How to take manufacturing to the next level with smart manufacturing
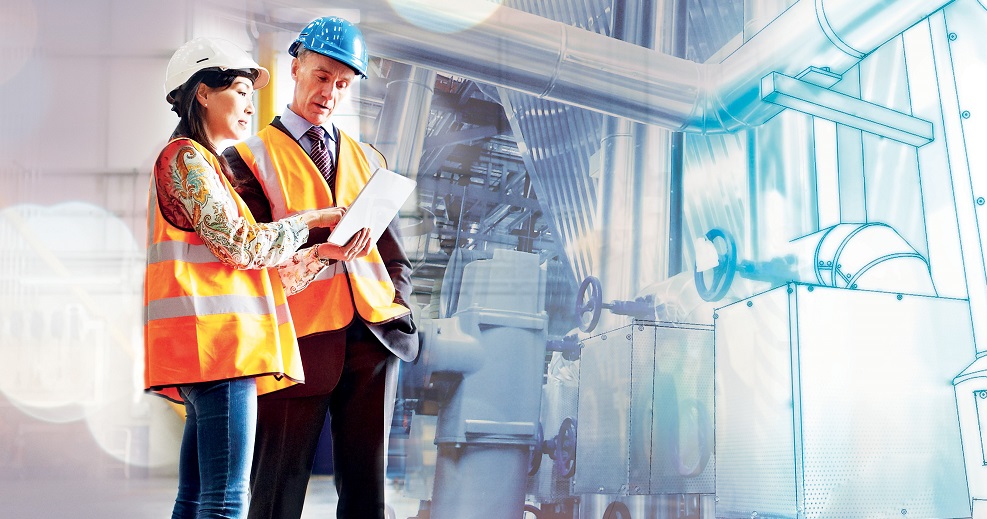
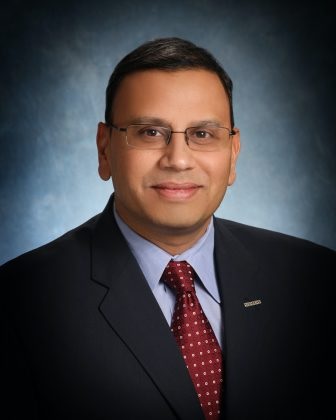
In a recent Industrial Machinery article, Rahul Garg, Vice President of Industrial Machinery, Siemens Digital Industries Software, describes innovative methods that are essential to address many challenges in the manufacturing industry. These hurdles include product complexity and emerging sustainability goals to meet consumer demands for greater customization. Concurrently, companies deal with global competition, supply chain and labor shortages.
Digitalization is the new equalizer that achieves a new level of smart manufacturing. Digitalization takes manufacturing processes to a new level, delivering more and better data—crucial for improving operational efficiencies to achieve benefits:
- High availability.
- Maximized factory utilization.
- Real-time management of supply chains.
- Improved time to market.
The key capabilities digitalization supports that lead to smart manufacturing includes:
Convergence of information technology (IT) with operational technology (OT).
This leads to greater flexibility and visibility into operations, empowers better decisions in an integrated manner and provides real-time process monitoring of the shop floor. Also, it encourages collaboration across planning and scheduling. Lastly, it applies artificial intelligence and machine learning to large data sets, uncovering non-conformance and non-regular data to make decisions quickly.
Enables closed-loop manufacturing (CLM) and execution that focuses on creating and optimizing the process and expediting customer orders.
CLM synchronizes and optimizes production across product design, production planning, manufacturing execution, automation, and intelligence from consumer use in the field. Engineering teams will receive timely manufacturing feedback to expedite problem resolution and ensure optimal product evolution. Also, it allows tracking of what the data built, how it was made, and the materials and parts used.
Ensure products are delivered right the first time, regardless of lot size, through closed-loop quality.
Quality is a well-defined term in manufacturing when the product outcome meets the intended expectations for product performance and features. Therefore, the goal is to deliver the intended quality for every product manufactured. CLM provides crucial real-time quality data that enables manufacturers to adjust the processes to optimize quality in real-time continually. Also, it identifies parameter trends and their sources to allow adjustment at the first available downtime. As a result, organizations that establish closed-loop quality processes achieve a median product compliance rate of 99 percent, with a majority performance ranging from 97-100 percent.
Smart manufacturing supports the concept of a digital twin of the manufacturing environment – a game-changer for manufacturers positioning themselves for the future. It is a virtual, digital replica of the physical objects of a machine or manufacturing system or the shop floor in a digital environment. The digital twin provides a physically accurate simulation that combines the virtual and physical worlds while the factory operates. Data analytics and AI offer new insights and efficiencies for product manufacturing. The goal ultimately leads to the triple zero in manufacturing: zero downtime, zero defect, and zero harm.
Siemens Xcelerator, the comprehensive and integrated portfolio of software and services from Siemens Digital Industries Software, helps companies of all sizes create and leverage a comprehensive digital twin that provides organizations with new insights, opportunities and levels of automation to drive innovation.
For more information on Siemens Digital Industries Software products and services, visit siemens.com/software or follow us on LinkedIn, Twitter, Facebook and Instagram. Siemens Digital Industries Software – Where today meets tomorrow.
About the author
Rahul Garg, Vice President of Industrial Machinery, Siemens Digital Industries Software, responsible for defining and delivering key strategic initiatives and solutions, and global business development. He and his team are responsible for identifying key initiatives and developing solutions for the industry while working closely with industry-leading customers and providing thought leadership on new and emerging issues faced by the machinery industry. Rahul’s experience and insight are derived from a 25-year career delivering software-based solutions for product engineering and manufacturing innovation for the global manufacturing industry, spanning a career in R&D to program management, sales and P&L management and having focused exclusively on the industrial machinery and heavy equipment industry since 2007.