The Drivers of Sustainability in Industrial Machinery
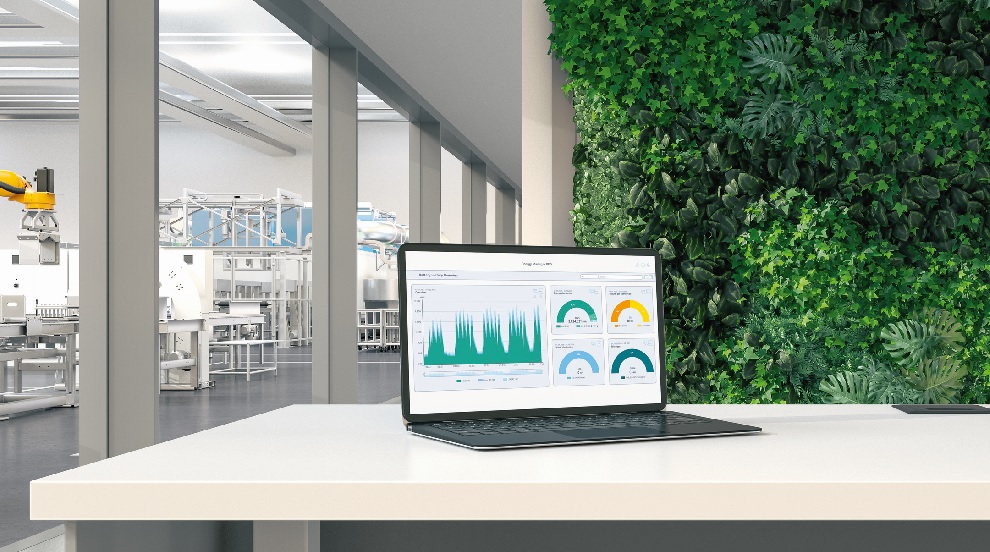
A sustainable factory is a must in today’s competitive marketplace. Companies want to know that their machines, process, and delivery are sustainable for the environment and the overall lifecycle and costs.
Four key issues are driving the need for sustainability in the industrial machinery industry:
- Commitments, reporting and compliance are driven by regulatory bodies, government bodies and others.
- Capital flows to where money is being invested in driving smarter factories and smarter sustainable factories.
- The social aspect is the resource scarcity at the end of the day. We all have some obligations in trying to manage a better manager.
- Customers are demanding that equipment providers make their equipment more sustainable.
These drivers specify the need for industrial machinery companies to change how they view sustainability as essential and imperative to their business strategy moving forward. As a side note, you can also see how the need for electrification is driving the prerequisite for efficiency because so many of these processes require energy density that is only available in a fossil fuel, which is not the same way in electricity. So, there’s the need to drive down the energy used in a factory to convert materials that require evaluation and optimization.
Remember that the end objective is not merely a reduction in emissions from energy consumption of fossil fuels but also energy cost, which is on the rise. Therefore, there is the motivation to optimize that cost.
Digitalization drives sustainability
Siemens combines the real and the digital world. Digitalization drives sustainability. Therefore, sustainability is an outcome that requires lots of planning and many tools to make it happen. Digitalization provides the opportunity to look at the entire product lifecycle, taking data from many different phases and visualizing it. This process allows you to try various scenarios as you run through simulation tools. It provides an environment where you can try many different variables, pulling things together within the context of digitalization, thus providing the ability to exchange data.
When you can view everyone in your value chain and ecosystem, there is much success with sustainability coming from people collaborating, exchanging data, sharing information, working together, and defending standards across competitors, moving forward into the entire area.
In the past, digitalization was viewed as helping a company to become a digital enterprise so they could be more adaptable, agile, and flexible to improve their ability overall to deliver the product within the right time, quality, and cost.
However, leveraging digitalization for energy efficiency, decarbonization circularity, and resource efficiency is bringing it all together comprehensively for our customers. It’s an evolutionary process. Digitalization provides the tools to make it palatable and executable.
So, as the scenarios become more complicated with more and more outcomes, we also provide digital tools and enablement to make it manageable moving forward. Managing or building in a complex environment can become more challenging; therefore, digitalization offers the tools to make it easier.
It also allows you to view the whole value chain and the entities in that chain working together to move it forward and find pain points universally and holistically to work together to address them. It provides a safe, secure exchange of data that allows people to visualize it across the entire lifecycle of a product, the production line or production facility. There are significant data implications for the industry and how those feed both traditional and sustainable outcomes.
Optimizing the design process
When optimizing the design process using digitalization tools, you’re looking at the cost of the part from a supplier, the carbon footprint of that part, and the carbon footprint that the supplier may have in delivering that part to your factory or location. All of these are factors that can be evaluated upfront via digitalization tools.
This process provides the ability to perform evaluation and analysis in the realization phase when planning a product’s design and the machinery that will manufacture it. This is the perfect time when you can decide about energy-efficient equipment and how long that product will last. We hear people talk of brownfield factories, but there are also brownfield designs (existing designs that you are trying to make more environmentally friendly), which are more complex than starting fresh with the information you need to make them environmentally friendly from the beginning.
Learn more on this topic from our Sustainability Podcast series with Erin Devola, Head of Sustainability at Siemens Digital Industries Software, and Dale Tutt, VP of Industry Strategy at Siemens Digital Industries Software,
Software solutions
Siemens Digital Industries Software helps organizations of all sizes digitally transform using software, hardware and services from the Siemens Xcelerator business platform. Siemens’ software and the comprehensive digital twin enable companies to optimize their design, engineering and manufacturing processes to turn today’s ideas into the sustainable products of the future. From chips to entire systems, from product to process, across all industries. Siemens Digital Industries Software – Accelerating transformation.