Realise the power of the dirty digital twin
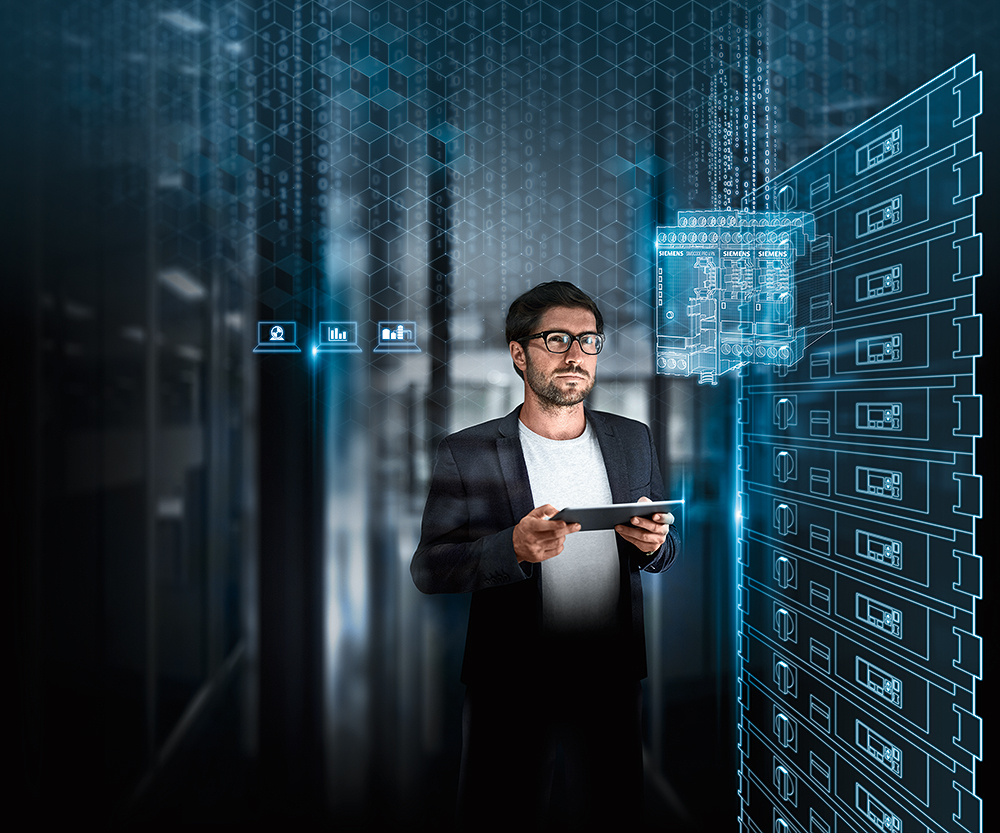
While presenting at a recent digitalisation conference in the United Kingdom, I asked the question of over 200 people in the audience, “Who uses digitalisation in your companies right now?” All 200 hands went up.
My follow-up question: “Who uses a full digital twin or thread?” – elicited no response.
The cause of this could be the British trait of not blowing one’s own trumpet. Alternatively, it’s more likely that everyone has already seen what can be accomplished with the use of digital twin – but no one thinks they’re at that point in the journey to take advantage of it, so they’re not ready to start.
The general perception of digital twin is that it’s a great idea with immense power and results in considerable value. The concept of having the ability to digitally represent your asset in a virtual world and predicting what could physically happen in a digital twin example is phenomenal. Additionally, providing a delivery method exhibiting one-of-a kind-experiences, via predictive intelligence embedded into the model, facilitates observation of customer behaviour, displaying alterations to usage, environment or design.
The outcome: being able to implement changes into the digital twin, based on a myriad of factors, to simulate results-driven data which can provide the means for building a better product.
However, first, the digital twin can mean many things to many people: how can we clearly define it? The digital twin is simply a digital representation of a real-life object or process. It must include some inputs, either assumed or from measured data, and must output information you didn’t have before.
To give a simple digital twin example: a person sits in a room and is either comfortable with the temperature or not. The simplest digital twin would be a spreadsheet with an input cell for temperature and an output cell of yes/no with a calculation related to maximum and minimum temperature. Adding on a 3D CAD model of the room, a full CFD simulation of airflow and temperature increases the fidelity of the model, but it’s still effectively the same digital twin.
The next step then is whether it’s a connected digital twin, or a standalone digital twin. Connected digital twins would automatically feedback the temperature from the room into the model, usually via an Internet-connected sensor and online digital twin model. The standalone digital twin has the temperature read by a person, then manually entered into the digital twin model.
Most companies have some digital representation to their assets, though they perceive it to be incomplete. Therefore, the effort to complete that model seems too significant, so they don’t try.
However, it isn’t less of a digital twin just because it’s not a full 3D representation. This is the concept of the dirty digital twin.
It’s important to remember that you have digital data, regardless of its completion status. Even in its current state, you still have the power to extract predictive analysis. So, you begin by recognizing the current state and begin to connect the pieces, developing a roadmap.
A roadmap: digital twin example
This roadmap of portraying the development process serves as a guide to:
• Define requirements
• Design the product
• Plan production
• Plan documentation
• Initiate production
• Package and ship
The stages of any digital twin begin with paper drawings, including a printout of requirements, along with documentation shipped with the product. These drawings are passed digitally to the documentation team to begin production.
At production, the requirements and parameters are automatically moved onto the design, via CAE, for full validation and verification. Then, CAD enables the creation of live models, embedded into production and accessible online by consumers, receiving up-to-date information.
Barriers to the digital twin
Some barriers to utilising the digital twin include crucial processes which are currently being held up by manual intervention. These require constant monitoring of critical measurements, and then entering those measurements into the standalone digital twin.
However, a connected digital twin is a significant improvement. Though perceived as difficult, the advent of Internet of Things operating systems solves this dilemma.
Another barrier is that every company perceives their situation or industry to be unique – be it defence, mechanical manufacturing, chemical or environment. It may be true, but you still need to ask the question as to why you aren’t leveraging connected digital twin technology.
One solution to addressing this question is to take a broader approach when looking at your entire process, and focus on one particular area which could be transformed by the digital twin. For example, discontinue copying your spreadsheet into a CAD model and store it with more visibility in a broader system. Or, proceed by using part of your process for the digital twin.
Another example is the design and reengineering upgrades of a naval vessel ― an overwhelming task. You could start small by choosing to focus on one problem, like the pumps running too hot. Utilizing a physics-based model of a submarine, and beginning with a 1D or 2D system of the vessel, results in a simpler model for predictive simulation. This operative representation allows for easy monitoring, which goes back into the predictive analysis model.
This method of starting small and focusing on a specific area within your process which could benefit from the digital twin can be incredibly effective. Attention to those critical processes which might be held up by more conventional means allows the digital twin’s beneficial properties to make positive improvements – without spending the time and money for analysing the entire process.
Join the evolution ― power of the digital twin
The dirty digital twin is a change in thinking, an evolution to what people are accustomed to doing. Once you locate the breaks in your system, you can then use a digital twin example to discover how to fix only those areas.
By starting small – using a minimalist approach to 3D technology and focusing on one or two points in your process which might be problematic, or currently performed through manual means – you discover the advantages to leveraging the digital twin to revolutionise your production.
This concludes part one on our series about the dirty digital twin. In part two, we discuss how companies can start leveraging the benefits of 3D technology right away when they’ve implemented a dirty digital twin.
About the author
Bruce Jackson is an account orchestrator for Siemens Digital Industries Software and works closely with aerospace and defence companies in the U.K. He has been working in the PLM and CAE space for more than 25 years and is currently working with companies across Europe to help them achieve productivity gains through digitalisation.
Comments