Podcast: Understanding Siemens NX’s New Sketch Solver – Transcript
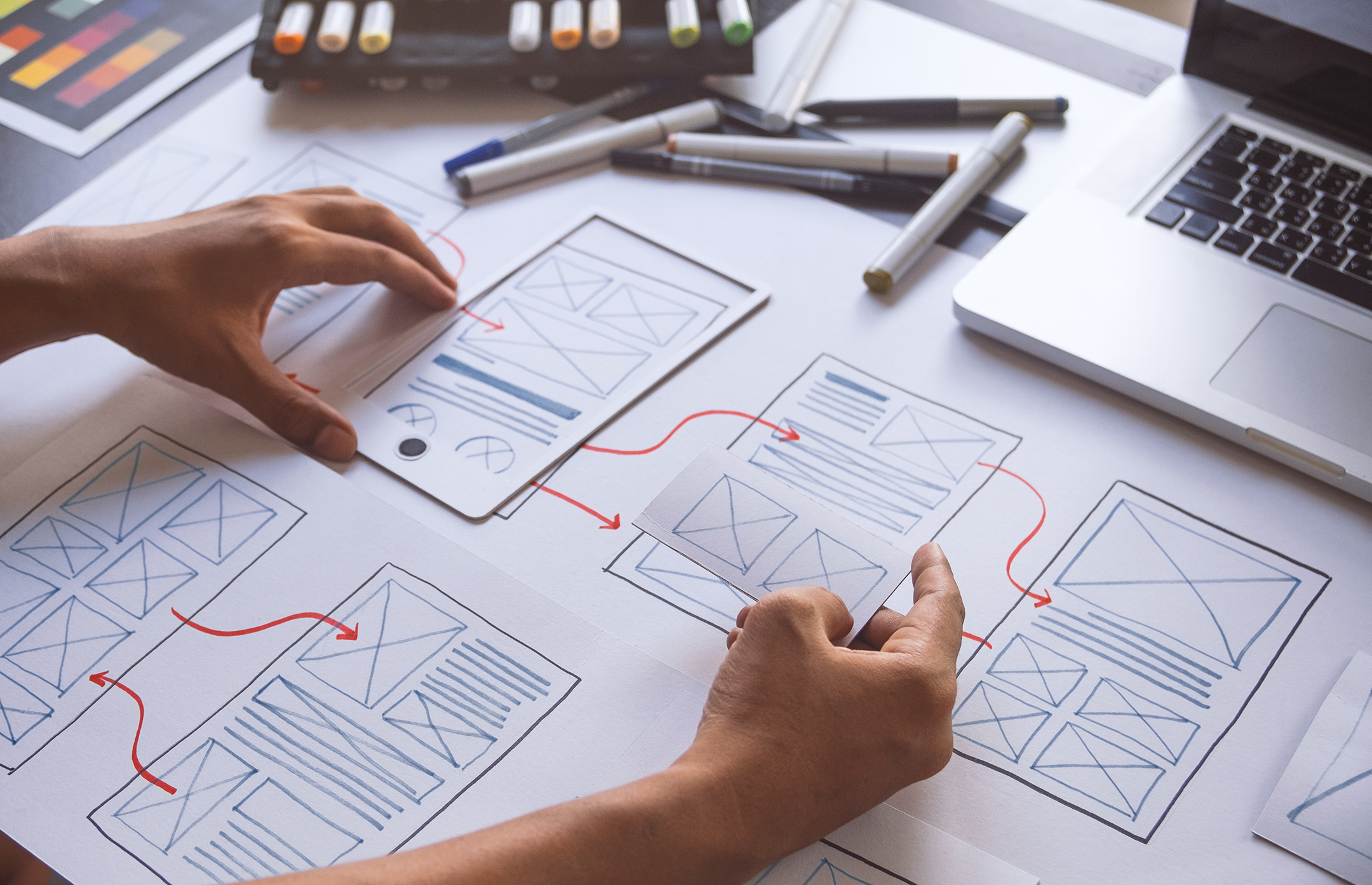
I recently had the opportunety to chat with Scott Felber and Mike Yoder from the NX Product Marketing and Management team about the invotive work they’ve done with NX’s new sketch solver. To listen to the full podcast, click here, but for those who prefer reading the full transcript is available below.
Spencer Acain: Hello and welcome to the Next Generation Design podcast, where today we’ll be looking at the innovative work Siemens is doing to improve the design process. I’m your host, Spencer Acain, and today we are joined by Scott Felber and Mike Yoder from the NX Product Marketing and Management team. Scott works in the Product Marketing group, and Mike works in the Product Management group and is focused on the NX design tools. Welcome, Scott, Mike.
Scott Felber: Thank you, Spencer.
Mike Yoder: Thank you, Spencer.
Spencer Acain: So before we get started, how about we talk a little bit about you guys’ background? So, if you wanted to start Scott?
Scott Felber: My name is Scott Felber. I’m with the NX Product Marketing team. I’ve been with the company, going on 32 years almost now. Lately, I’ve been focusing mostly on NX product marketing. And one of my big areas of focus is helping bring the NX sketch product out to the market to help our customers get the most advantage and be the most productive they can with the new tool.
Spencer Acain: That’s great. And how about you, Mike? Can you give us a little bit about your background?
Mike Yoder: Yes, I’m NX Product Manager. I have responsibility for the design application inside of our CAD tool. And I’ve been with Siemens, this is my 26th year now. And I’ve been on the product management team for about six years. And like Scott, working with customers to bring them on to the new sketcher.
Spencer Acain: Can you guys tell us a little bit about what you’ve been working on recently? I think you mentioned a new sketcher.
Mike Yoder: Yes, we started development of a new sketch solver several years ago. And this is kind of a smart solver, it finds geometric relationships for you inside the sketch, removing the need to place all the geometric constraints that we had with our old solver and just see in other CAD tools. This new sketch environment also brings a new user interaction, it’s a lot more streamline, a lot less clicking on the screen to get your job done everyday.
Spencer Acain: I see. So you’ve streamlined the process a lot. Can you tell me what prompted you to make these changes in the solver? Why are innovating on this right now?
Scott Felber: What we’re really trying to do is we’re trying to make MCAD innovative in the marketplace today. A lot of people perceive MCAD and design tools as being all the same. And there’s no differentiation between the two. What we’re doing here at Siemens is we’re looking at all the things we do every day to help the design process make people more efficient in their design process. So, what we want to do is we want to just bring innovation. And if you look at sketching, the traditional sketching methodology and workflows, there’s been really no attempt to make it any different than people have been doing over the last three decades. So, we did as we stepped back and say, “Hey, what can we do now with the new computing power to be able to make this sketcher more efficient, and make people get their work done a lot faster?” So, that’s really what prompted us to do this change.
Spencer Acain: I see. So, you’re kind of shifting the paradigm of what’s been going for the last 30 or even 40 years. We are trying to bring it to be a little more intuitive, would you say?
Mike Yoder: We’re aiming kind of like the back of a napkin sketch, where all of the engineering and intent is understood just on a hand-drawn sketch without the need to place the constraints. And that’s really what our new sketching environment brings to the table here.
Spencer Acain: I see. And you mentioned that this is going to help speed things up and make things faster. Do you have any idea how big of an improvement we’re looking at with this sort of change?
Scott Felber: Yeah, we went ahead and we had some third-party studies done early on when we’re developing this new tool. And we found that people can have a 30% reduction in the time they spent sketching. And if you look at all of MCAD and all the design across all the tools everyone uses, sketching as the one tool every CAD system does and people use it a lot. It’s really one of the basics of CAD. And what we’re saying is we’re going to take 30% of the time you use doing the one thing you probably do more than anything else, it’ll eliminate that time from your process, so you can get your job done faster.
Spencer Acain: That sounds like it’d be a huge time saver. I know, I’ve used several different sketching tools and different programs, and it’s definitely been a bit of a time sink to work through all of these kinds of constraints and everything. So, it sounds like you’re making the process more natural, which is absolutely fantastic. But can you tell me why it’s happening now more so than in the past? Like you said, it’s been 30 years or more. Why are you guys the first ones to be doing this?
Mike Yoder: Well, I think the mainstream tools inside of a CAD system, people get into maybe a rut with it. And they develop it to the point of where it’s really good, which is what we had beforehand, and which is what many of our competitors have quality sketching tools out there also. But as alluded to earlier, we really wanted to push the boundaries and see how we can save people time on their day-to-day jobs doing something that they do multiple times a day. So, when we step back and looked at what sketching involves, there are really three things: there’s the creation of the curve geometry itself, the geometric constraining, and then the dimensional constraining. And as I alluded to earlier, one of the areas that we’ve streamlined the interaction is with dimension creation. And then obviously, we’ve talked about the new solver and removing the need to create geometric constraints on every piece of geometry in the sketch.
Spencer Acain: I see. Can you explain a little bit how this new solver works? How are you able to eliminate, basically, 30% of the work for sketching just like that?
Mike Yoder: When we did studies early on, when we first had this concept, we did some timing trials, looked at how much time people spent creating geometry, creating constraints, and creating dimensions. And the curved geometry was the largest part; the creation of geometric constraints, we feel was about 30%, based on the timing; and then the remainder was dimension. What this new solver does, instead of forcing the user to create geometric constraints on every curve or point in the sketch, it finds the relationships for you and presents those relationships to the user when they go to select a piece of geometry to modify it, drag it, create a dimension on it, or any other type of manipulation that you do. So, the solver works instantaneously when the user selects something and presents those relationships in the terms of little symbols, similar to what we had with constraints in the past. And then the user is free to use what the solver presents – in almost every case, the solver gets it right. There are times when a drag operation needs to occur and the user has to relax or deactivate one of the found relationships. But that’s basically it in a nutshell; when a user selects something, the solver goes into action and finds the relationships for that operation that the user wants to perform.
Spencer Acain: I see. So, you mentioned that the solver gets it right almost all of the time, but then kind of implies that it doesn’t get it right 100% of the time, obviously. So, with that in mind, are you seeing any challenges with users adopting this new system, because it sounds like a big step forward or kind of a big change to how traditional CAD modeling practices are taught and sketching practices?
Mike Yoder: Yeah, it is a very big step forward. For the last three decades, users have been taught to fully constrain their sketches. What we’re offering now is a fully “constrained sketch” with dimensions only without the need to create those geometric constraints. And I’ll let Scott expand on this a little bit, but I think the biggest challenge that we’re having with customers is getting them to really unlearn what they’ve done for their whole life sketching, and really kind of let the solver take over and stop placing those geometric constraints in the system for everything that they believe needs it.
Scott Felber: That’s exactly what we’re really seeing. We’ve been doing this now for the last couple of years in production. A little before that, we did quite a bit of usability testing with customers and other people before that. It’s taking that step back and saying, “I need to take a new approach to what I’m doing.” It’s hard just for all humans because it’s human nature to not want to have to change. And what you really need to do is just reconsider what you need to do. And once you get through that mindset of “Hey, this is going to be different than everything I’ve been doing for the last little bit,” it is a lot better. We’ve all struggled with it from day one. I’m no different than anybody else because I was raised with the old sketcher. And at first, it took about a week or a week and a half to really understand what was going on. And once you do that, it naturally starts coming. And really to prove that point home is when we did our usability testing, we actually went to three or four universities across the United States, and we did it with people in design classes at the university level who have no preconceived notion for the most part of how MCAD tools are supposed to work. And that’s probably the one group we had the least amount of resistance with, because to them, they had no predefined notion of what they wanted to do. They’re like, “Well, I want to draw these lines. I want them to be like this, and I want them to move like that.” And to them, it just works right out of the box. Whereas with our existing customers, what we’re seeing is if you try to apply the old paradigm to the new tool, you can kind of run yourself into the ground pretty quick. So, it’s, like I said, taking that step back and saying, “Hey, what are we trying to accomplish here?” And just looking at it from that way. And then the other one is the confidence they have in the solver. Like we said, the solver will always pick all the constraints that exist in relations; it’s the users that need to have the conference in the results we’re presenting to them. Because up until this point in their lives, they had to do all that work. And as computing powers increased, and as algorithms and everything else we can create become more and more robust, we can do all those calculations for them. But they have to have confidence in the results we’re presenting to them. So, I think those are a couple of big things that we’re really trying to work on moving forward.
Spencer Acain: I see. So it sounds like you’re trying to overcome a lot of momentum in the industry of how things have been done to really innovate here.
Mike Yoder: Yes, that’s correct. We’re really shifting the paradigm of sketching into the future.
Spencer Acain: Oh, that makes sense that you’d be facing a little bit of resistance on that then. You also mentioned having confidence in the solver. Is that similar to how you would have trust in your smartphone or the Google searching algorithm to tell you stuff?
Mike Yoder: Yeah, that’s a pretty good analogy. People have been using smartphones for a decade now. Google has been out for, I’m not exactly sure how long, maybe two decades. And at first, the adoption was a little slow. But as people got used to it and got to trust it, and see how fast the Google Search works, and you get the results that you want immediately; the adoption takes off, and then it’s very widespread. One of our colleagues uses the analogy of getting into a self-driving car with the new sketcher. It’s the wave of the future, but not everybody wants to get into a self-driving car right now and let the car take over and drive them to a destination.
Spencer Acain: That makes sense. I could definitely see that taking a little getting used to; the idea of just sitting back and letting the computer do what it has to do without having to micromanage everything.
Scott Felber: Really, what we’re trying to see here with the confidence too, is, especially in something like mechanical CAD, where it’s very engineering and design-centric. And all of us that use tools like this, that were trained in colleges as engineers, we put a lot of thought and processes into what we’re trying to accomplish. And we think we can just do it, and we know we can do it because we have that confidence, because we’ve been doing it for years upon years, even in some cases, decades. So, when you say something new to an engineer, it is the confidence. And engineers will pry a little harder theneven places like earlier we talked about, using a smartphone. Smartphones are used across a spectrum of people, but engineers have a certain way of approaching problems sometimes; that’s what we learned in school is problem-solving. And they want to control the answer and the solution they get. So that’s really the thing we’re trying to get over the hump here on lately.
Spencer Acain: So, it’s kind of like, since engineers are trained with problem-solving, critical thinking in mind, they’re a little more critical of new and innovative technology. They want to know what’s under the hood. They come and say, “How does this work? do I have confidence in the result that this is giving me?” Is that kind of the issue you’re facing?
Scott Felber: That’s exactly, Spencer, in a nutshell.
Spencer Acain: Yeah, I can relate to that. I’ve been trained as an engineer myself. Can you tell us a little bit about some of the typical questions your customers are asking you about the new solver and the new sketching paradigms? Some of the big ones.
Mike Yoder: One of the first questions we get is, “Can I take a new sketch back to the old sketch?” And the answer to that is no, the solvers are so different, and we’ve put so much work into the new solver that, pretty much like any new CAD functionality, you can only move forward with it. So, if you have an old sketch that was created with the previous solver, you can bring it forward into the new one and it will convert all of those geometric constraints the user created into what we call persistent relations, which are very similar. But you can’t take a new one to an old one.
Scott Felber: One of the biggest questions we get, day one, especially in the first month of use is “How come I can’t find my relations?” And again, we try to explain that to people as “The relations do not exist until you go to make a change.” It’s not like the old traditional sketching where I created all these relations, I created this perpendicularity, I created these equal length.They just don’t exist, because they don’t exist until you need to make a change, and the solver goes into action and says, “Hey, I found perpendicularity. I found equal length. I found all that stuff and now I’m gonna honor that as you make that change.” And the other thing people sometimes struggle too within that concept is dimensions really are king over relations in the new sketch. So, if you change a dimension, it will figure out which relations it can override to accomplish that task. That is, I think, one of the day-one things that people need to rethink, and that’s one of the things we get a lot of questions on.
Mike Yoder: Another question alluded to this already, just to build on what Scott said is, when customers select a piece of curved geometry, they see the relations, and then they make the change, and they go away. And they say, “Why do my relations keep falling off?” Well, they didn’t fall off. If you remember earlier, when we started the podcast, we mentioned that they’re found instantaneously, and then they’re more or less discarded, and the sketch remains static after the move is done. If you select another piece of geometry, the solver goes into action immediately, finds those relationships, you make the change, and then when you’re done with the change, the sketches, static or frozen, if you will, until another change occurs. And so one of the hurdles that we’re seeing is customers aren’t exactly having the confidence that we wish they would have in it because those relationships come and go. And they’re having a hard time understanding that because of the way sketching has been done for the last 30 years, where you always see your geometric relations. They feel that if they can’t see those sketch constraints, then the geometry is going to move at will. And that’s not the case with our new sketching tool.
Spencer Acain: It sounds like you’ve made the process very dynamic, as opposed to the static way where you would define everything before. And now everything is just happening in real-time in the specific area that you’re considering or working on.
Mike Yoder: Yes, that is true. And like I said, once you’re done working, the sketch is solved and it stays there. Customers are, again, trying to get over that hurdle of just working with dimensions only, and trusting that the design and dimensions confine with their dimensions. And that’s really the heart of what the new solver brings.
Scott Felber: And yeah, Mike, along those lines of what you just said was one of the questions we see a lot is people talk about, “Well, what are my degrees of freedom on my sketch?” And because we’re not applying, because the users aren’t applying constraints, the concept of degrees of freedom; that was invented as part of sketching. If you go back to the old days of engineering where people just did stuff on paper, there was no concept of degrees of freedom. We just looked at the drawing, and it was fully defined. As we move into the computer world, this concept of degrees of freedom came about 30-40 years ago, and it’s moved forward. And what we do to help people alleviate that is we color-code the curves within the sketch now, as the curves that are fixed by the dimensions that have them in place are black, and the only way you can change this is by dimensions. And then there are brown curves, that’s out-of-the-box colors that have a different color, those are ones that are still movable if we just try stuff. Once we get a fully defined sketch, and that’s what people ask for – “How do I know my sketch is fully defined?” – it will let you know in the queue in the Status Line, say “Your sketch is fully defined.” That means it will only move by changing dimensions. And whichever dimensions you change, it’ll show you what we’ll have to do to do that. So, that’s one of the big changes that people look. The color coding is kind of, like you talked about, the instantaneous results, that really helps, to me, as I learned and move through it, I like the color coding. I know it’s curves, I still need to really put some dimensions on which ones are defined by the colors they are.
Mike Yoder: A couple of other questions that we get very frequently are, “Can I turn off relation finding? And can I fully define a sketch with persistent relations?” And if you remember, I mentioned that persistent relations are very similar to the old style constraints. So, these two questions go hand in hand. The answer is yes, you can turn off relation finding, but you’d be defeating the entire purpose of the solver and the benefit it brings. So, you can tweak it, so it won’t find a perpendicular or equal radius or equal length curve. But you’re really just making more work for yourself once you turn off relation finding. And then an example of fully defining a sketch with persistent relations. A user was having problems with a sketch, it was pretty simple, but he had almost 40 dimensions on a sketch, and almost 100 persistent relations. And the sketch was behaving correctly, but he was having some problems changing things. So, he sent the sketch to me, I looked at it, and first thing I did was delete all the persistent relations and looked at what the solver found. And it turned out, I needed to create 11 persistent relations, and then work with less than half of the dimensions that he had. So, I went from almost 100 persistent relations down to 11, and the sketch solved better and was easier to manipulate using the new solver to its full potential than over conditioning, if you will, with all the persistent relations and extra dimensions that you didn’t need. And when I was done working it, I had a fully defined sketch that I was able to modify inside the sketcher and outside the sketcher through the expressions that he created. So, I went back to the user and said, “To be blunt, you wasted a lot of time creating almost 90 persistent relations, when the solver would find all that information for you.”
Scott Felber: And Mike, that’s where the 30% saving comes from. Because if you think about that sketch, and you look at it, if I’m an end user and I’m going back to traditional SketchUp, the legacy sketch methods, and I have to create all those; if I have to create 90 relations, that’s going to be picking two items and picking the relation it is – so you’re saving almost 300 pics by not doing that. That’s where you get 30% savings. Someone went through and he created all that stuff in the new sketch, and you can do that and it’ll allow you to do it. But that was almost an extra 300 picks for a simple sketch that was probably like 20-30 curves if I remember correctly. That’s a lot of extra work. And that’s really what we’re saying the benefit is.
Mike Yoder: Yeah, that really hits home as when you start telling the user how many pickssomething takes, and you just made 300 extra picks.
Spencer Acain: That sounds like a huge strength with the new system, is that you’re cutting down the complexity and the busy even, and you’re just taking it back to a simpler state that still has all the same functionality.
Mike Yoder: Yeah, and actually, the new sketcher has more functionality than what the previous sketcher did. We’ve added some new dragging methods where you can drag rotationally. Scott mentioned the constant finding of movable curves that’s always on, that wasn’t present before. We have the ability to do patterns, mirrors, reflections, all associatively.For large sketches, we have what we call a work region. So, if you have 1000 curves in your sketch and you only want to work on a small area of it, you can window a small area, and the solver will ignore everything outside of that area. So you’re only connecting in the area that you need to do your modification in. So, it’s another tool that we did not have previously.
Spencer Acain: I think we’ve covered a few of these already. But are there any other strengths of the new sketcher that you’d like to highlight for us?
Mike Yoder: Probably the biggest one is the new dimensioning paradigm. All sketchers out there, rely on icons or commands that the user has to select first to create a dimension. With the new user interaction model we’ve created, all you simply have to do is two curves. The dimension appears, you select that dimension to keep it, and you can drag it around and modify it or turn it into an expression or a reference dimension, all with just a couple of clicks on a screen without ever using a toolbar or an icon.
Scott Felber: I think one of the other biggest strengths is the new workflow works. Westart with a clean sheet of paper what we call forward create. You’re creating a brand new design, all you need to do is just put down all your curves, you dimension on, and it just works. And I think when the people get the confidence in that workflow, that’s when they really excel and said, “This is the best thing we’ve ever seen.” That’s really where the strength that comes in, and we’ll callforward createfor the majority of sketching that people do every day for creating parts and features in their parts. It’s unparalleled fast. You can do it once you have the confidence in it and once you understand what it’s doing; just drawing lines dimensionally and go. And it just that is the strength of it more than anything.
Spencer Acain: We’ve talked about a lot here, but is there anything else of interest that you guys are working on within Siemens or even outside the company?
Mike Yoder: Well, we started a continuous release process, probably about two and a half, maybe three years ago, where instead of releasing software every year and a half or releasing it every six months. So, this has allowed us to bring new functionality, new applications, and much more aligned with what our users are looking for and what customers request. It’s allowed us to bring all this to market much faster than what we were before, and even what our competition does with having two releases a year. And if you look at some of the– I don’t have the numbers exactly, I think Scott knows these. But some of the enhancement numbers that we’ve added in and the patents that we’ve received since we started the continuous release process, it’s very impressive what we’ve been able to do. So, I’d say that our new release process, quality assurance, testing has been a really big benefit to our customers.
Scott Felber: Yeah, Mike, just to expound on what you just said, in the last year over the last couple of releases. Within the last one year, the NX team has delivered about 1400 enhancement requests based on customer inputs. Those are new things we put into software to make our customers that our customers asked us for, that’s what an “ask for a request” is. And the other one kind of goes back to where we started talking at the beginning about CAD being a– “It’s all the same. It’s not innovative. It’s old.” We don’t believe that because, in fact, in the last year, the NX team has been granted 43 patents around NX, which tells us we’re being innovative and we’re leading the way to help our customers get their designs done every day, and bring in new ways of doing that into the marketplace that the competition is just not thinking about because they’re being granted patents on that technology and those things we are doing.
Spencer Acain: That’s fantastic to hear that, how much innovation you guys are putting out there. But I think that’s all the time we have for this episode. Once again, I’ve been your host, Spencer Acain, and this is the Next Generation Design podcast. I’d like to thank Scott and Mike for joining me here today.
Mike Yoder: Yeah, thank you, Spencer. It was our pleasure.
Scott Felber: Thank you, Spencer.
Siemens Digital Industries Software helps organizations of all sizes digitally transform using software, hardware and services from the Siemens Xcelerator business platform. Siemens’ software and the comprehensive digital twin enable companies to optimize their design, engineering and manufacturing processes to turn today’s ideas into the sustainable products of the future. From chips to entire systems, from product to process, across all industries. Siemens Digital Industries Software – Accelerating transformation.