Product lifecycle management for machine builders brings digital transformation
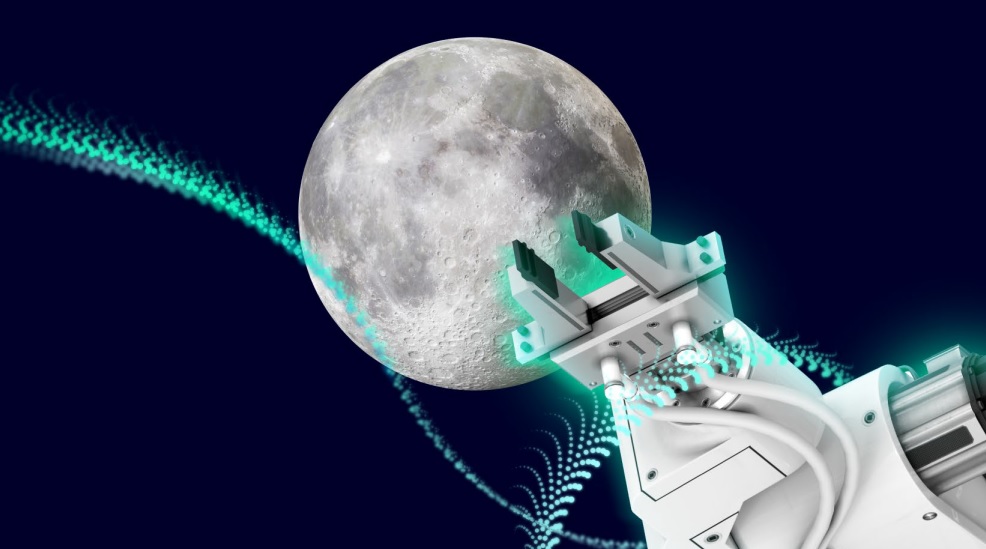
The global industrial machinery and equipment industry grows increasingly more complex each year. Many machine and equipment builders are dealing with outdated technology, legacy procedures, complex workflow processes, and slow projects leading to delays that impede future orders and jeopardize staff morale.
Therefore, there is an essential need for a templatized tool with a minimum cost of ownership that can effectively track changing customer requirements while eagerly cloning and reusing data across projects to satiate quickly and scale on an impulse. With Siemens Digital Industries Software, machine and equipment builders advance with an instant-on, cloud-based platform pre-configured with best practices. Therefore, machine and equipment builders will immediately improve their output. Organizations make an enormous leap forward for their business by making a small investment in digitalization.
Learn more in the Executive Brief.
The current machinery and equipment market is customer-driven, requiring more operators and complex machines to produce products in assorted colors, sizes, and shapes. Simultaneously, customers are demanding more, continually changing their requirements; therefore, machine and equipment builders face much pressure to update projects quickly while maintaining competitiveness globally.
To extend beyond the global competition, keep the best employees, retain complex customer requirements, and increase profitability, machine and equipment builders must advance in this marketplace. They can accomplish this by adopting a cloud-based, templatized, easily deployable approach to product lifecycle management. As a result, machine and equipment builders can track complex customer requirements effortlessly, overcome machine changes, leverage built-in best practices to update processes, and bring reliable, flexible machines to market quickly while maintaining market share and sustaining employees.
Overcome global competition and sustain staff with project management tools
The path to digital transformation and business process improvement begins with a cloud-based project, process, and requirements management tools. SaaS tools provide machine and equipment builders with the ability to identify information and monitor and deliver project markers via real-time dashboards. Integrated dashboards offer a project’s progress transparency while providing traceability across the engineering design process.
When machine configuration and reuse tools integrate with project, process, and requirements management tools, a synchronization occurs within the organizational ecosystem. This scenario allows for revamping project information across multiple orders, project management tools enable quick and efficient remote collaboration. Also, requirements and timeline transparency to the budgets are essential to meet goals and to remain competitive.
When a company or organization does not adhere to customer requirements, timelines, and budgets, it stifles the project management process. These delays can negatively affect organizational output, which leads to a loss in immediate revenue and straining staff whose expectations change given the paradigm shift with the COVID-19 pandemic. Delays can threaten future income, causing dissatisfaction with operators’, machine, and equipment builders’ output. A loss in business brings a loss in competitors’ market share who are unencumbered by legacy technology and business processes. They can afford to offer lower price points to win orders. Therefore, cloud-based project, process, and requirements management tools assist machine and equipment builders in avoiding competitive pressures and staffing challenges.
Machine configuration and reuse
Customer requirements are met by compounding project utility, process, and requirements management tools with a machine configuration and reuse approach. Machine configuration and reuse allow machine and equipment builders to use templates with a cloud-based software system; customized to fit engineering needs, from the design domain to the quality control department. It is a pre-configured system that permits machine builders to quickly respond to dynamic customer requirements, with the ability to source, clone, and manage machine structure and computer-aided design (CAD) documents as synchronized business objects.
In the meantime, workflow and version management tools can track order development and maturity in each phase of a project’s lifecycle. Therefore, machine configuration and reuse make change management easier across the enterprise, so machine and equipment builders can instantly begin storing project data in the cloud for reuse. Also, they can standardize their design practices to address dynamic customer requirements and design practices to understand and improve long-term machine maintainability, reducing possible repair costs. Subsequently, machine lifecycles will extend beyond the standard measure, extending a machine’s productivity and profitability.
Xcelerator, the comprehensive and integrated portfolio of software and services from Siemens Digital Industries Software, helps companies of all sizes create and leverage a comprehensive digital twin that provides organizations with new insights, opportunities and levels of automation to drive innovation.
For more information on Siemens Digital Industries Software products and services, visit siemens.com/software or follow us on LinkedIn, Twitter, Facebook and Instagram. Siemens Digital Industries Software – where today meets tomorrow.
Comments
Leave a Reply
You must be logged in to post a comment.
I notice that recently more and more entrepreneurs prefer digitalization of the industry of industrial machinery and equipment.
In general, the digital transformation of business is necessary at all stages of doing business, for this they create special software
if we even talk about documentation, then it can also be digitized safely, for example in https://fluix.io/digital-transformationthere is such a function. As you mentioned in the article, business needs to be scaled
it is a key idea of development think that red tape is one factor respects scaling.