Deloitte, Siemens and the Model-Based Enterprise: The Future of the Digital Twin
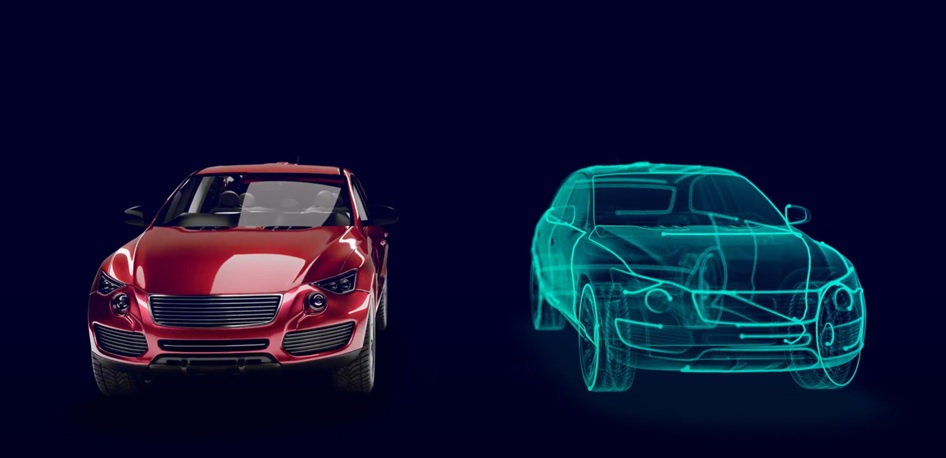
What Can a Digital Twin Do?
Before we can explore the full functionality and benefits of digital twins, it is important to understand exactly what digital twins are and how they can be applied throughout the operational lifecycle. A digital twin is, as the name suggests, a virtual model of a physical object or system that can be used to simulate the behavior of that object or system to better understand how it works in real life.
At present, the most commonly used type of digital twin is a product digital twin. These twins allow product development teams to create a complete digital representation of an item, even before a physical version exists. Engineers can build digital twins to the mechanical, electrical, and software requirements of a product in development and simulate its performance under various conditions as the work to optimize design. Digital twins also allow engineering teams to improve, among other things, the reliability, manufacturability, testability, and safety of their products by “designing for x.”
Digital twins can also replicate shop floors and entire supply chains. Just as product digital twins represent the behavior of a specific item, these digital twins can simulate how complex systems operate. This gives stakeholders powerful insight into how effective these systems are and even helps companies redesign them to optimize their efficiency.
In addition, digital twins can mirror a company’s service process, giving them visibility into how equipment performs in the field and allowing them to predict service and maintenance needs.
Taking Digital Twins Out of the Silo
Given the benefits digital twins can deliver, it’s no surprise that so many companies are using them in some way. In the fall of 2021, a Deloitte study* indicated that 85 percent of respondents were utilizing digital twins—or at least strategizing around their use—in some capacity. But how much value are they deriving from those efforts? The study findings indicate that it is considerably less than it could be. In fact, only 15 percent of respondents reported using digital twins from one end of the product lifecycle to the other. Five percent are using them on the shop floor, and less than five percent use them in service and maintenance.
Even in a silo, digital twins can reduce costs by between 20 and 30 percent. But those savings only occur within that particular silo. By bringing together the different types of digital twins as part of a model-based enterprise (MBE), however, companies can lower total costs by between 50 and 70 percent. An MBE makes those kinds of savings possible by removing barriers between aspects of the product development lifecycle and creating all-encompassing views of the processes that drive it. Stakeholders can view and share critical data seamlessly, reduce cycle times, and develop higher quality products more quickly, all of which reduces operational friction and improves efficiency, not only within particular silos, but throughout the company.
As computing power increases and 3D printing technologies improve, MBEs will also allow for the introduction of more innovative, cost-effective designs. In fact, we’ve already seen some of what MBEs can do with the rapid production of personal protective equipment (PPE), vaccines, and prosthetics for children.
Deloitte and Siemens: Guiding the MBE Transformation
Increasing efficiency, lowering costs, and doing good in the world are all outcomes worth pursuing, and they are all possible with an MBE. But reaching those outcomes requires more than technology—it requires the reimagining of processes and ensuring that those within an organization are equipped to utilize a new system and take advantage of the opportunities it presents.
That’s where Deloitte and Siemens leverage their experience to help companies align the three core aspects of any digital transformation effort: technology, people, and processes. That alignment is essential to any organization that wants to derive the most value from an MBE.
The value an MBE creates is on full display at The Smart Factory @ Wichita on Wichita State University’s Innovation campus, where Deloitte and Siemens have joined together to showcase the depth and breadth of what is possible with an MBE. Within this facility, Siemens developed the dedicated eXplore Live space as 3,000 square-feet of hands-on learning opportunities for companies looking to modernize, reshore, localize, or regionalize their operations in North America. Visitors see demonstrations for how digital solutions, including digital twins, can enable manufacturers to drive new business models, improve product quality, boost productivity, and become more sustainable. The broader factory experience features a fully operational production line and labs dedicated to the exploration of factory innovations. In short, it’s a space that is defining what cutting-edge means for today’s manufacturers and establishing what the future of manufacturing will be.
Conclusion
Digital twins may not be a brand new technology, but it is safe to say that most organizations have only begun to scratch the surface of what they can do, especially when freed from organizational silos and integrated to create an MBE.
By creating a single source of truth visible across an organization, companies can unlock far greater efficiency and cost savings than by using digital twins in isolation from one another. The advantages of this step are clear: better products can be made more quickly, data can be more easily shared between teams within the organization, and project timelines can be sped up.
But digital twins and MBEs are not magic wands. To maximize their potential, companies must ensure that their team members understand the technology and can use it effectively. They must also ensure that the required process changes are understood and implemented across the organization. Anything less risks losing out on everything these technologies make possible.
Deloitte and Siemens can ease that transition and put companies in a position to realize as much value as possible from an MBE. We would love to discuss how we can transform your organization.
View the video recording of Model-Based Enterprise Now, Near, Far. In this video you’ll hear from Brian Meeker, Product Strategy & Lifecycle Management practice leader at Deloitte Consulting LLP, and Del Costy, Senior Vice President and Managing Director, Americas, for Siemens Digital Industries Software, on how to become a Model-Based Enterprise.
To learn more about the Siemens and Deloitte Alliance:
Please contact Brian Armstrong
Strategic Partner Manager, SIEMENS