Leveraging digitalization to optimize aircraft maintenance
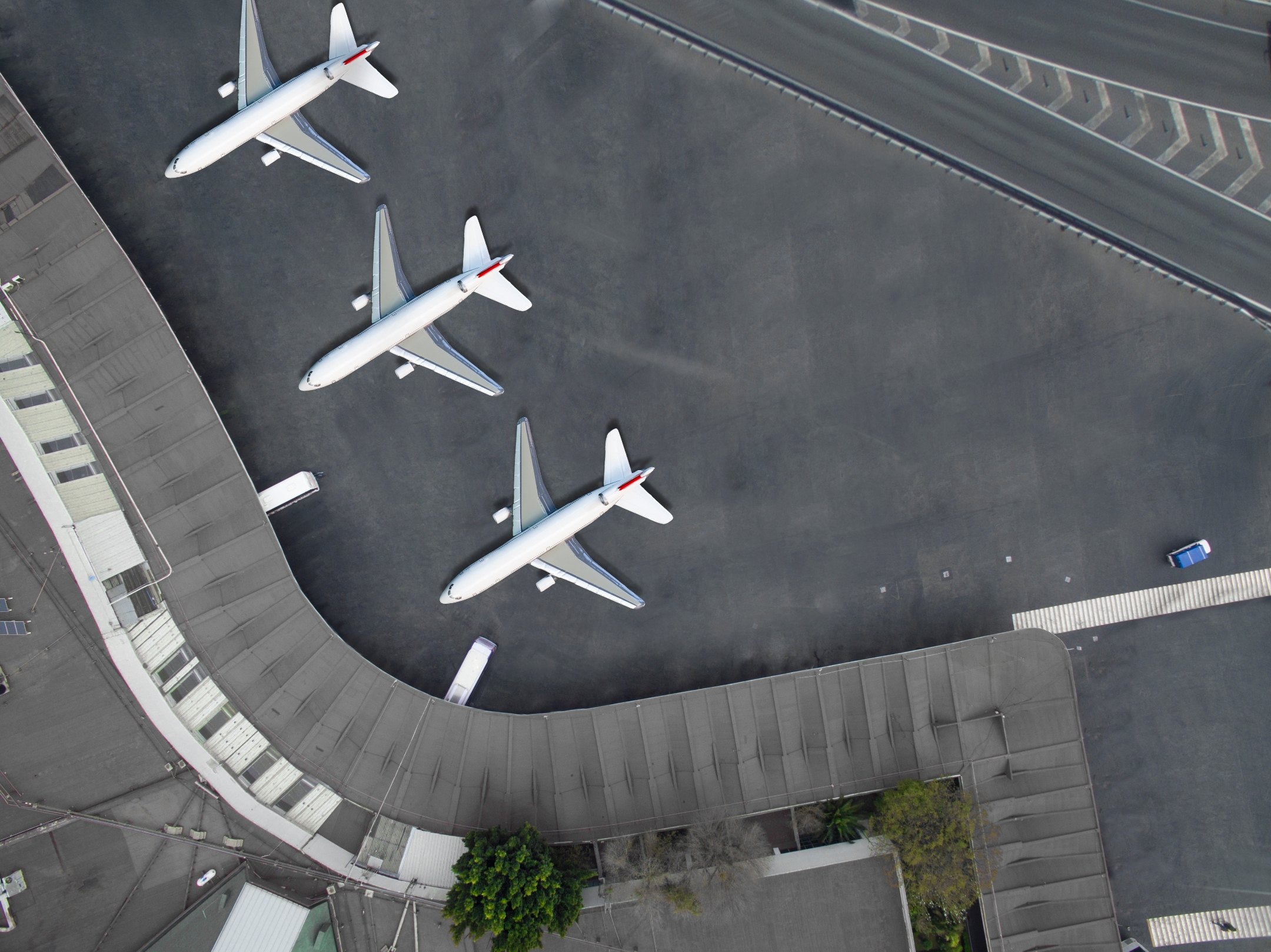
Maintenance plays a critical role in ensuring the operability and safety of all aircraft. For over eighty years, the procedures for aircraft maintenance—from documentation to distribution of data—have remained the same for the most part, largely because no alternative methods existed. However, recent advances in digital technology like the digital twin have changed that, offering new opportunities for aviation companies to improve how they perform maintenance. Digitalization offers new means to optimize aircraft maintenance procedures through model-based systems engineering (MBSE), improved knowledge capture, and predictive maintenance. These new approaches would hasten the production and access of maintenance-related information and track an aircraft’s conditions, making maintenance procedures more efficient.
One of the biggest advantages of the digital transformation of maintenance is the application of model-based systems engineering. Whereas traditional document-based systems engineering stores data for a product or process in separate documents isolated from each other, an MBSE approach centralizes product data around a virtual model, the digital twin. The entirety of a product’s data is instead coalesced as a single, accessible resource where everyone involved with the product can find the information they need. This is particularly important for service technicians working in aircraft maintenance since they will have to look up information on multiple components and procedures. With MBSE, all this data will be up to date and easily accessible from the digital twin, allowing technicians to begin work and get aircraft back into the air faster.
The benefits of accessing data from the digital twin are exemplified with how digitalization streamlines knowledge capture, the process of gathering and retaining knowledge from experts that could potentially be lost as they retire or move to new positions, to produce technical documentation. Technical authors, the individuals responsible for producing the documentation, have traditionally spent up to 40% of their time researching information rather than actually creating documentation. As mentioned earlier, this was due to a lack of alternative methods, but digital technology can now streamline the process by centering a product’s data around its digital twin. All the data a technical author needs can be easily accessed from the digital twin, letting them transfer 3D diagrams, repair procedures, diagnostics codes, and more to their documentation, drastically reducing the time needed for research. Additionally, the newly published documentation can be uploaded back to the digital twin, interconnecting all the documents with each other and making it easier for service technicians to access all the information they need for each step of maintaining an aircraft. Digitalization makes knowledge capture more efficient, resulting in the quick production of accurate, interconnected technical documentation and the streamlining of aircraft maintenance procedures.
Another significant feature digitalizing aircraft maintenance provides is predictive maintenance capabilities. While this approach is still being developed, predictive maintenance algorithms hold great potential for optimizing maintenance procedures by gathering data from aircraft while they are in operation thanks to smart technologies like embedded IoT sensors. This data is fed back into the digital twin, allowing engineers and algorithms to monitor the conditions of individual parts and products as a whole to determine exactly when an aircraft needs to be grounded. Using a predictive maintenance algorithm means aviation companies will not need to regularly ground aircraft for maintenance they may not even require. Instead, they can simply assign individual aircraft to maintenance whenever their data shows maintenance will be required. Predictive maintenance means aircraft will only need to be grounded when they actually need to be, better optimizing their maintenance-related ground time and keeping them in operation longer.
For decades, there have only been a limited number of ways to perform aircraft maintenance. With the advent of digital technology, however, newer, faster, and more efficient options are becoming available. If companies digitalize their aircraft maintenance procedures, they can streamline their data access and documentation production through MBSE and enhanced knowledge capture, allowing maintenance technicians to work faster. The power of predictive maintenance can also better optimize maintenance-related ground time, letting aircraft operate in the skies for longer. In an era where air travel is rapidly on the rise, digitalizing aircraft maintenance can help keep the aviation industry soaring.
Siemens Digital Industries Software helps organizations of all sizes digitally transform using software, hardware and services from the Siemens Xcelerator business platform. Siemens’ software and the comprehensive digital twin enable companies to optimize their design, engineering and manufacturing processes to turn today’s ideas into the sustainable products of the future. From chips to entire systems, from product to process, across all industries, Siemens Digital Industries Software is where today meets tomorrow.