Smart manufacturing provides Closed-Loop Quality – Transcript ep. 4
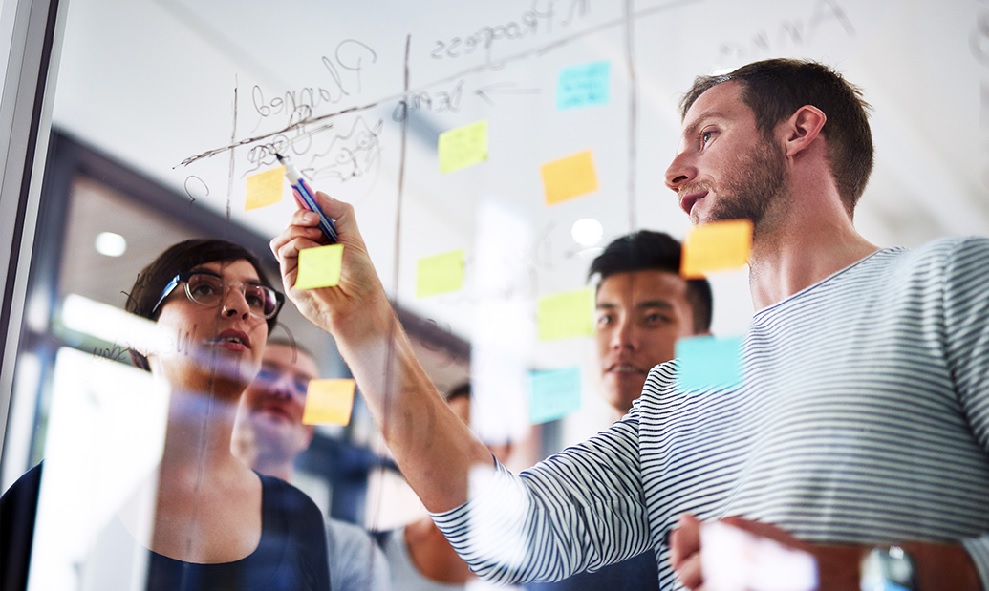
We have the privilege of speaking again with Rahul Garg, VP of the Industrial Machinery Mid-Market Program at Siemen Digital Industries Software. For this fourth Smart Manufacturing podcast episode, we are discussing the benefits of a Closed-Loop Quality to the factory, products, and processes.
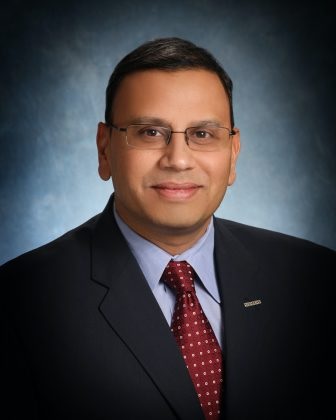
Learn how manufacturers are overcoming challenges in the industry by integrating quality into manufacturing, ensuring that they are taking advantage of digitalization and moving the entire quality process to the next level.
Listen to the audio podcast or read the transcript.
Read the transcript:
Chris: Hi everyone and welcome back to the Siemens Smart Manufacturing podcast series. I’m your host, Chris Pennington, the global industry marketing leader for industrial machinery at Siemens Digital Industries software. This episode is the fourth installment of our Smart Manufacturing podcast series. Our previous podcast covered closed loop manufacturing, discussing how it breaks down the barriers between design and manufacturing, including the CLM process and ERP and PLM systems.
We continue our discussion on closed-loop manufacturing technology, but shift our focus now to closed loop quality.
We’re privileged again to be joined by our expert Rahul Garg, Vice President for the Industrial Machinery and mid-market program at Siemens digital industry Software. Also, his 25-year career includes delivering global software-based solutions for product engineering and manufacturing innovation. He’s held leadership positions in research and development, program management, sales, and P&L management. He has had a focus on industrial machinery since 2007.
So, as we jump back into this topic on closed-loop manufacturing, let’s focus on quality. You previously stated that automation and digitalization could significantly reduce factory flow disruptions due to design changes, supply chain issues and changing requirements. And I’d like to elaborate in this area. So, I begin by asking why we need to integrate quality into the manufacturing process?
Rahul: So, Chris, thank you, again, I am very excited to talk about this very important topic for our customers. When you look at quality and the manufacturing process, it’s the Ying and the Yang, as one cannot exist without the other and it’s really the important aspect of ensuring that what gets manufactured has the right quality. It’s also ensuring that the products and parts are delivered on time and are through the correct specifications.
By integrating quality and manufacturing, we are making sure that we are taking advantage of digitalization and taking the entire quality process to the next level.
Chris: OK, excellent. So maybe you could provide an example of an application for closed-loop quality on the factory floor.
Rahul: Yeah. So first, let’s just take a step back, right. So quality is a well-defined term. It’s basically ensuring the product outcome is a meeting the original expectations. And when you look at closed-loop quality, the goal of closed-loop quality is ensuring optimization of your manufacturing process, identifying and correcting nonconformance early enough, minimizing scrap and rework, and improving the overall product to market.
Manufacturers are looking to accomplish these goals by accounting for quality in phases. If you will write a plan for quality up front, it is essential to look at all of your requirements for quality before you actually start building anything, checking against those well-defined capabilities and the expectations of the products defining where the failures could exist.
And then they’re finding additional details like how the how the machine should be run and operate it, right? So, even defining the environmental and conditions that can impact overall product quality and these conditions could be things like vibrations, temperature tolerances, machine condition and where and all of these must be monitored quite closely to ensure that the final product is delivering the expectations that customers have – so this is the upfront planning.
Then the second piece is monitoring the quality through the process. This is where you’re capturing the output parameters, looking at the as-built conditions against the requirements, and making sure that you’re closing the loop on the process to the source of the parameters needed. And if there are any deviations to this monitoring of the process of the production process, it becomes an important piece to be able to do that, taking advantage of IoT which provides this uninterrupted, unhindered data collection mechanism and provides the ability to monitor what’s, going on and provides that closed loop feedback to your manufacturing process. So, bringing these two pieces together, helps optimize your critical quality requirements and characteristics.
So, once you’ve got that, you obviously go through verifying your original requirements and the throughputs that are needed and making sure that you’re getting the quality expectations.
And where I I see maybe even a bigger challenge in today’s world is with the many disrupted supplier issues and the supply chain challenges like being able to monitor what’s happening and being able to track where your supplier parts are coming in can all have a big impact on your overall quality processes.
And finally, to close off on that, what we have seen is companies that have implemented closed-loop quality processes have been able to achieve a median product compliance rate of 99 percent with most of them performing between ranges of 97 to 100 percent.
And organizations without that capability, in our experience, had significantly more variability in performance with majority of them having performance between 90 and 98 percent.
So when you look at it, this disparity in performance could mean the difference between being first to market or being second to market and avoiding a major product recall or winning future contracts. So, what may appear as a small difference can have a significant impact on your overall business and we really do see being able to implement closed-loop quality can help.
It gets you closer to your final customer expectations. And one of the last points I would like to highlight is by implementing closed loop quality, you’re shifting quality related concerns to your entire organization. So, you’re making it into a shared responsibility instead of treating it as a disconnected or isolated process at the end. Therefore, by implementing this closed loop process, you’re trying to make sure that people who are up front in the design and engineering process are looking at the manufacturing process and it’s this closed loop process as well.
Chris: Yeah, sounds great. Those are some impressive figures there on those product compliance ratings. So, yeah, impressive. Would you say that quality is the overall goal of smart manufacturing and smart machines?
Rahul: Well, quality is one of the key pillars, and smart manufacturing and smart machines create more value for the manufacturing customer providing better quality and reliability. Also, obviously lowering costs, improving safety, less waste, and improving serviceability, right? So, it becomes a key contributor to the overall success, and then smart machines enable overall improved quality as well by eliminating nonconformance by detecting before they become issues and enabling appropriate changes to be made in near real time before they become big issues and avoiding any significant downtimes in the overall productivity process as well.
Chris: OK. Yeah, I mean OT is obviously critical to this whole thing and maybe you could provide some more examples of how deploying advanced technologies can result in improving quality.
Rahul: Yes. So, when you look at organizations that have integrated more advanced technologies into their machines and their factories, they gain value from the results in production machines, right? And some of these can be quite significant. So, an example of this is being able to customize to specific manufacturing needs. And one of our customers in Germany, collects and analyzes machine data and provides users with recommendations on how to optimize their machine operations. For example, it allows a configuration of their laser setting values or other process variables, thus being able to adopt that into their production processes where smart machines can help reduce maintenance costs by around 10 to 40 percent, and energy consumption by around 40 percent. So smart machines may itself decide to start and stop if it detects a potential issue with the product quality. For instance, in a gear production machine, the machine allows for an automated and continuous gear.
I’ll also bring up processes. It will continuously measure the tooth width of the machine work pieces, evaluate the measurements in real time, and adjust if necessary. So, it makes it very precise to make sure that it’s delivering the right product, and if necessary, make any stoppages in your production process. Therefore, it provides a very highly agile and adaptable process for customization and personalized goods.
And then the products, right? So, the smart machine becomes in charge of more and provides more substantial control as changes in the production process come into picture as well.
Chris: Yeah, impressive figures again. Obviously, maintenance costs are a big hit for many companies, but energy consumption shouldn’t be reducing by 40 percent. I think in today’s climate, that’s another important thing that needs to be considered. So, you know, maybe we could just look at what the main components are of the advanced technologies that provide these benefits.
Rahul: Yes, there are some key capabilities that one must consider, starting from something as simple as connectivity, historically. Companies relied on cables and wiring, and now today, with the 5G in the factory, it really enables a very high bandwidth bidirectional communication to and from the machine.
Another key component is AI (artificial intelligence) and machine learning. Artificial intelligence is crucial for efficient data processing, right? Despite the immense amount of information created on the manufacturing floor on which machines are running 24/7, generating a lot of data continuously which is necessary and so AI and machine learning are essential at multiple levels, providing that real value in getting the nuggets out.
The third piece is this whole challenge of IT and OT convergence which we spoke about in one of our earlier podcasts, which will play a key role in an organizations ability to respond in real time.
Lastly, but not the least, is this whole concept of a digital twin, which is very crucial for a factories and machines to provide that closed-loop operation. So, the digital twin will enable, during the design stage, for designing and commissioning and testing the machine, testing the production lines and then that facility in a virtual manner. But it also enables the factory operations to be monitored, providing predictive and preventive maintenance, and ensuring that your machines are running at the most optimized levels.
Chris: Excellent. Thanks for that. And I think I would like you to finish up by asking you to do a little bit of forecasting. So, what trends do you foresee in the next two to five years that will affect manufacturing and close-loop quality of our future factories?
Rahul: Yes, some of the key enablers that we spoke about earlier are obviously going to be critical. But there are other advanced technological capabilities that are all being considered very aggressively by many of our customers. IT and OT were just spoken about with robots and cobots, having a human interactive robot as well – they are going to become a big player. Also, hyper automation with more and more automation as reshoring happens and localization of production happens, hyper automation enables productivity impacts on the bottom line and fully integrated PLM systems that extend down the supply chain to suppliers and customers that ensure that all the way from the customer requirements, to the design, to the production shop floor, all connected and working effectively.
Chris: OK. Well, great conversation today. Raul. Thanks again for joining me in this fourth episode of our smart manufacturing series. It’s been a compelling conversation to learn a few of the details of close-loop quality and its advantages. And thanks to all our listeners for joining us. Please stay tuned for our final smart manufacturing episode on automated processes and have a great day.
Rahul: Thank you, Chris.
Xcelerator, the comprehensive and integrated portfolio of software and services from Siemens Digital Industries Software, helps companies of all sizes create and leverage a comprehensive digital twin that provides organizations with new insights, opportunities and levels of automation to drive innovation.
For more information on Siemens Digital Industries Software products and services, visit siemens.com/software or follow us on LinkedIn, Twitter, Facebook and Instagram. Siemens Digital Industries Software – where today meets tomorrow.
Related links:
Smart Manufacturing podcast 01 – Uncovering Smart Manufacturing
Smart Manufacturing podcast 02 – The Convergence of IT and OT in Digitalized Manufacturing
Smart Manufacturing podcast 03 – Uncovering Closed-Loop Manufacturing
Smart Manufacturing podcast 04 – Closed-Loop Quality