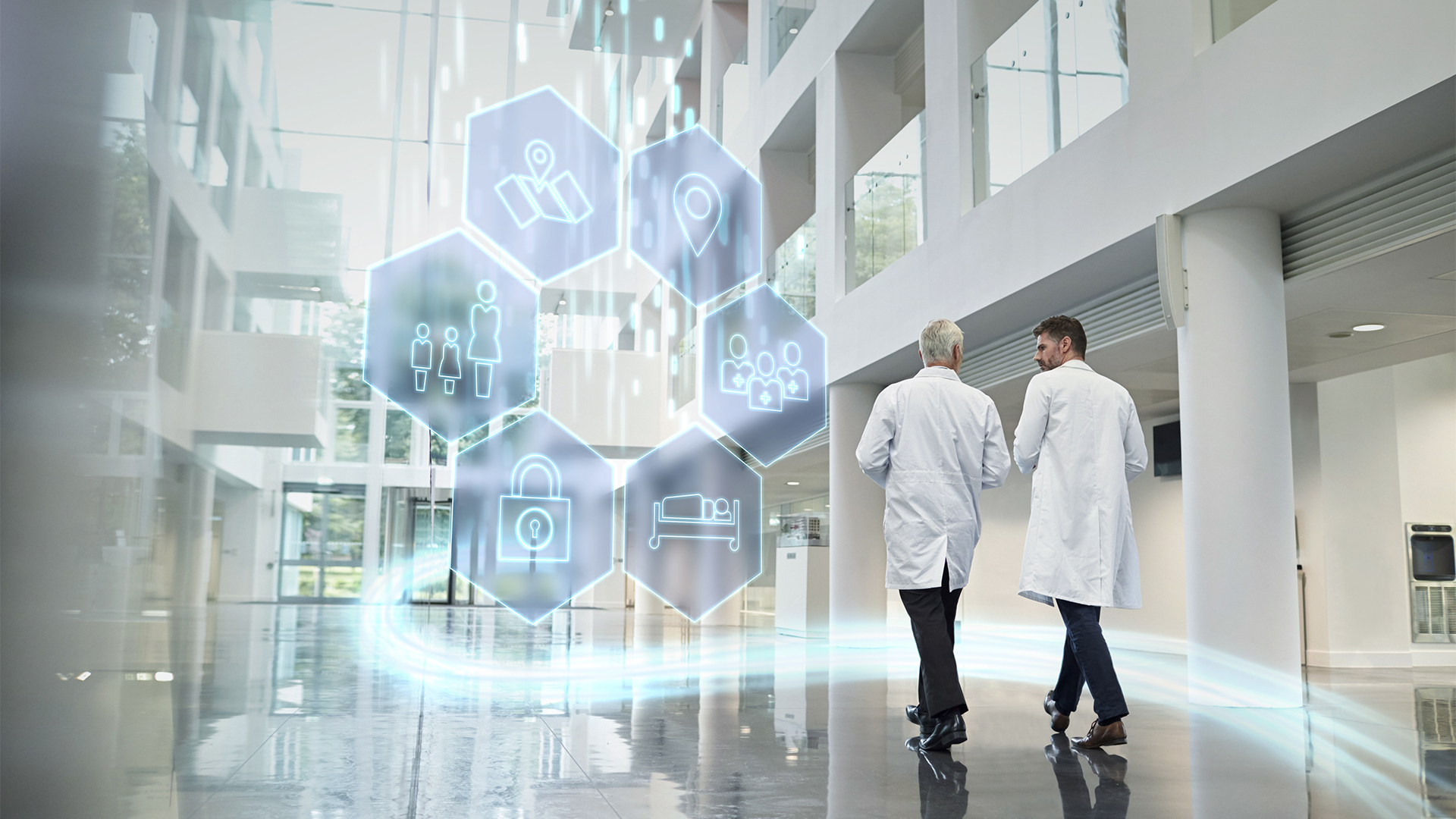
I recently read an article about AI being deployed to hospitals and ERs to detect deadly infections and downward spirals hours before doctors and nurses would, saving lives. This is thanks to AIs unmatched ability to quickly collate and analyze data before offering an at-a-glance summery to healthcare professionals. But the healthcare industry is not the only industry where the ability to accurately predict problems in a critical environment early on is a huge asset. Fundamentally, the challenges with keeping a factory running smoothly and a human body healthy are similar. Qualified personnel must sift through voluminous data to try and diagnose issues or better yet, address them before they become a problem. While at first glance it might seem the ER and the factory floor have little in common, the truth is both fields have a clear use case for the impressive analytical ability of AI. In the manufacturing space this process is known as predictive maintenance.
In this modern, connected, world everything from a multi-million-dollar CNC machine to a lightbulb is packed with sensors and electronics dispensing a constant stream of data covering a wide variety of metrics. This data can be used to measure productivity, check for problems, develop maintenance schedules, and any number of other applications but right now much of that valuable data is going to waste. Due to its sheer volume—up to 2TB a day in some advanced factories—analyzing all the data produced in a day would be a monumental task and impractical using conventional methods. By and large this data provides neither insight into production nor a clear warning of any issues, conventional wisdom would simply discard it rather than expending the resources required to analyze it. However, this does not mean the data as a whole is without value.
When all the data streaming out of a factory is used to train a machine learning algorithm instead of allowing it to disappear into the ether, suddenly millions of pieces of innocuous data become the framework for what an AI knows as “normal” in a factory. This functions in much the same way a medical AI trained on thousands of patient records can understand what a healthy human is and then be educated enough to recognize the symptoms of a disease. With a framework built on dozens or hundreds of metrics established, it becomes possible for an AI to spot aberrant patterns leading to an imminent failure. Patterns that would either be lost in the volume of data or simply overlooked as a minor variance by a human operator. Gathering a collection of symptoms that may be individually overlooked before collating them into actionable information is where AI can shine, both in the factory and the hospital ward.
Predicting impending critical failures is not the only way for AI to show its worth and, in fact, is not as valuable as the preventative care it can offer – the powerful AI-driven predictive maintenance. Rather than waiting for a failure to be imminent, predictive maintenance uses the abundant data provided by factory IoT devices to help optimize maintenance schedules. AI can help technicians and factory managers decide when the best time to take a machine down for longer maintenance is on top of giving advance warning of any critical failures. Since recommendations draw on both production machine data and manufacturing targets, maintenance schedules are developed to both maximize the lifespan of the machine while minimizing the impact on production. Something a more traditional static maintenance schedule would not allow for. Thanks to the power of AI, maintenance happens exactly when required cutting down on both wasted time and costly emergency repairs. Just like how a regular checkup at the doctors can head off major illness, predictive maintenance provides the same peace of mind in the factory.
Despite their obvious differences, humans, and machines both need regular care from experienced professionals who are required to sift through vast quantities of data to make an accurate diagnosis. AI presents a convenient solution to the issue of having more available data than experienced eyes can possibly absorb, comparing all available data points to create a holistic assessment of any issues – present or future. While the human touch of doctors and technicians is not something that will be easily replaced by AI, now or ever, AI can provide faster, more concise data analysis of the highest quality, allowing those with the knowledge to do the best work possible without cumbersome clerical work, saving time, money, and ultimately, lives.
Siemens Digital Industries Software is driving transformation to enable a digital enterprise where engineering, manufacturing and electronics design meet tomorrow. Xcelerator, the comprehensive and integrated portfolio of software and services from Siemens Digital Industries Software, helps companies of all sizes create and leverage a comprehensive digital twin that provides organizations with new insights, opportunities and levels of automation to drive innovation.
For more information on Siemens Digital Industries Software products and services, visit siemens.com/software or follow us on LinkedIn, Twitter, Facebook and Instagram.
Siemens Digital Industries Software – Where today meets tomorrow.