MBSE: Advancing system engineering for Aerospace & Defense – part 4
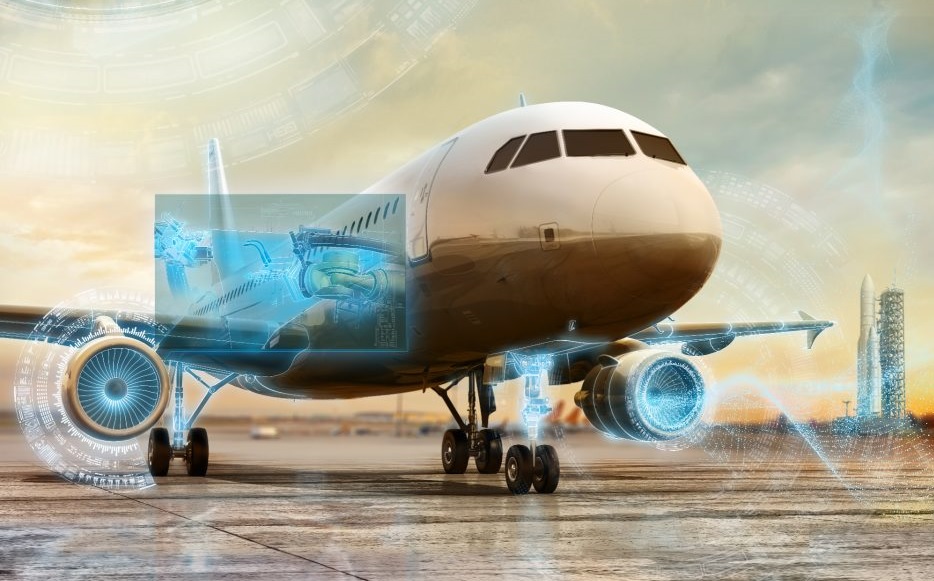
The innovative technologies that utilized science and math with skillful resourcefulness and allowed for human flight are a monument to the achievements of the 20th century. However, because air travel is ubiquitous, the industry has not seen tremendous change in several decades. The push for greater efficiency and more environmentally sustainable flight has brought innovation, and with-it greater complexity. New accomplishments like sustainability, making flight safer, more accessible, faster and maintainable has brought the need for new development practices.
In this fourth and final blog in our series, we address the new requirements essential to integrating new systems because of growing necessities, goals and standards that make building a modern aircraft successful and more challenging. The traditional V-diagram for aircraft development, referenced in a previous blog, was the standard; however, the sophistication of new systems is causing current engineering methods to falter and cause overruns.
Model-based systems engineering (MBSE) increases the system’s knowledge by managing requirements, modeling the system, verifying the results and managing integrations. It makes it possible to have effective programs.
Learn more about MBSE for aerospace, at Siemens Special Edition of MBSE for dummies. Also, read about the connections between every domain in the Xcelerator portfolio.
MBSE manages system engineering requirements
It is crucial to determine system features and functions at the project’s outset. For example, designing a plane begins with an overall idea coupled with the desired technologies and conditions. Imagine that you’re having dinner with the customer CEO and writing it all down on a napkin. This plane can fly 2,000 miles, with a specific number of passengers and at a top speed over specific routes with their own set of conditions.
These decisions will inform the project architecture. So, the more complex the product, the more requirements are necessary to define the system. Keeping this information in a single source of truth, rather than several different documents scattered across the development process, ensures knowledge sharing to the team to understand the final goal.
More existing engineering work provides better direction toward producing innovative solutions to problems; and definitive information management is key in accessing those developments. Thousands of options must be tested against all the system requirements and losing even one data point is costly. The positive results of managed requirements include enabling flexible development practices, which are essential for the transition to software and electronics in aircraft systems.
System modeling
When requirements link to a single source, it allows for testing many design concepts to integrate modeling capabilities. An excellent example of this could be a wing’s flight characteristics that require further clarification. A robust modeling environment enables the testing of various options before committing to the specific manufacturing resources.
And a wing would have many responses with unique wing shapes or designs which include specifications that find the ideal fit for the aircraft. As a result, model refinement occurs as information and ideas are exchanged between groups. For instance, experts in aerodynamics can deliver a wing form to structural designers, and they create the internal support, receiving an edited design while remaining within the structural group requirement. So, whatever the circumstance of events, it is a guided methodology adjacent to the model – for team members’ collaboration to create an optimum product.
System verification
Ideally, after this aircraft interaction, it would be natural to progress to the next development phase; however, mistakes can still occur. Therefore, MBSE provides a continuous framework to verify corrections by addressing the following questions:
- Does the electronic control system effectively communicate correct information regarding the controlled systems status?
- Will an internal structure safely support the external component weight?
- Will a part survive the projected aircraft lifetime, and can it be replaced efficiently?
These questions are answered through the development verification process, from concept to service and decommission.
MBSE manages complex system integrations
MBSE is highly valuable in complex systems, integrating different workgroups, often for large-scale and global aerospace projects. Therefore, parts from two suppliers and the OEM in one region must interface with in-house components, appearing like everything is created in a single group. So, it’s essential to manage these interconnections between suppliers and OEMs, enabling a design in parallel to reduce the total development schedules of massive projects.
Subsequently, management relies on the initial requirements during the concept phase, repeating this process as issues arise and implementing solutions. This process is not merely focusing on the mechanical, as software communicates with mechatronic components to understand the hardware systems’ impact. Consequently, a digital MBSE solution enables constant integration across the entire development cycle.
Numerous workflows and practices exist within an MBSE framework to enable complex development without the high cost of time required by previous systems engineering iterations.
Learn more in our eBook about how MBSE accelerates aircraft development. Chapter four covers the topic in this blog.
Siemens Digital Industries Software is driving transformation to enable a digital enterprise where engineering, manufacturing and electronics design meet tomorrow.
Xcelerator, the comprehensive and integrated portfolio of software and services from Siemens Digital Industries Software, helps companies of all sizes create and leverage a comprehensive digital twin that provides organizations with new insights, opportunities and levels of automation to drive innovation.
For more information on Siemens Digital Industries Software products and services, visit siemens.com/software or follow us on LinkedIn, Twitter, Facebook and Instagram. Siemens Digital Industries Software – Where today meets tomorrow
Related Links:
MBSE: Future of aerospace industry – part 1
MBSE: Reassessing systems engineering – part 2
MBSE: Model-based approach transforms Aerospace & Defense – part 3
MBSE: Advancing system engineering for Aerospace & Defense – part 4