The last step in PCB design needs more attention
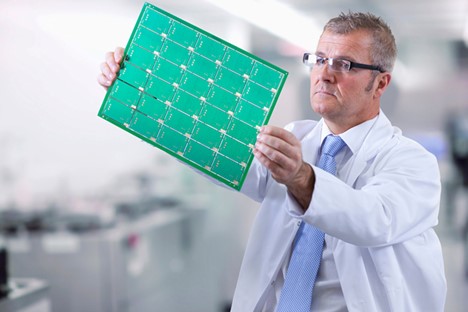
Why is it that the last step in a process always gets short-changed?
We put a lot of attention on the first step of a process and then it seems we fall behind schedule. By the time you get to the last step of a process you are out of time and just need to wrap things up. How often are you pressed by management to get a PCB design out the door and sent to the fab house? If you’re like most companies, it’s virtually every design. And that means that one of the most important steps in the release process is not given the attention it deserves. That step is PCB panelization.
I’m not talking about the fabrication panelization that the board house uses in production. That one requires venting and thieving patterns as well as scaling and etch compensation factors to be applied. The panelization I am speaking of is the assembly panel you are responsible for defining. This is the array you expect back from the fabricator that will then be sent to assembly. Unless you only design very large PCBs that are fabricated one per fabrication panel, your company can benefit from assembly panel design optimization.
In this whitepaper, Lowering PCB Costs with Material Utilization, you’ll learn how even companies doing small volume production can benefit from panel optimization in as few as four panels. On top of that, the right solution can even help you avoid quality issues you might not be aware of through the use of panel-level DFM.
Download the free white paper “Lowering PCB Costs with Material Utilization”>>